Les robots des usines automobiles bientôt au chômage? Ce sera peut-être le cas si les constructeurs fondent d’énormes pièces d’un coup au lieu de souder des dizaines de tôles. Tesla utilise cette technologie pour réduire ses coûts. Toyota, Volvo et d’autres suivent le mouvement.
Un jour de fin 2018, Elon Musk entame une réunion chez Tesla en posant sur la table une Model S miniature, un jouet. “Qu’est-ce qui nous empêche de réussir la même chose?” lance-t-il à ses équipes. Le CEO fait allusion à la manière dont la maquette (ou le jouet) a été fabriqué, soit une seule pièce de métal coulée et moulée… Deux ans plus tard, Tesla commençait à fabriquer de grands éléments de ses Model Y avec cette technique: les soubassements avant et arrière habituellement assemblés avec des dizaines de tôles estampées et soudées.
Cette scène, racontée dans un récent livre consacré Elon Musk (*), illustre une innovation considérable dans l’assemblage automobile. Elle consiste à réduire le nombre de pièces à la fois par économie et pour alléger le véhicule, et à fabriquer des morceaux de la structure d’une voiture non plus avec des robots mais en coulant des pièces de grande taille dans des systèmes de moulage à haute pression. “Les machines injectent de l’aluminium fondu dans un moule, écrit l’auteur de l’ouvrage, Walter Isaacson, d’où ressort en tout juste 80 secondes un châssis complet, monobloc, qui se composait auparavant d’une centaine de pièces.”
Ce système utilisé par Tesla est fourni par une société italienne, Idra. Il consiste en une machine énorme, pesant 400 tonnes, appelée Giga Press, dont le nom est devenu générique. Tout le secteur parle désormais de “gigacasting” ou aussi de “megacasting” (moulage géant). Ce processus de “die cast” (moulage à haute pression) est un élément clef pour réduire les coûts de production que Tesla espère abaisser de moitié pour les prochaines générations de voitures. Cette technologie lui a déjà permis de réduire le prix de vente des Model Y en restant rentable, déstabilisant au passage la concurrence.
Un des problèmes du moulage est la difficulté de dépasser une certaine taille en conservant une bonne qualité. L’utilisation d’une forte pression permet de résoudre ce problème.” – AUDE SIMAR (UCLOUVAIN)
Volvo, Toyota, GM, Ford suivent
Après une valse hésitation, la concurrence a décidé de suivre aussi cette voie. C’est notamment le cas de Toyota. Pour ce dernier, le défi est de taille car jusqu’ici, le constructeur japonais était la référence mondiale en matière de processus de production automobile avec son “Toyota production system” et son approche dite “kaizen” d’amélioration continue. Volvo s’est aussi lancé: en 2022, la marque annonçait qu’elle commandait à l’entreprise suisse Bühler deux machines géantes de moulage sous pression pour son usine de Torslanda, en Suède. On y assemblera dès 2025 une nouvelle génération de voitures électriques. Mais le constructeur a aussi récemment annoncé avoir commandé deux Giga Press de 9.000 tonnes de pression chez Idra pour une nouvelle usine en Slovaquie.

Toyota travaille également sur la production de grandes pièces en gigacasting. Selon la publication spécialisée Automotive News Europe, le groupe compte même fabriquer lui-même ses machines de moulage sous pression, en partie parce que l’offre n’est pas suffisante au Japon, et parce que les rares producteurs de systèmes géants auraient déjà des carnets de commandes bien remplis.
Plus récemment, General Motors a, lui, acquis Tooling & Equipment International, entreprise qui a déjà aidé Tesla à concevoir des moules pour ses pièces fabriquées en gigacasting à l’aide d’une technologie d’impression 3D utilisant du sable. Tesla va donc sans doute devoir désormais trouver un autre partenaire pour cette tâche, ou la développer en interne.
“A l’instar de GM, les constructeurs automobiles, de Ford à Hyundai en passant par Toyota, tentent de copier le savoir-faire de Tesla en matière de gigacasting pour parvenir à son efficacité en matière de conception et de fabrication et éviter d’être dépassé dans les show-rooms”, résume ainsi l’agence Reuters.
Des machines de 400 tonnes
Evidemment, le moulage à haute pression d’aluminium ou d’autres métaux n’est en soi pas une nouveauté. Tous les constructeurs utilisent déjà le procédé pour fabriquer des culasses, des blocs moteurs et bien d’autres éléments. L’innovation réside ici dans la taille des pièces fabriquées, que seule une machine pouvant injecter le métal à une pression considérable est capable de concevoir. Cette machine, cette Giga Press, la société italienne Idra la commercialise depuis 2019. C’est “la plus grande machine au monde, de 8.000 et 9.000 tonnes de pression de moulage, utilisée pour accélérer la transition vers de voitures électriques et hybrides”, proclame le site de l’entreprise. Celle-ci est une filiale depuis 2018 d’un groupe chinois, LK Technology, basé à Hong Kong, lui aussi actif dans le moulage à haute pression pour l’automobile.
Jusqu’ici, le moulage de pièces de grande taille était quasi impossible. “Un des problèmes est la difficulté de dépasser une certaine taille en conservant une bonne qualité”, explique Aude Simar, professeure de fabrication mécanique et d’advanced manufacturing technology à l’Ecole polytechnique de l’UCLouvain. “L’utilisation d’une forte pression permet de résoudre certains de ces problèmes.”
Aude Simar estime que la nouvelle approche de la fabrication dite additive (WAAM ou “wire arc additive manufacturing”), qui utilise des dispositifs d’imprimantes 3D, permet aussi de fabriquer des pièces complexes d’un seul tenant. Par exemple les moules eux-mêmes des machines géantes de moulage. Mais selon la professeure, le die casting (moulage métallique sous pression) a sans doute l’avantage actuel de mieux convenir à une production en grande série, soit plusieurs centaines de pièces par jour.
Plus difficile à réparer?
Cette évolution n’est pas sans risque. “Ces machines massives de gigacasting peuvent poser des soucis de déformations dans le métal (…) et exiger une inspection détaillée, un scanning en fin de ligne”, avance un rapport de l’agence de rating Standard&Poors (S&P). Cette dernière reconnaît toutefois que si elle est effective, cette avancée sera considérable pour ceux qui sont prêts à effectuer de tels investissements. L’agence estime que cette technique pourrait réellement bouleverser l’activité d’estampillage de tôle et tout le matériel qui y est attaché, les robots notamment. La partie visée par le gigacasting, les soubassements des autos, représente en effet environ 50% de la carrosserie dite blanche (carrosserie sans les éléments ouvrants).
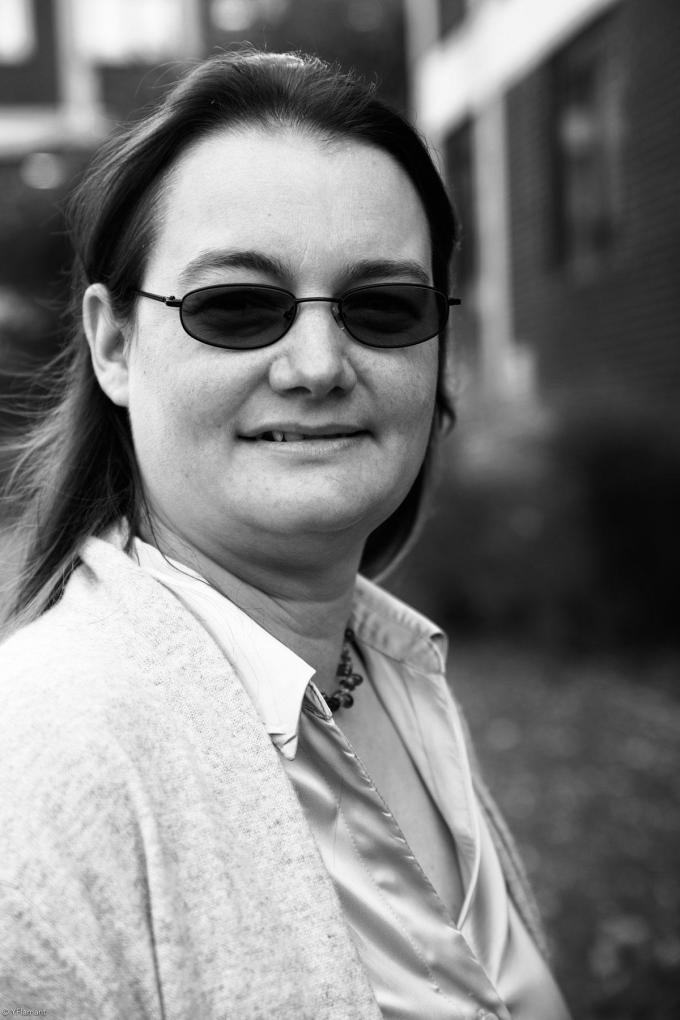
Pour les automobilistes, cette évolution ne devrait rien changer puisqu’elle porte pour l’heure sur des grandes pièces formant le châssis du véhicule et que personne ne voit jamais. Mais pour les garagistes, l’usage du gigacasting a d’autres conséquences: notamment la plus grande difficulté à réparer le véhicule quand il est accidenté puisqu’il faudra alors remplacer une énorme pièce et non quelques éléments soudés. Ce qui peut mener à un déclassement plus fréquent. Cet argument est contesté par Sandy Munro, spécialiste en simplification de la fabrication de voitures. “Si vous pliez les longerons d’une voiture (fabriquée de manière traditionnelle, avec des tôles soudées, Ndlr), vous ne pourrez pas non plus la réparer ; les assurances ne voudront pas que l’auto soit remise sur la route, car elle ne sera pas sûre”, réplique l’expert dans une séquence de son Munro Live, sur YouTube.
Sandy vous explique tout
Pour comprendre l’apport du gigacasting, cela vaut la peine de visionner sur YouTube les vidéos publiées par Sandy Munro, 73 ans. Cet ingénieur américano-canadien dirige une société de conseil, Munro & Associates, spécialisée dans la simplification de la production d’automobiles. Avec ses 360.000 followers, Sandy Munro est un peu une vedette dans le petit monde des ingénieurs de l’automobile, publiant des vidéos sur sa chaîne Munro Live dans lesquelles il démonte des batteries ou des moteurs de voitures électriques, truffant son action de commentaires. Ses vidéos sur le gigacasting permettent de bien en comprendre les principes. Tapez “Munro et gigacastings”. La vidéo titrée “Evolution of Tesla Bodies in White” est sous-titrée en français et assez spectaculaire, montrant plusieurs structures de Tesla avant et après l’utilisation de cette technique.
Tesla semble en tout cas bien miser sur le gigacasting pour développer son futur modèle à 25.000 euros, qui sera notamment produit à Berlin. Le constructeur américain pourrait même aller plus loin et construire d’une seule pièce l’ensemble du soubassement. Mais ce procédé nécessiterait une machine encore plus énorme que les Giga Press ou les autres machines de LK utilisées actuellement par Tesla, devant dégager une pression de 16.000 tonnes, rapporte Reuters. Tout cela fait encore l’objet de tests et de recherches.
S&P doute d’ailleurs que Tesla utilise systématiquement cette technologie. L’agence a fait de savants calculs et déduit que le constructeur ne peut produire actuellement que 150.000 pièces en gigacasting dans son usine de Shanghai dont la capacité est pourtant d’un million de véhicules par an. Il y aura donc encore sans doute une longue période de transition, d’essais/erreurs, et de gros investissements.
La fin de la chaîne de montage
Reste que le constructeur américain travaille aussi à une nouvelle approche de l’assemblage, appelée “unboxing”, qui mettrait fin à la fabrication à la chaîne. Elle consiste à usiner et peindre des modules de la voiture séparément et à tout assembler en fin de parcours. Cette approche, favorisée par le gigacasting, a été présentée à son Investor Day le 1er mars dernier. Elle contribuerait à une réduction du coût de 50% (espérée) et une réduction de 40% de l’espace nécessaire dans les usines. Une tendance à la simplification qui s’inscrit dans le droit fil de l’électrification. On le rappelle, construire une automobile électrique nécessite beaucoup moins de pièces. Le seul élément réellement coûteux de ces véhicules encore chers est la batterie. Quelle meilleure manière, donc, d’en abaisser le prix en parvenant à réduire le coût de production du reste de l’auto?
(*) Walter Isaacson, “Elon Musk”, Fayard, 672 pages.