A Lanklaar, commune mosane à la frontière néerlandaise, la société Vandersanden utilise une matière première d’origine naturelle, traditionnelle et en abondance dans la région pour fabriquer ses briques: tout simplement l’argile. Elle en produit plus de 550 millions par an.
Le spécialiste de la brique de parement
C’est en 1925 que Jaak Vandersanden ouvre une petite briqueterie à Spouwen, dans la province du Limbourg. Après la Seconde Guerre mondiale, son fils Constant fait de l’entreprise l’une des plus grandes briqueteries de Belgique. La troisième et quatrième génération de la famille a, depuis, intégré la société. Deux gendres de la troisième génération sont aujourd’hui à la barre: Jean-Pierre Wuytack, CEO, et Guy Wauters, CFO. Deux arrière-petits-enfants de Jaak Vandersanden ont même fait leur entrée dans le groupe.
Vandersanden a racheté en 2017 la division argile de l’irlandais CRH, spécialisé dans les matériaux de construction. “L’opération a accéléré notre expansion internationale, déclare le COO Raf Jansen: les quatre usines reprises sont situées aux Pays-Bas et en Allemagne. Elle a également conduit à une plus grande diversification de la gamme puisqu’aux briques de parement se sont ajoutés les pavés.” Pour Nathali Donatz, la directrice du marketing, l’acquisition est aussi synonyme d’économies d’échelle: “Nous pouvons investir davantage dans l’innovation et la stratégie durablelle. Or, nous voulons être précurseurs dans la lutte contre le changement climatique.”
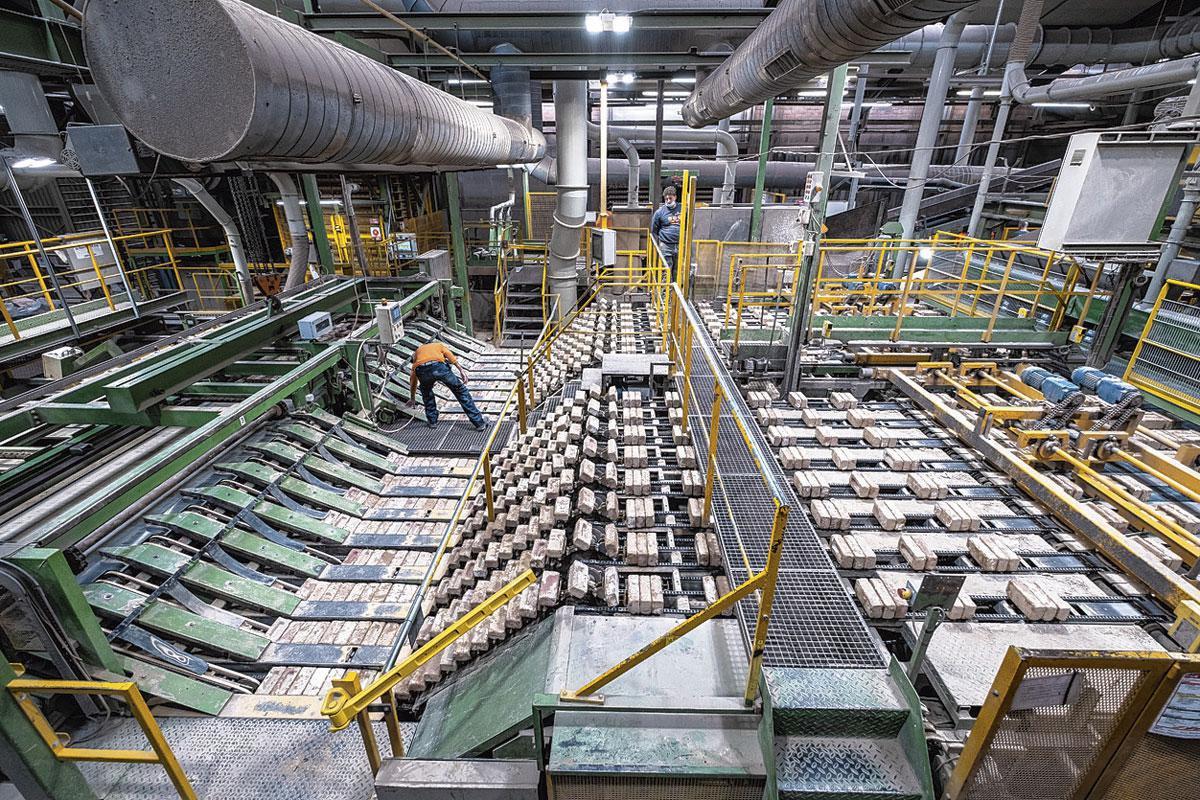
L’usine de Lanklaar, également située au Limbourg, produit quelque 100 millions de briques de parement par an. Les 10 sites du groupe fabriquent au total plus de 550 millions d’unités. L’entreprise, qui emploie 725 personnes, a achevé l’exercice 2019 sur un chiffre d’affaires de 200 millions d’euros.
Vandersanden est relativement épargnée par la crise. “Parmi les projets de construction autorisés, démarrés et financés, très peu ont été interrompus, se réjouit Raf Jansen. Les entrepreneurs nous disent maintenant que leurs carnets de commandes se remplissent moins facilement mais pour relancer l’économie, de nombreux pays comptent soutenir le secteur de la construction.”
1. Une matière première naturelle
Deux immenses monticules dominent le site de Lanklaar. “L’un est du limon rouge, l’autre, du limon jaune, précise Raf Jansen, le directeur opérationnel de Vandersanden. En plus des quelques argilières que nous possédons, nous employons du limon récupéré lors de travaux d’infrastructure, ainsi que de l’argile du Westerwald (en Allemagne, Ndlr). Toutes ces matières premières sont omniprésentes dans le sous-sol. Nous ne risquons donc pas d’épuiser les ressources naturelles. Elles sont de surcroît situées à proximité de l’usine.”
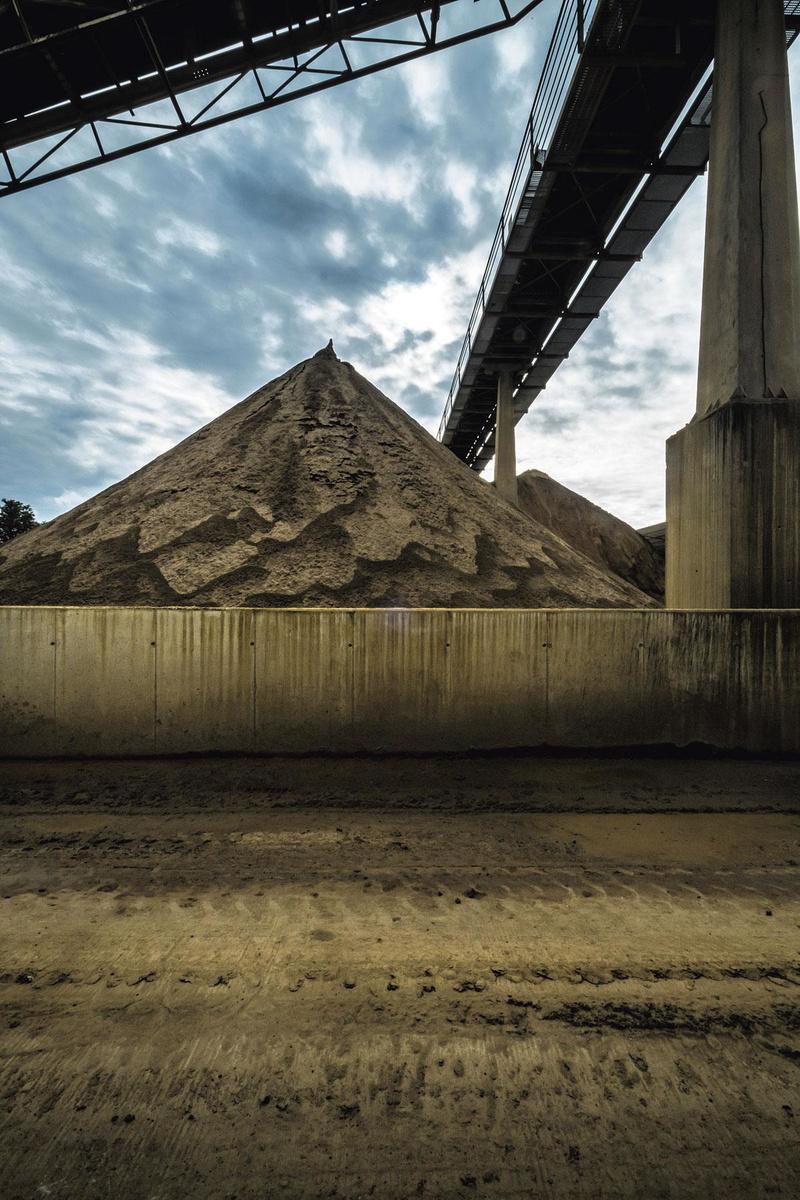
2. Le malaxage
L’argile et le limon récupéré peuvent contenir des impuretés, comme des composants métalliques ou des cailloux. Après avoir éliminé celles-ci, des mélangeurs malaxent la matière pour en faire une masse fine et homogène qui sera ensuite divisée en boules.
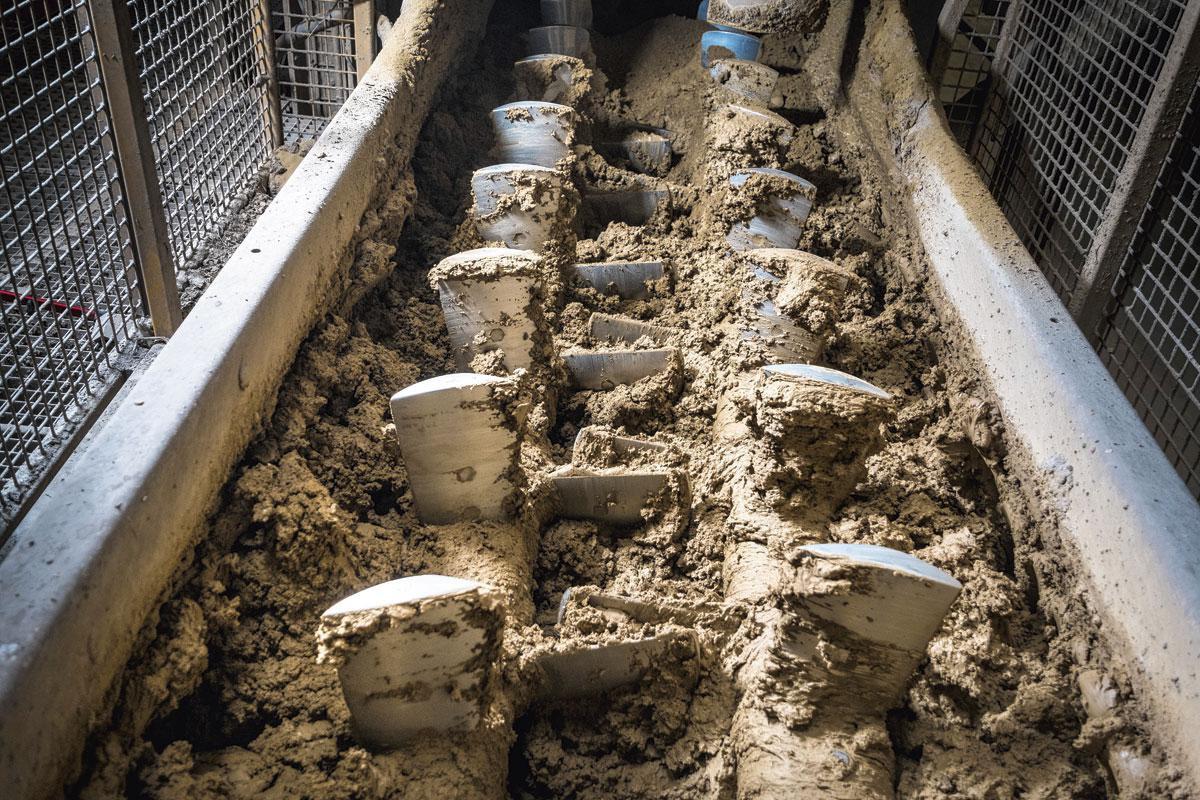
3. Le moulage
Les boules formées par la presse roulent sur un lit de sable, avant d’être projetées dans des moules. “Cela donne au produit sa structure rugueuse caractéristique et garantit qu’aucune brique n’est identique à une autre, poursuit Raf Jansen. Autrefois, les boules d’argile étaient jetées dans le moule à la main. Aujourd’hui, l’opération est entièrement automatisée”, explique Raf Jansen.
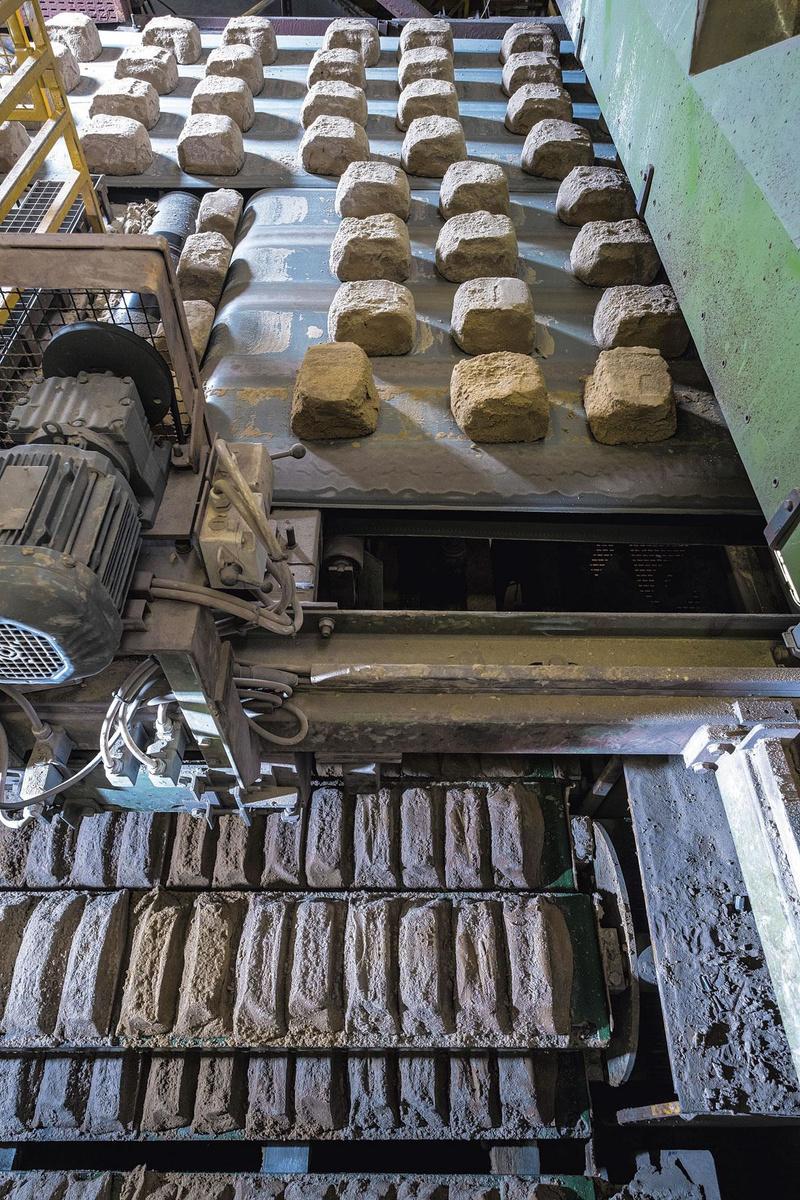
4. Le séchage et la cuisson
Une fois sorties du moule, les briques sont installées par des robots sur des platines et empilées sur des étagères. Elles resteront deux jours dans le séchoir. “C’est pendant le séchage que les particules d’argile s’agglomèrent les unes aux autres, ce qui forme la structure de la brique, détaille notre interlocuteur. Le taux d’humidité est abaissé de 18-22% à 2%. Cela permet d’éviter la formation de vapeur, susceptible de fendre la brique, pendant la cuisson.” Raf Jansen précise que c’est la chaleur récupérée des fours qui chauffe le séchoir. Les briques séchées sont ensuite empilées sur des wagonnets pour être acheminées vers l’un des quatre fours tunnels. “Les briques sont chauffées à 1.100 °C, puis refroidies d’une manière très contrôlée, décrit Raf Jansen. La température élevée liquéfie légèrement les particules d’argile, qui s’agglomèrent aux parties dures de la matière.” La cuisson dure trois jours.
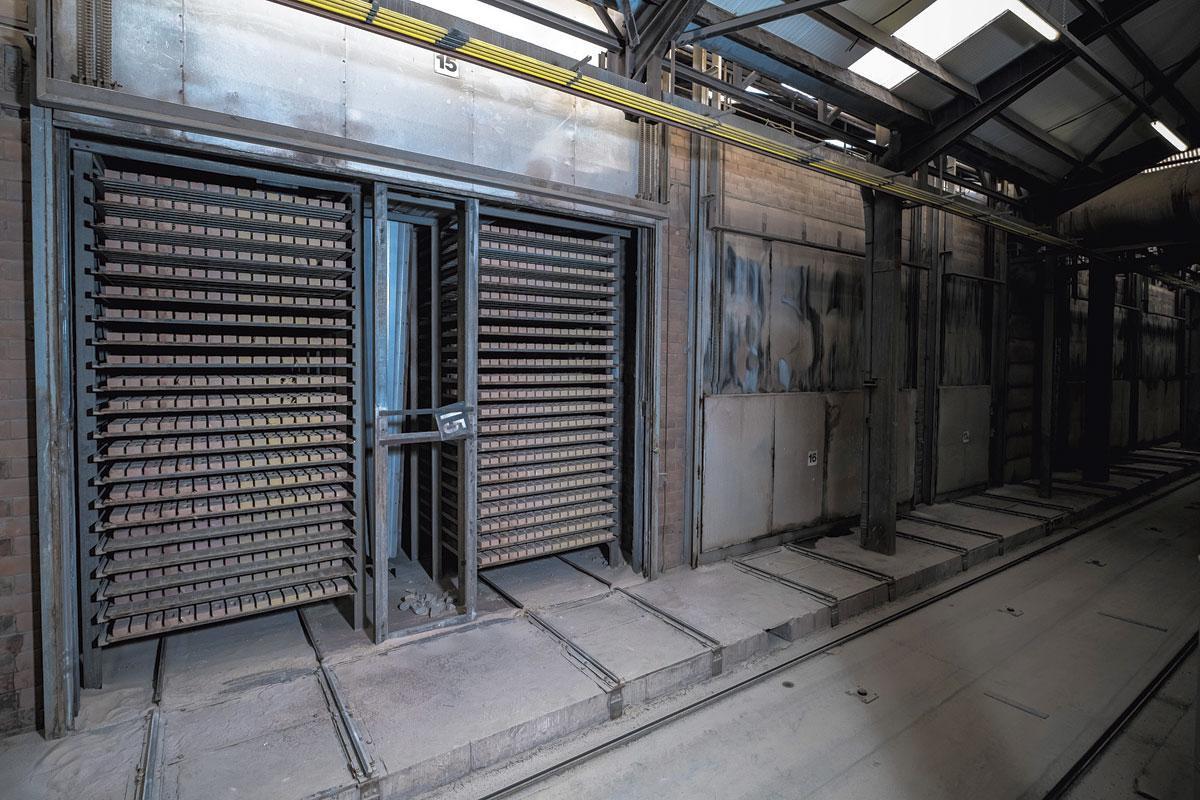
4. Le séchage et la cuisson
Une fois sorties du moule, les briques sont installées par des robots sur des platines et empilées sur des étagères. Elles resteront deux jours dans le séchoir. “C’est pendant le séchage que les particules d’argile s’agglomèrent les unes aux autres, ce qui forme la structure de la brique, détaille notre interlocuteur. Le taux d’humidité est abaissé de 18-22% à 2%. Cela permet d’éviter la formation de vapeur, susceptible de fendre la brique, pendant la cuisson.” Raf Jansen précise que c’est la chaleur récupérée des fours qui chauffe le séchoir. Les briques séchées sont ensuite empilées sur des wagonnets pour être acheminées vers l’un des quatre fours tunnels. “Les briques sont chauffées à 1.100 °C, puis refroidies d’une manière très contrôlée, décrit Raf Jansen. La température élevée liquéfie légèrement les particules d’argile, qui s’agglomèrent aux parties dures de la matière.” La cuisson dure trois jours.
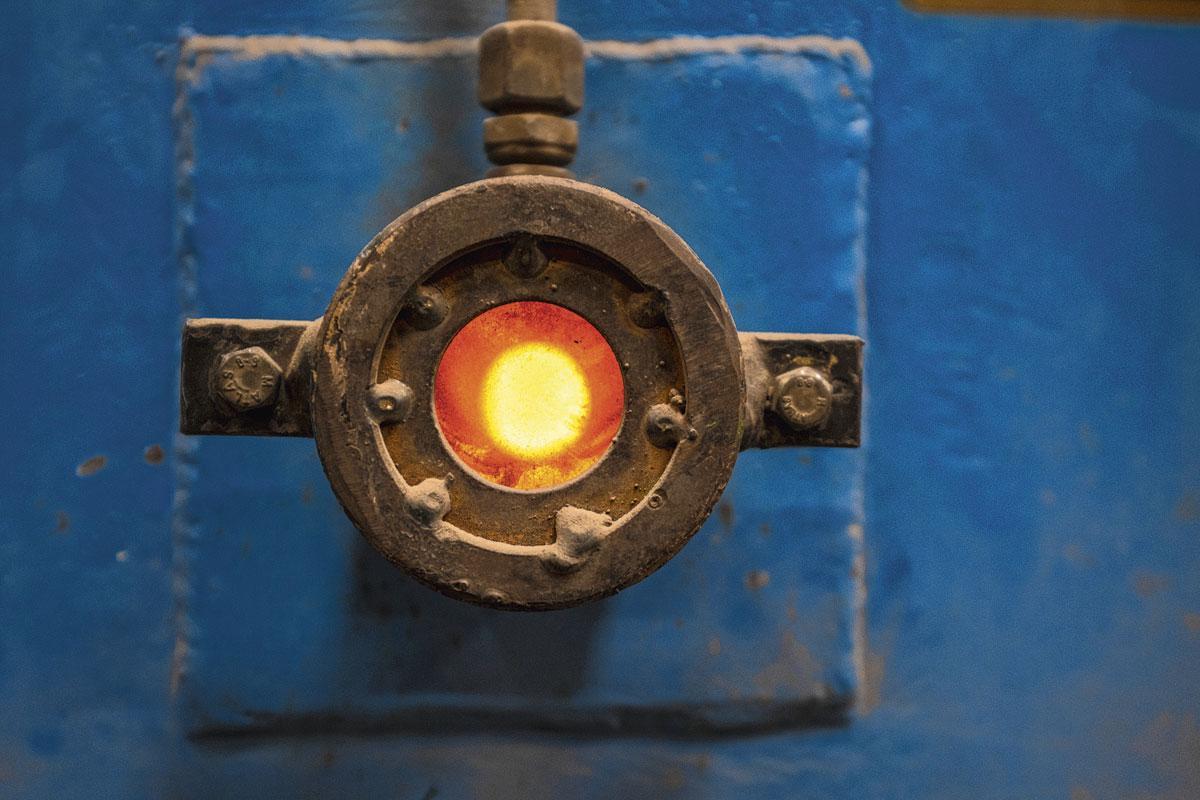
5. L’imprégnation
Vandersanden a investi 35 millions d’euros pour équiper ses trois grandes usines de briques de parement d’une ligne d’imprégnation et rendre ses produits plus résistants aux intempéries. “L’imprégnation rend la brique imperméable. Les mortiers contiennent souvent des sels hydrosolubles et de la chaux, qu’un phénomène d’évaporation fait migrer vers la face externe de la brique ; c’est ce qui provoque ces dépôts blancs que l’on voit sur certaines façades.” Le produit d’imprégnation est appliqué à l’aide d’un rouleau spongieux.
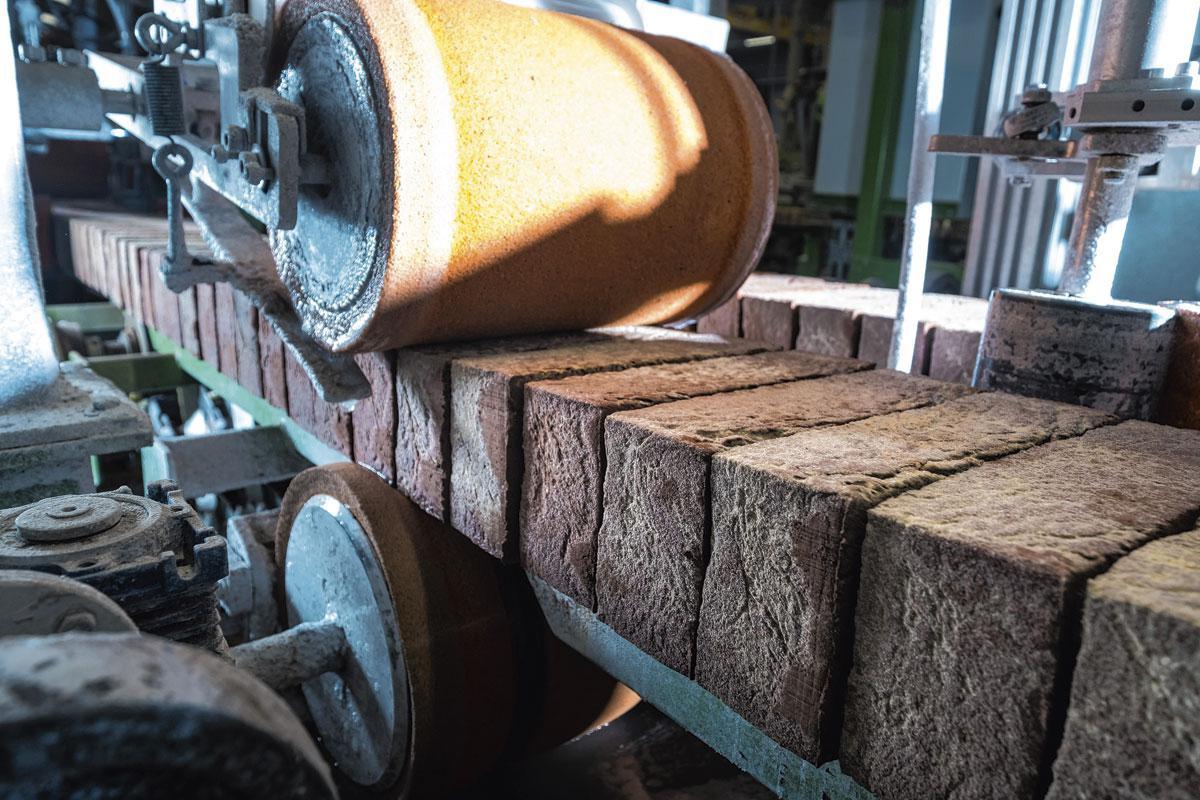
6. Emballage et stockage
Des robots empilent ensuite les briques sur des palettes. Ce sont eux aussi qui les entourent d’un film rétractable, avant que les palettes soient entreposées à ciel ouvert. “Pour un produit qui résiste au vent et aux intempéries, investir dans des entrepôts est inutile. A Lanklaar, le stock contient environ 25 millions de briques”, conclut Raf Jansen.
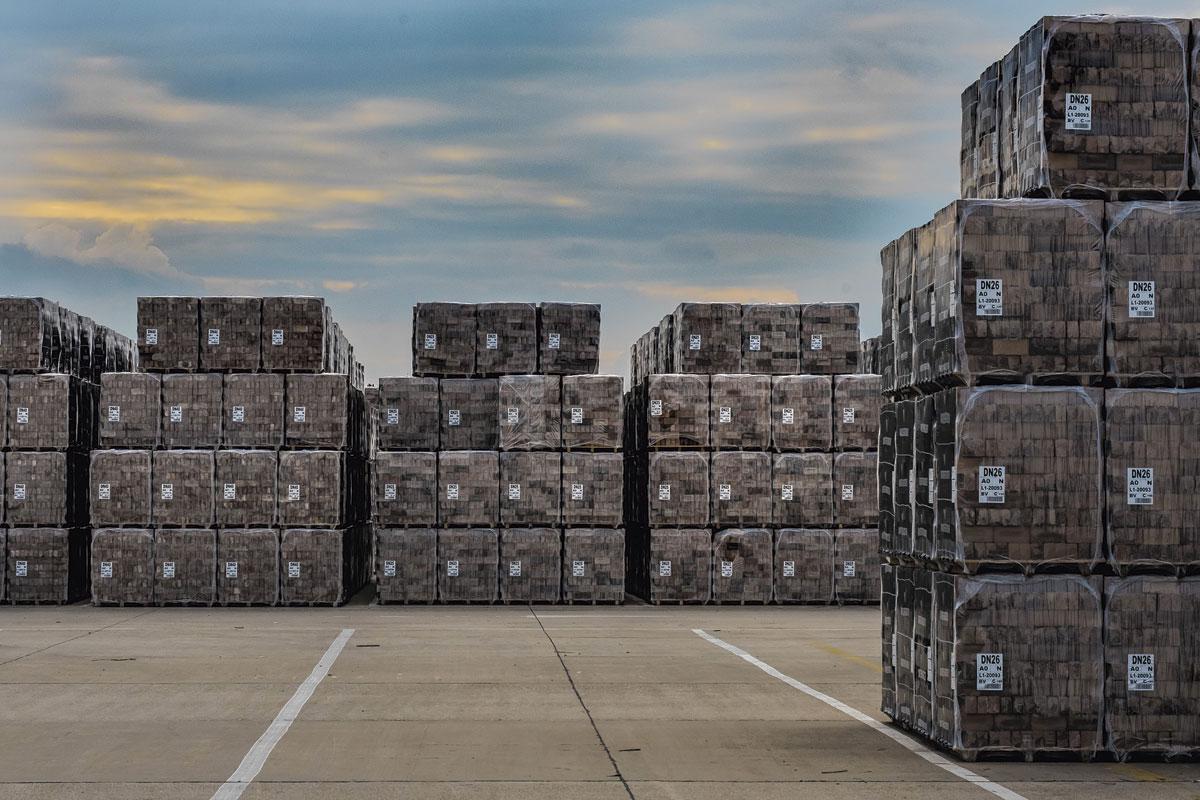