D’immenses volumes de terre sont extraits chaque année des chantiers de construction à Bruxelles. BC Materials convertit cette terre d’excavation en matériaux de construction circulaires et neutres en CO2. Notamment en briques de terre comprimée qui seront employées sur des chantiers suivants.
1. La terre bruxelloise
A Bruxelles, d’immenses volumes de terre sont excavés à l’occasion de chantiers. “Environ 2 millions de tonnes par an, calcule Anton Maertens, business developer chez BC Materials, installé près de Tour & Taxis. La couche supérieure est faite de sable, généralement du sable bruxellien. Beaucoup plus profondément, on tombe sur de l’argile yprésienne, techniquement excellente pour la construction.”
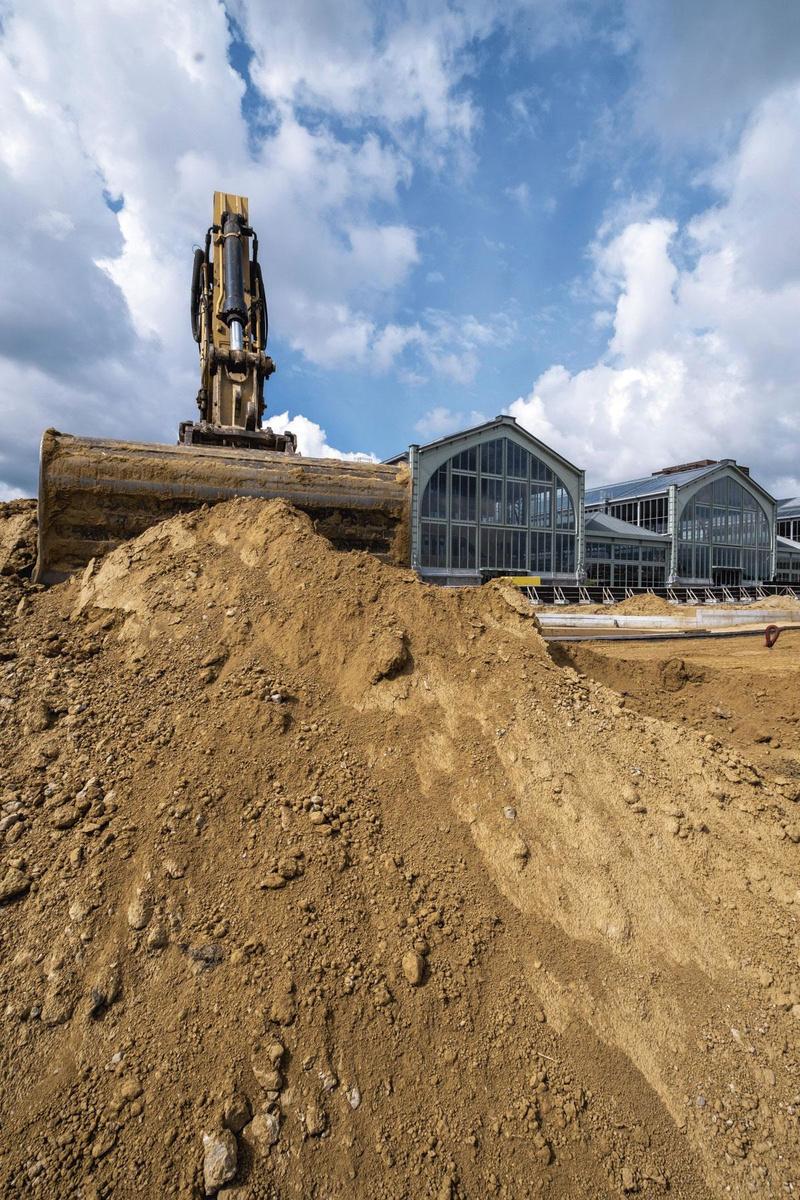
2. Entreposage et séchage
“Nous sommes ravis d’avoir trouvé ce site dans le port de Bruxelles, sourit Anton Maertens. Nous voulions être en ville, à la source, tout en disposant d’un espace suffisant. Le sable est livré par des camions, qui doivent pouvoir manoeuvrer et décharger. Chaque livraison pèse généralement une dizaine de tonnes, au bas mot.”
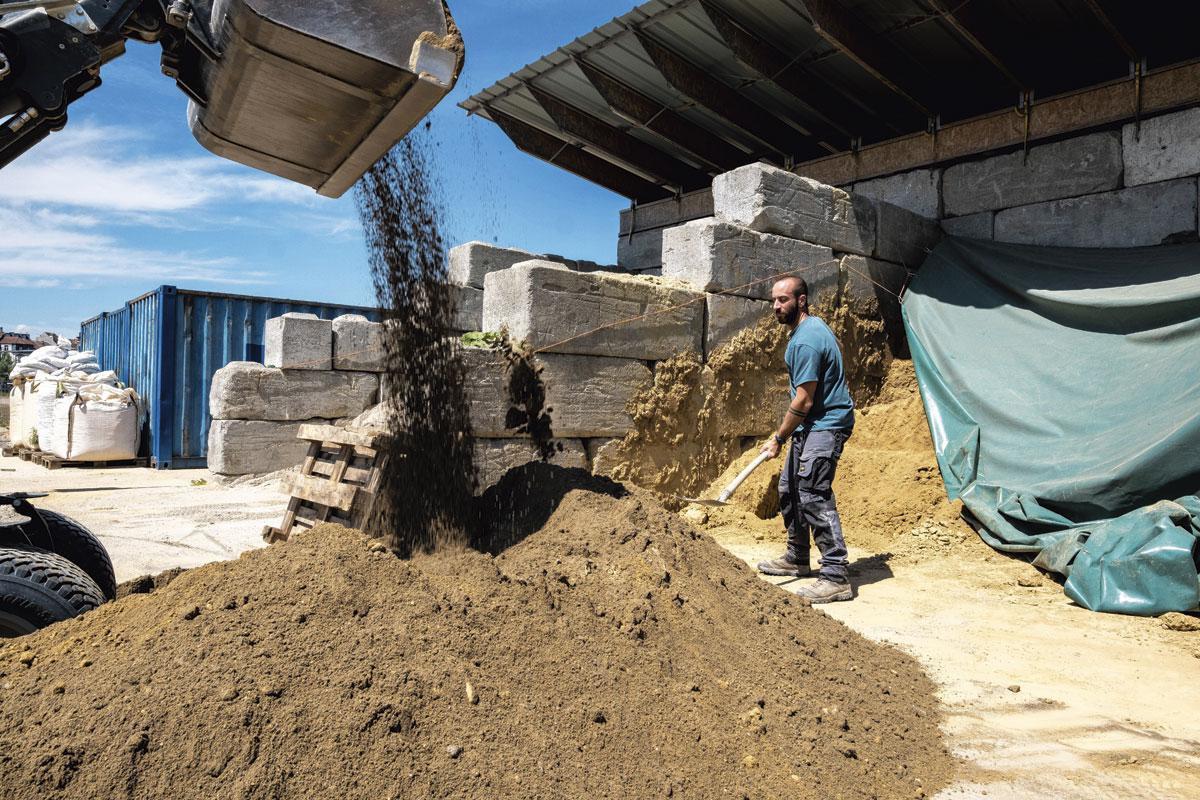
3. Mélange
Une chargeuse sur pneus déverse le sable dans un mélangeur. “C’est dans la définition de ce mélange que s’exprime l’essentiel de notre expertise, déclare Anton Maertens. Il s’agit surtout de trouver le bon rapport entre le sable bruxellien et l’argile yprésienne. Pour les murs porteurs, la brique doit être stabilisée. Une stabilisation à la chaux la rend plus solide.” Les briques stabilisées ne sont toutefois pas totalement neutres en carbone…. “mais beaucoup plus que les briques classiques: 10 fois plus”, souligne Anton Maertens qui ajoute que l’entreprise produit aussi pour les constructions à ossature bois: “La structure étant alors porteuse, les murs n’ont pas à être aussi résistants ; nos briques non stabilisées donnent de la masse à la construction, ce qui en améliore les propriétés acoustiques et thermiques”.
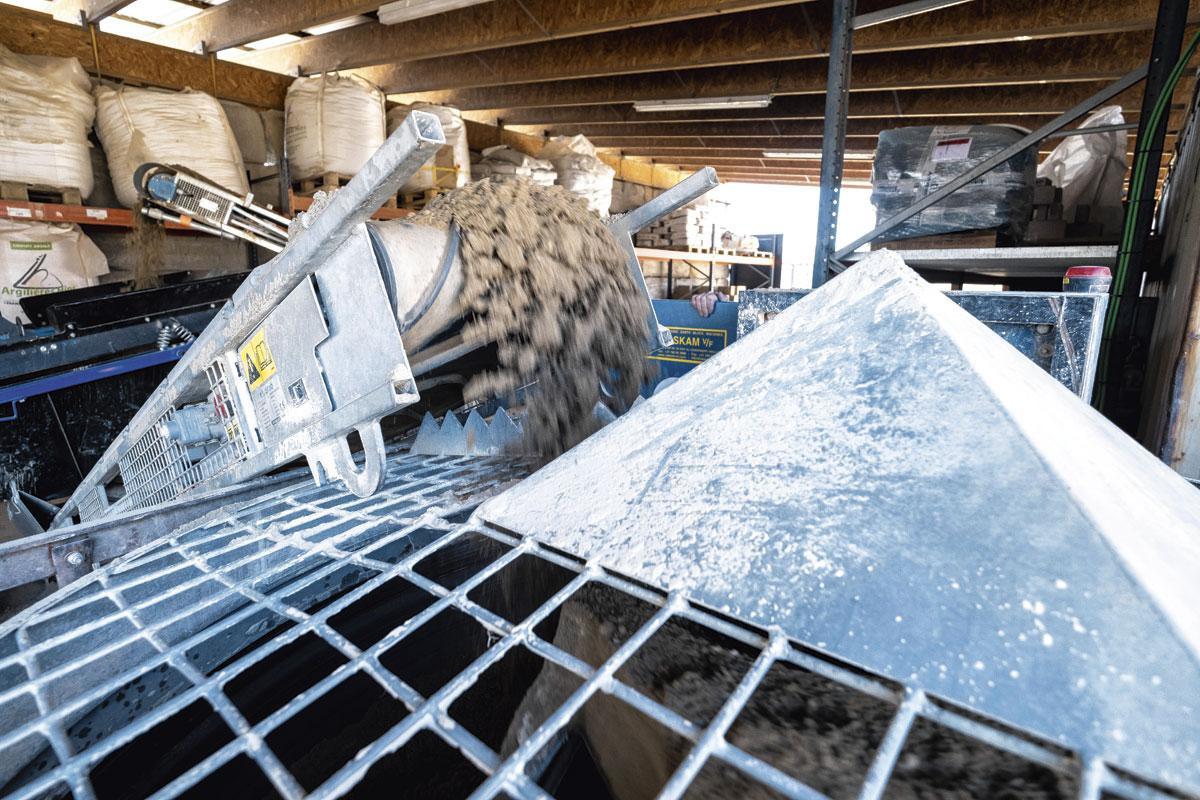
4. Vers la presse
Deux bandes de transport et de chargement acheminent le mélange vers l’entonnoir de la presse. “Un système extrêmement simple, apprécie Anton Maertens. Parfois, les entreprises sont très axées sur des solutions de haute technologie qui ont l’art de tout compliquer. Nous estimons qu’une technologie basique est, dans certains cas, une solution plus maligne.”
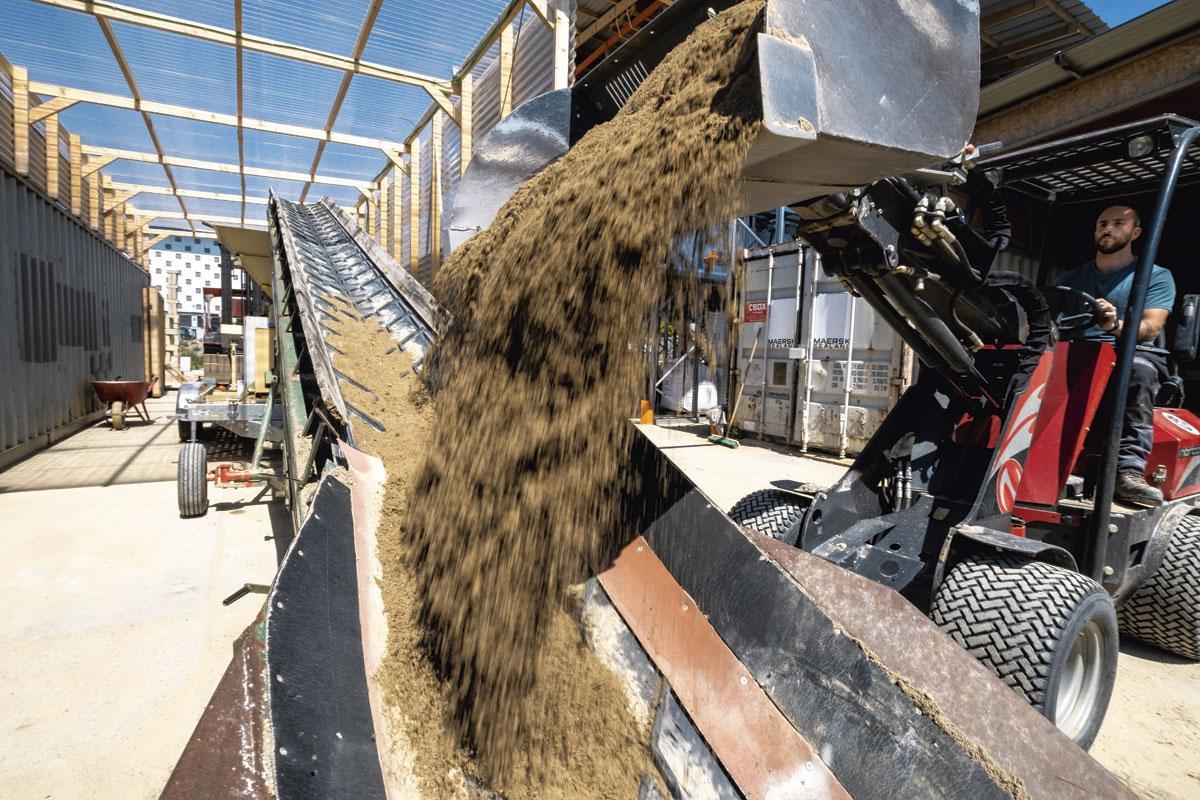
5. Presse
Le mélange est comprimé dans un moule, à une pression de 180 bars. “Nous avons fait fabriquer cette presse sur mesure par un spécialiste français, explique Anton Maertens. Sa capacité de production tourne autour de 1.500 briques par jour. Elle nous permet aussi de réaliser des prototypes. C’est important car nous travaillons avec de nombreuses sortes de terre. Nous pouvons tester de nouvelles variantes. Il s’agit en outre d’une machine qu’on peut déplacer sur chantier afin de produire sur place. Dans ce cas, nous pressons une terre tout juste excavée ou presque.”
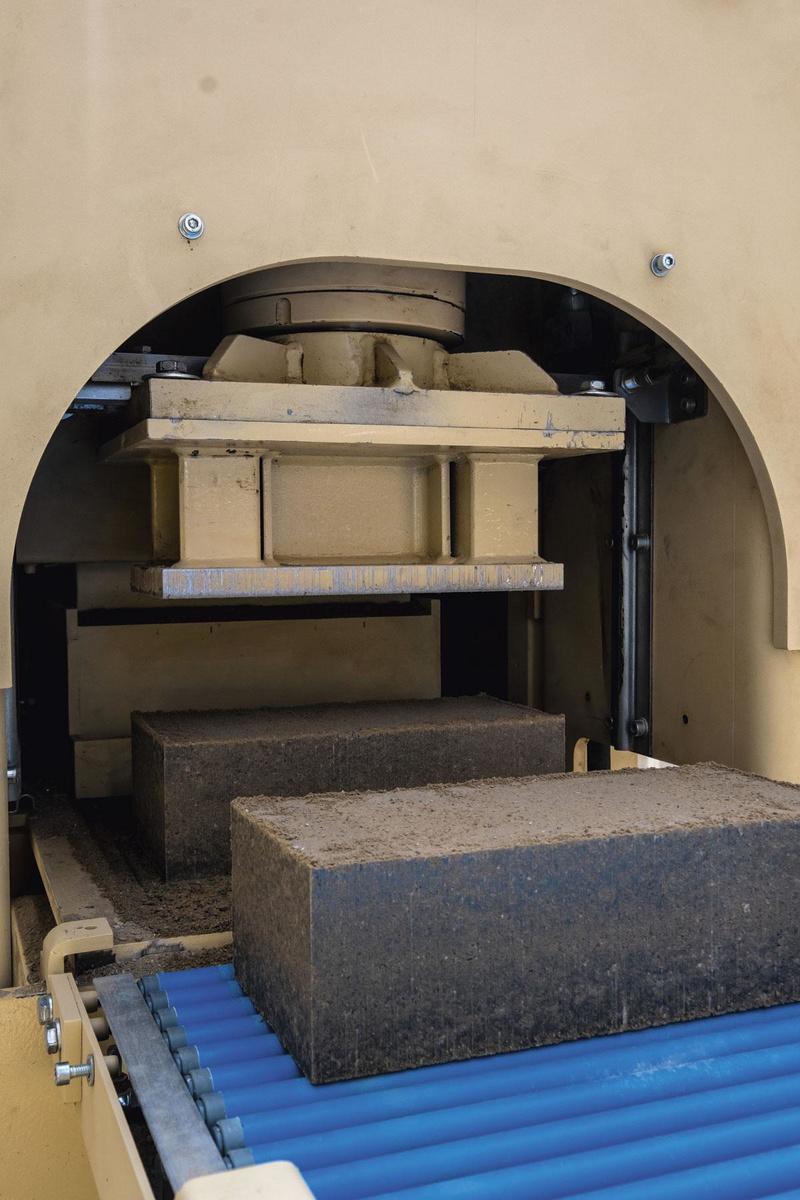
6. Empilage et séchage
Les briques sont empilées sur des palettes et placées sur des claies, où elles sécheront pendant un mois avant d’être acheminées vers de nouveaux chantiers.
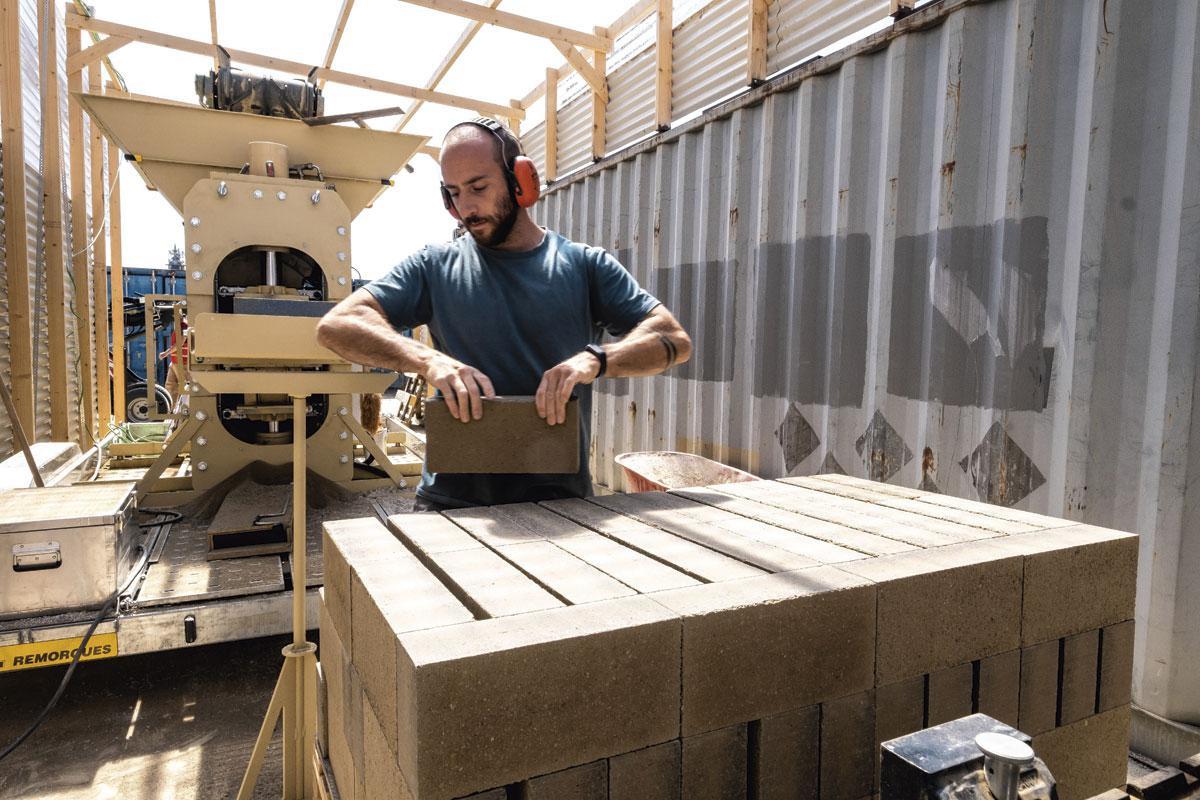
Vers la neutralité carbone
BC Materials est une spin-off du cabinet bruxellois BC Architects. C’est à l’occasion de la construction d’une bibliothèque au Burundi que ses architectes ont appris à travailler la terre locale, à l’état cru. Une fois rentrés, ils ont mis à profit ces connaissances nouvellement acquises dans plusieurs projets belges qui ont fait sensation. “Ces projets ont eu un effet inspirant mais les possibilités ne s’arrêtaient pas là, déclare Anton Maertens, business developer chez BC Materials. Nous voulions avoir un effet plus marqué encore sur le secteur de la construction.” Lequel, souligne notre interlocuteur, est responsable de 30 à 40% des émissions de CO2 et d’un tiers des déchets dans le monde. “Dans les environnements urbains, la part de la construction dans la production de déchets est beaucoup plus élevée encore, poursuit-il. A Bruxelles, elle atteint 50%. La plupart des terres excavées sont tout simplement jetées. BC Materials les valorise et les transforme en matériaux de construction circulaires et neutres en CO2.”
Sur son site installé dans le port de Bruxelles, BC Materials fabrique trois produits: l’enduit d’argile, la brique de terre comprimée – baptisée “brickette” – et le mélange pour pisé. S’approvisionner et fabriquer sur les chantiers mêmes permet de limiter les transports mais freine le potentiel d’exportation. “Nous n’avons pas l’intention d’exporter de la terre, précise Anton Maertens. Nous pouvons en revanche exporter notre savoir-faire. C’est pourquoi nous disposons, en plus de nos activités de production, d’un département R&D et d’une section formation. La construction circulaire doit se développer. Les ateliers et les formations sont pour nous l’occasion de partager nos connaissances avec le secteur de la construction.” Avec neuf employés à temps plein, BC Materials a achevé l’exercice 2021 sur un chiffre d’affaires d’environ 450.000 euros.