Si Audi Brussels a l’honneur de produire la première Audi e-tron entièrement électrique, c’est parce que la direction allemande d’Audi lui fait confiance. Le mérite revient aussi aux travailleurs du site belge, brillant par leur motivation et leurs compétences. Même si l’usine est une ‘no go zone’ en raison du caractère ultraconfidentiel du projet e-tron, nous vous proposons une plongée dans les coulisses.
Lisez ici tous les articles sur l’électromobilité.
Dans quelle mesure est-il difficile de garder les curieux à l’écart ? Cette question, nous l’avons posée à Jan Maris, chef de production chez Audi Brussels. ” Le site emploie 2.000 collaborateurs et des sous-traitants arrivent et repartent sans cesse. Vous pouvez imaginer qu’il est particulièrement difficile de garantir un secret absolu. L’usine est subdivisée en trois zones. Chaque zone possède une couleur qui définit les règles de sécurité en vigueur. Dans les ‘zones rouges’, les collaborateurs doivent verrouiller leur smartphone et les visiteurs occasionnels doivent laisser leurs effets personnels dans un casier. Les instructions sont claires : vous pouvez regarder, mais pas toucher ou photographier ! “
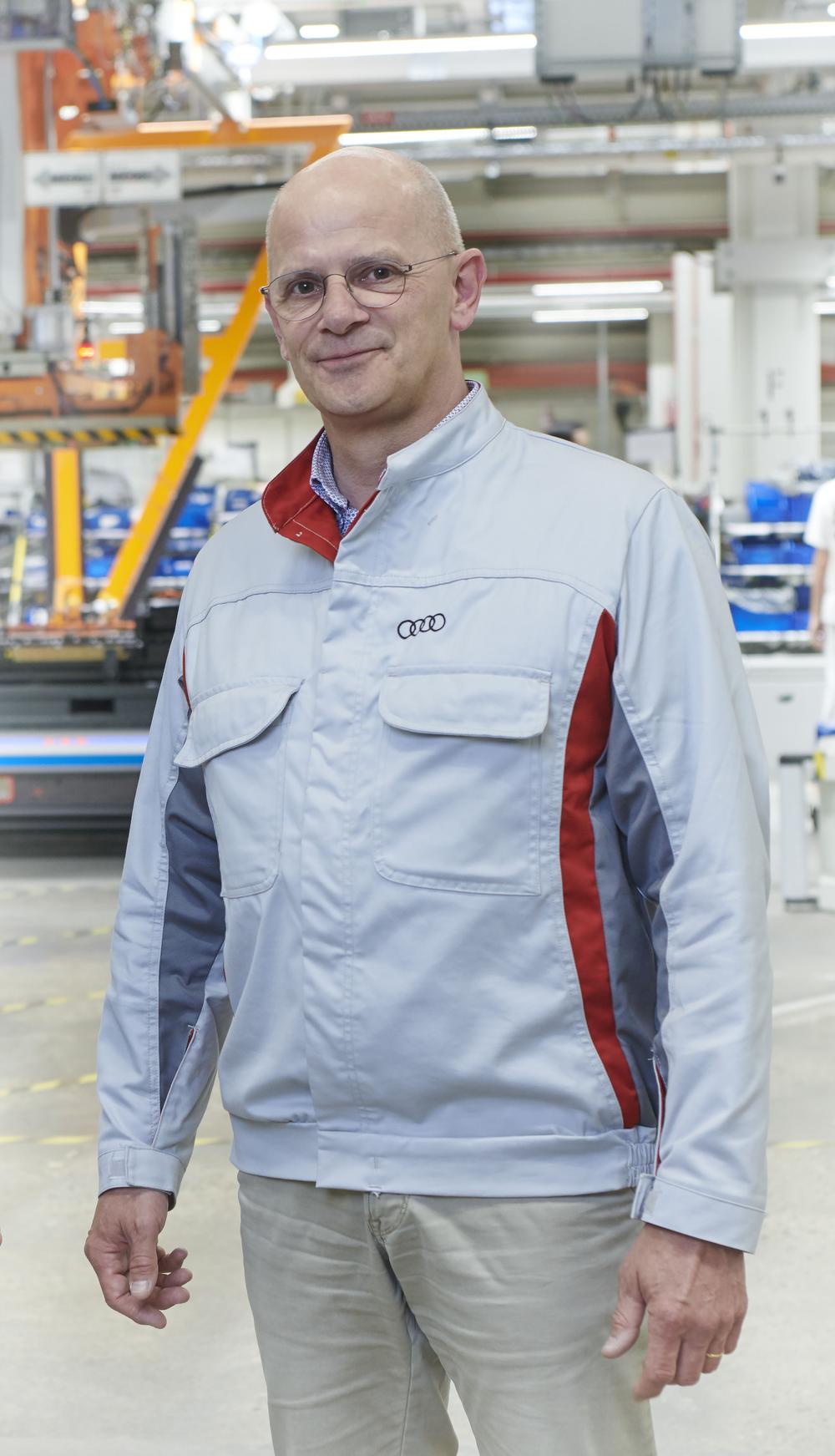
Une usine sous haute tension
L’arrivée de l’e-tron électrique marque le début d’une nouvelle ère pour Audi, mais aussi pour l’usine de Forest, qui devient l’usine pilote pour les futurs e-projets de la marque. Et cerise sur le gâteau, elle possède sa propre usine de batteries, ce qui permet de produire sur une seule et même ligne les batteries et les carrosseries. Pour la transformation de l’usine, qui a coûté 600 millions d’euros, la quantité d’acier utilisée est identique à celle constituant la Tour Eiffel. La production affiche un bilan CO2 totalement neutre : l’énergie est fournie par une centrale hydroélectrique et 37.000 m² de panneaux photovoltaïques sur les toits de l’usine. L’usine Audi de Forest dispose ainsi du plus grand système photovoltaïque de la Région bruxelloise.
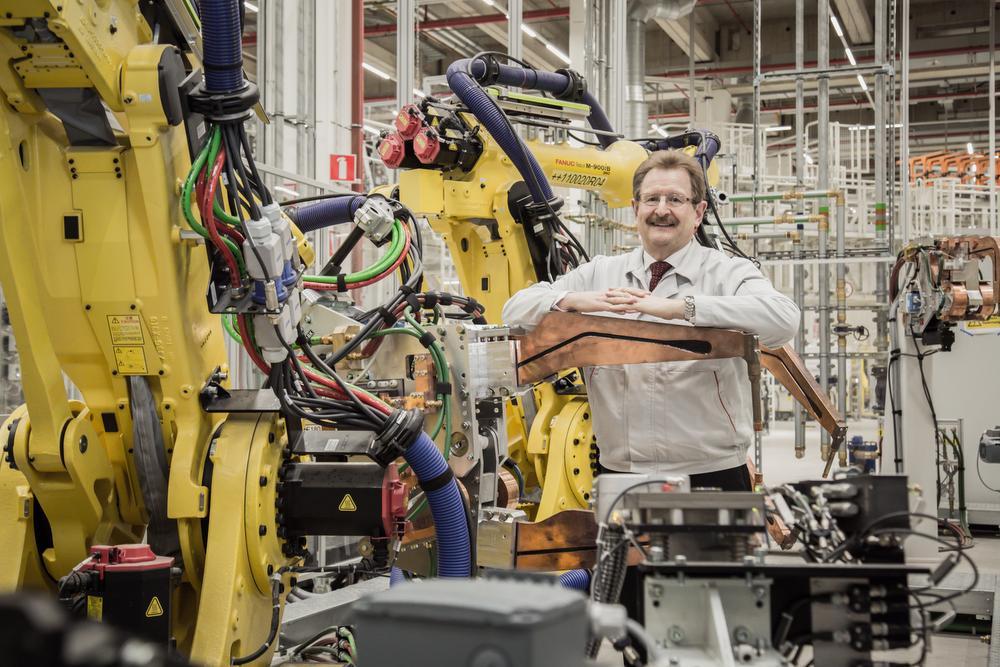
Patrick Danau, directeur de l’usine : ” Nous avons profité de la transition vers la technologie haute tension pour passer aussi à l’énergie durable. C’était tout simplement logique. Nous vivons désormais dans un monde nouveau pour lequel nous n’avons pas encore de cadre de référence. Nous avons créé notre propre institut de formation, où nos collaborateurs apprennent à gérer cette nouvelle technologie. “
Nous avons créé notre propre institut de formation, où nos collaborateurs apprennent à gérer cette nouvelle technologie.
” Le travail sous haute tension doit parfois être pris au sens propre du terme. Les dispositifs et les mesures de sécurité sont destinés à garantir une protection maximale contre les accidents du travail. L’utilisation de robots permet d’automatiser entièrement de nombreuses phases de production des batteries. Il n’y a plus d’intervention humaine et donc plus aucun risque pour les collaborateurs. “
Avenir garanti
La décision de confier à Audi Brussels la production du premier SUV électrique d’Audi démontre l’énorme confiance de la direction allemande d’Audi envers les compétences et l’implication des collaborateurs de l’usine. Patrick Danau : ” La question centrale était de savoir si cela avait encore du sens d’avoir une production industrielle dans notre pays. Nous avons mené des discussions en profondeur sur ce thème avec les autorités. Ces débats ont permis de montrer que le monde politique était prêt à nous aider pour optimaliser les investissements dans le cadre légal et à nous soutenir en mettant en place des formations pour les travailleurs moins qualifiés que nous employons. “
Un investissement de 600 millions d’euros, c’est un investissement sur le long terme qui s’inscrit dans un grand plan stratégique. Et dans ce plan, notre usine assume un rôle de pionnier.
” Ces promesses concrètes ont été décisives aux yeux de la direction en Allemagne. L’avenir d’Audi Brussels est-il pour autant assuré ? Un investissement de 600 millions d’euros, c’est un investissement sur le long terme qui s’inscrit dans un grand plan stratégique. Et dans ce plan, notre usine assume un rôle de pionnier. ” Voilà qui est clair et qui ravira sans nul doute les travailleurs de l’usine Audi de Forest.
Audi Brussels produit sa propre batterie
” La production d’une batterie à haut voltage était quelque chose de tout nouveau pour Audi et les défis étaient nombreux “, explique Wim Verbeiren, Head of Health & Safety, Security and Environment chez Audi Brussels. ” Aujourd’hui, Audi Brussels possède le savoir-faire et les compétences grâce à la bonne chimie entre le pragmatisme belge et le ‘Gründlichkeit’ allemand. La batterie est un composant essentiel d’une voiture électrique. Nous avons résolument choisi de la produire en interne. Sur la base des cellules fournies par notre sous-traitant, nous produisons une batterie à haut voltage complexe 100% Audi. Au terme de leur vie, nos batteries peuvent être facilement recyclées ou utilisées à d’autres fins. Elles sont ainsi parfaitement adaptées pour un usage domestique afin de stocker durant la journée l’électricité produite par les panneaux solaires d’une maison et l’utiliser durant la nuit. Pour nos batteries, il existe une vie après la mort ! “