Moins flamboyant que Tesla, moins tonitruant que le groupe Volkswagen, BMW suit son propre chemin dans l’électrification de ses véhicules. La marque mise sur la conception des cellules des batteries, l’élément clef de l’automobile à électrons.
C’est à Parsdorf, dans la banlieue est de Munich, que BMW a ouvert une usine d’un genre particulier, un maillon dans l’électrification des voitures de la marque bavaroise. Une chaîne de fabrication de cellules a été mise en place. Ces cellules, ou accumulateurs électriques, sont connectées entre elles et sont les éléments de base d’une batterie. “Nous avons construit cette usine pour étudier leur processus de production”, précise Milan Nedeljković membre du comité de direction de BMW AG, en charge de la production.
Cette étape prépare l’arrivée d’une nouvelle génération de modèles électriques, appelée Neue Klasse, à partir de 2025. Elle utilisera des batteries dotées de nouvelles cellules au lithium ion, élaborées par BMW et dont la fabrication est testée dans l’usine de Parsdorf. Elles ont une forme cylindrique de 96 mm de hauteur et de 46 mm de diamètre.
Lire aussi | BMW devient la marque automobile la plus durable
“Avec un potentiel de 20% de densité énergétique supplémentaire et 30% d’autonomie de plus que les cellules habituelles”, ajoute Milan Nedeljković Et un coût de 40% de moins! Avec cette nouvelle technologie, le chargé de production estime même que les batteries BMW surpasseront celles des Tesla. Elles permettront aux futures Neue Klasse d’atteindre une autonomie de 1.000 km.
Concevoir et non fabriquer
Contrairement à Tesla, dont la politique est suivie par plusieurs autres constructeurs automobiles, BMW ne cherche pas à investir dans la fabrication en grande série des cellules. Le groupe allemand n’estime pas cette activité particulièrement stratégique. Seule la conception de ces cellules lui paraît cruciale, différenciante. Il s’inscrit ainsi à contre-courant de ses concurrents.
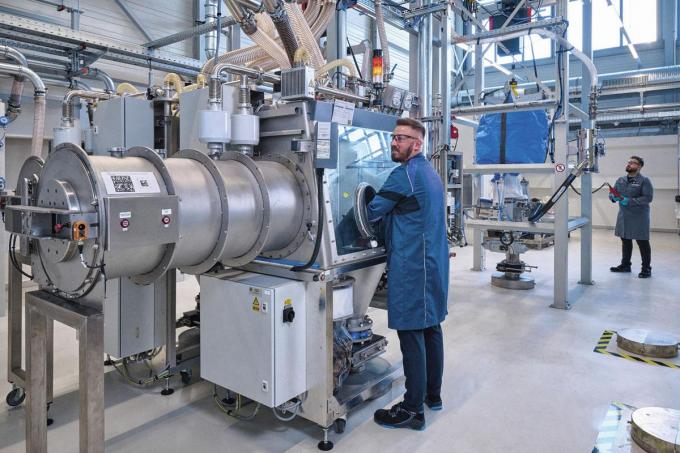
“Divers constructeurs automobiles européens ont établi des partenariats stratégiques avec différentes parties prenantes de la chaîne de valeur des batteries pour avoir accès à des cellules en quantités suffisantes et de haute qualité”, explique Jean-Marc Timmermans, senior business group leader manufacturing pour la mobilité chez Agoria et qui a lui-même poursuivi des recherches dans le domaine des batteries à la VUB. “C’est le cas, par exemple, de la coentreprise Ionway, de PowerCo (Volkswagen AG), avec Umicore pour la production de précurseurs et de matériaux de cathodes, des éléments essentiels à la production des cellules.”
Renault sous-traite la conception des cellules à ses fournisseurs sur base de cahiers des charges. Parmi eux: LG, Envision et Verkor, Renault ayant même pris une participation dans ce dernier. De son côté, le groupe Stellantis est aussi actionnaire d’usines de cellules en France (ACC, avec Saft et Mercedes) et aux Etats-Unis.
On l’a dit, pour BMW, l’élément clef, c’est la conception même de la cellule, et non sa production en série. “Nous n’avons pas de participation dans des joint-ventures pour fabriquer des batteries. Ce sont des relations de fournisseur-client”, précise Milan Nedeljković. Des fournisseurs très encadrés, dont CATL ou Samsung, en Europe, aux Etats-Unis et en Chine, selon les marchés visés. Ils construisent les cellules avec des matières premières achetées par le constructeur selon les recettes et le processus de production (breveté) mis au point et testés par BMW dans l’environnement ultra-propre (comme pour la fabrication de microprocesseurs) des installations de Parsdorf.
Si le moteur est un élément différenciant pour les voitures à carburant, ce sont les cellules des batteries qui déterminent à la fois le coût, l’autonomie et la vitesse de charge pour la voiture électrique, des éléments essentiels pour les clients. “Le développement des cellules de batterie est très dynamique. Nous voulons fournir aux clients le dernier cri en la matière, ce qui implique de développer notre propre technologie pour les batteries. D’où ce centre de compétences dans le manufacturing et nos efforts pour communiquer cette connaissance au fabricant qui nous les fournira.” La conception des nouvelles cellules inclut évidemment la question de leur recyclage. “Aujourd’hui, pour la cinquième génération, nos cellules sont conçues pour pouvoir être recyclées à plus de 90%, et même 95% en fait.”
Lire aussi | La stratégie d’électrification de BMW
Qui a raison dans son approche stratégie de la transition électrique? “BMW est un constructeur très prudent sur la question de l’intégration verticale. Il veut s’impliquer dans la technologie mais pas fabriquer lui-même les cellules. C’était très clair dès le début. Avec des ambitions de baisse de coûts semblables à celles de Tesla”, explique Philippe Houchois, analyste du secteur automobile à la banque Jefferies, qui note en passant que Tesla n’a pas réussi à monter en cadence sur leur technologie cylindrique.
“Tesla a peut-être promis trop vite, BMW est plus lent et plus prudent, poursuit-il. L’approche de celui-ci n’est pas mauvaise car la technologie progresse rapidement et la rentabilité de la production de batteries reste très incertaine. Il y a un coût de capital énorme et des marges faibles, comme on le voit chez CATL. A présent, les constructeurs pensent à remettre en cause l’intégration verticale, alors que BMW n’a jamais suivi cette voie.”
Plus de 15 ans de recherche
Se concentrer sur le développement des cellules exige des moyens. “C’est une manière de se différencier, une marque comme BMW a besoin de le faire pour créer une différence dans un métier où il n’y en a pas beaucoup”, continue l’analyste. Cela fait un bon bout de temps que BMW s’intéresse à l’électrification de ses véhicules. “Nous avons démarré la recherche sur les cellules il y a 15 ou 20 ans, déclare Milan Nedeljković. A chaque génération, la performance s’est fortement améliorée.” La pile cylindrique constitue la sixième génération. La véritable entrée sur le marché grand public remonte à 2013 avec la BMW i3. A présent, le groupe électrifie méthodiquement sa gamme, lentement mais sûrement, en y mettant les moyens.
Lire aussi | Quelle est la voiture électrique la plus écologique?
Il a joué un rôle de pionnier en lançant la i3 en 2013, mais le succès moyen de ce modèle a manifestement incité le constructeur à ne pas aller plus vite que la musique et à prendre son temps pour proposer des modèles électriques premium qui ne font pas trop regretter les moteurs à carburant fort appréciés de la marque. Le groupe Volkswagen, lui, a été plus rapide à sortir des modèles basés sur des plateformes conçues exclusivement pour l’électrification, avec la famille ID (ID. 3, ID. 4, etc.), les Audi Q4 e-tron, la Cupra Born, la Skoda Enyaq, mais il rencontre un trou d’air actuellement.
Aujourd’hui, la plupart des constructeurs perdent de l’argent en produisant des véhicules électriques, hormis Tesla. Les modèles actuels de BMW sont généralement conçus sur des plateformes mixtes qui peuvent aussi comporter des moteurs à carburant, rentables selon BMW. Le premier modèle basé sur une plateforme purement électrique sortira avec la génération Neue Klasse, en 2025, au format des BMW Série 3, en SUV comme en berline.
Batterie solide dès 2030?
La plateforme sera plus avancée, avec des batteries plus performantes, dont l’autonomie s’approchera de celle des voitures à carburant, entre 600 et 1.000 km, selon la taille des batteries, et une recharge très rapide grâce à des batteries à 800 volts, comme certaines grandes Audi. BMW espère surtout que la Neue Klasse sera rapidement rentable.
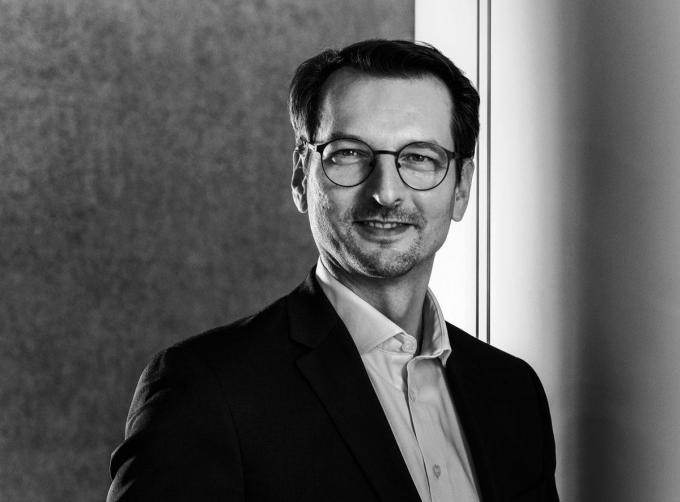
“La batterie solide sera un ‘game changer’ à la fois en autonomie, en densité énergétique et même sur le plan environnemental.” MILAN NEDELJKOVIĆ (BMW)
La même prudence vaut pour les perspectives d’une nouvelle génération de batteries solides. Alors que Toyota annonce lancer la production de masse de ce type de batterie à partir de 2027, pour des véhicules dont l’autonomie dépassera les 1.000 km via une recharge complète en 10 minutes, BMW se montre moins catégorique. “Les batteries solides autorisent une plus grande densité énergétique, donc un poids moindre, mais nous devons parvenir à un processus de production stable, une technologie qui puisse être industrialisée et nous en sommes encore loin, explique Milan Nedeljković. Ce sera sans doute pour la fin de la décennie.”
Problèmes de dilatation
Martin Schuster, vice-président en charge du développement des cellules de batterie et de leur recyclage chez BMW, ajoute: “Il y a encore pas mal de problèmes à régler. Par exemple, les cellules solides se dilatent d’environ 10% pendant le processus de charge/décharge. Imaginez ce que cela peut représenter sur un pack de batteries de deux mètres: c’est 20 cm de différence. Nous devons mieux comprendre le processus et essayer de réduire ce phénomène. Mais nous sommes convaincus de l’intérêt de la technologie. Sinon, nous n’aurions pas investi autant d’argent dans cette approche. Ce sera un game changer à la fois en autonomie, en densité énergétique et même sur le plan environnemental, car il n’y a pas d’électrolyse”. Un vaste espace a d’ailleurs également été prévu dans l’usine de Parsdorf pour de futures chaînes tests de production de la batterie à cellules solides.