La sidérurgie est responsable de 7 à 9% des émissions de CO2 dans le monde. Des projets de production d’acier décarboné émergent en Suède mais aussi en Belgique dans les usines d’ArcelorMittal et Aperam.
Gand est l’un des fleurons d’ArcelorMittal. Un bijou de technologie que le deuxième producteur mondial d’acier couve d’un regard embué de fierté. Après une cure de jeunesse à 195 millions d’euros, son haut-fourneau B est à peine remis en production depuis mars dernier que dirigeants et politiques ont annoncé en septembre une nouvelle étape: le site accueillera une nouvelle usine de production d’acier combinant la “réduction directe” avec deux nouveaux fours électriques, en remplacement du haut-fourneau A voué à l’arrêt. Objectif à l’horizon 2030: faire baisser les émissions de dioxyde de carbone (CO2) d’environ 3 millions de tonnes par an, soit à peu près l’empreinte carbone des habitants de la ville de Bruxelles.
Plus de 30% de notre personnel travaillera bientôt dans le recyclage, la culture de forêts ou la valorisation des matières. C’est un chiffre fort pour un soi-disant sidérurgiste, non?”
L’enjeu n’est pas mince. Avec 1,878 milliard de tonnes d’acier brut produites en 2020, la sidérurgie, dont le vaste empire s’étend de la fonte du fer jusqu’à l’affinage des aciers, est responsable de 7 à 9% des émissions globales de CO2, et d’un tiers de celles de l’industrie. Si elle était un pays, elle serait le troisième émetteur après la Chine et les Etats-Unis, mais avant l’Inde! Décarboner ce business permettrait d’agir à grande échelle sur les changements climatiques en cours.
Une innovation… connue depuis 50 ans
Bien que qualifiée d’innovante, voire de révolutionnaire, la technologie qui sera implantée à Gand n’est ni l’une ni l’autre. Elle est maîtrisée depuis les années 1970, et ArcelorMittal l’emploie déjà au Mexique. Mais comme tous les grands du fer, le groupe n’avait jusque-là jamais sauté le pas en Europe. C’est donc le premier acteur de cette taille, dans l’Union européenne, à renoncer à un procédé inchangé dans ses principes depuis… plus de 3.000 ans!
Dans la méthode historique, qui produit encore 75% de l’acier mondial, le fer est extrait dans un haut-fourneau, vaste four où sont mis en contact le minerai, du charbon purifié appelé coke et de l’air brûlant. Une fois la combustion du coke démarrée, les réactions chimiques associées dégagent des gaz comme le monoxyde de carbone qui vont arracher les atomes d’oxygène au fer, ce que les chimistes appellent une réduction. Le résultat est une fonte liquide, qui donnerait tel quel un métal dur mais cassant car trop riche en carbone. Une fois transférée dans l’aciérie, la fonte est versée dans un four où de l’oxygène sous pression est injecté pour brûler le carbone. Le produit final est alors de l’acier, souple et résistant.
Brûler du coke est affreusement émetteur de CO2: en moyenne 1,85 tonne par tonne d’acier, selon la World Steel Association. Ne pourrait-on pas obtenir le même résultat sans produire de gaz carboné? C’est tout l’intérêt de la “réduction directe” (Direct Reduced Iron ou DRI en anglais) qui sera pratiquée à Gand. Sous l’action d’un gaz chauffé, en général du méthane mais possiblement de l’hydrogène, le minerai de fer sera réduit sous forme de petits blocs, appelés éponges de fer. Sous cette forme, le métal peut ensuite passer dans des fours à arcs électriques, technologie qui utilise des courants électriques de forte intensité pour fondre le fer.
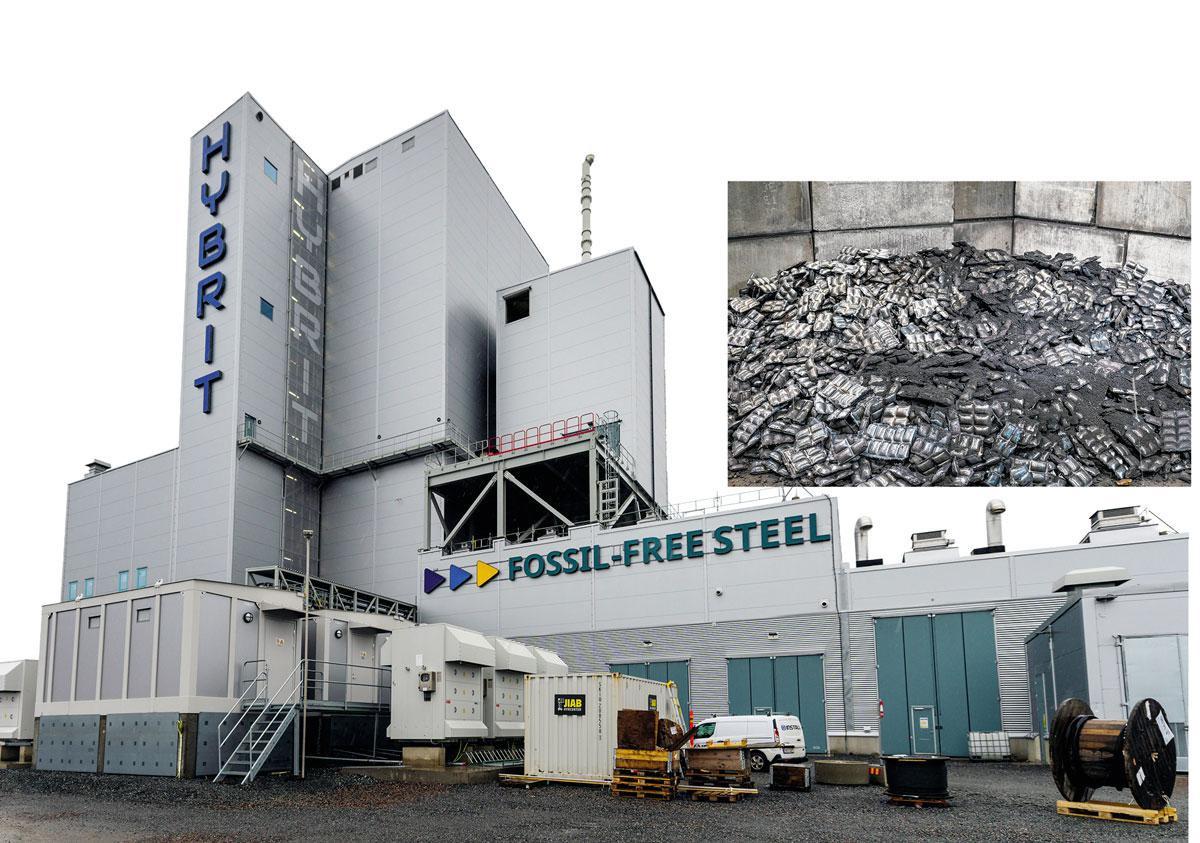
Avantages de cette technologie: la souplesse (à la différence d’un haut-fourneau, un four électrique s’arrête facilement) et, surtout, une moindre contribution au réchauffement climatique. Quarante pour cent de CO2 en moins avec le méthane, potentiellement beaucoup moins encore avec l’hydrogène… A condition d’utiliser de l’hydrogène “vert” et de l’électricité de même couleur. Car 95% de l’hydrogène mondial est en réalité “gris” car fabriqué en cassant des molécules de méthane avec de la vapeur d’eau, un procédé qui libère environ 10 tonnes de CO2 par tonne d’hydrogène. Pour devenir propre, il lui faudra découler d’une électrolyse de l’eau par une électricité elle-même décarbonée.
> Lire aussi: Les scieries belges à la pointe de l’innovation
De l’acier vert pour Volvo et Mercedes
A Gand, ArcelorMittal ne proposera pas ce produit hautement durable avant plusieurs années. En Suède, c’est pourtant déjà le cas. En août dernier, le consortium suédois Hybrit a annoncé avoir livré ses premières tonnes garanties “zéro fossile” à son client, le groupe Volvo. Dans les semaines suivantes, Hybrit, qui est l’émanation du sidérurgiste SSAB, de la minière LKAB et de la compagnie d’électricité Vattenfall, a signé des contrats avec les constructeurs Mercedes-Benz et Cargotec, ainsi qu’avec l’équipementier Faurecia. Par “zéro fossile”, le consortium signifie que le fer a été réduit par de l’hydrogène produit à l’aide d’électricité issue de barrages hydroélectriques, éliminant ainsi 90% des émissions totales de CO2.
Nous avons là le fruit d’un programme de recherche lancé en 2017, avec l’appui de l’Agence suédoise de l’énergie. Une belle avancée mais nous sommes encore loin du triomphe de l’acier décarboné. Le rendement sur le site pilote n’excède en effet pas encore une tonne de minerai réduit par heure, loin des quantités industrielles nécessaires. Même en tournant 24 heures sur 24 et sept jours sur sept, cela reste bien en dessous des 2,5 millions de tonnes de minerai réduit par an promis dans les nouvelles installations de Gand.
“Cela fait déjà une dizaine d’années que notre groupe recherche activement à décarboner notre industrie”, confie Eric Niedziela, vice president climate action d’ArcelorMittal Europe. Dans un rapport publié en juillet dernier, ArcelorMittal aligne un catalogue de projets aussi long que celui des maîtresses de Don Giovanni dans l’opéra de Mozart! Le grand oeuvre est prévu en Espagne pour 2025. A Gijón (Asturies), une installation de réduction directe à l’hydrogène vert, couplée avec un nouveau four à arc électrique hybride, verra le jour pour alimenter l’aciérie de Sestao, 250 km plus loin. Chaque année, 1,6 million de tonnes d’aciers plats garantis zéro émission de carbone devraient en sortir. Cofinancé avec le gouvernement espagnol pour 1 milliard d’euros, soit à peu près la même somme qu’à Gand (1,1 milliard), Gijón sera alimenté par un vaste réseau de centrales solaires.
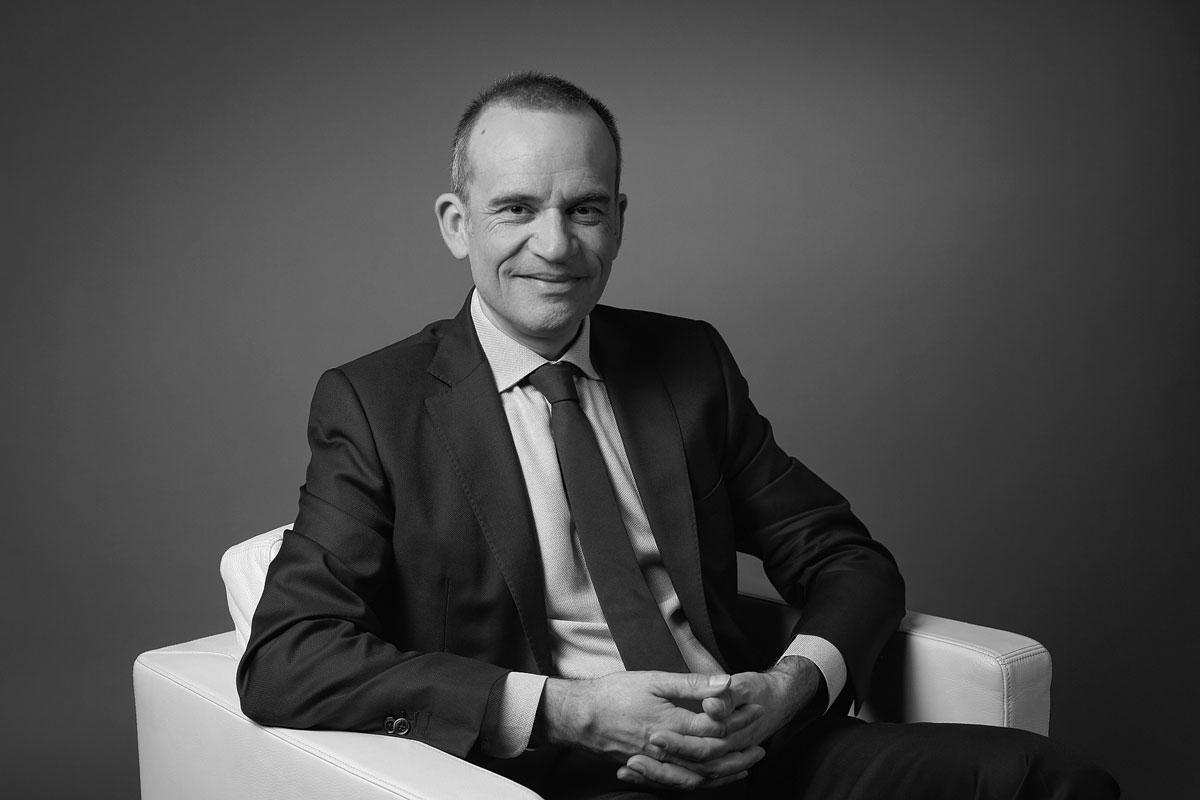
Dans l’intervalle, un démonstrateur construit sur le site ArcelorMittal de Hambourg par la société américaine Midrex, servira à peaufiner la technique de réduction directe. Comme le résume Eric Niedziela, “nos pré-études montrent que la réduction est atteignable avec 62% d’hydrogène. Le 100% devra être prouvé à Hambourg”. Dès 2023, le groupe vise une production de 100.000 tonnes de fer solide directement réduit.
Autre priorité: faciliter la circularité et la valorisation des déchets et sous-produits. A Gand, le procédé Torero, dont le site pilote est en chantier, visera à transformer par chauffage, dans un environnement pauvre en oxygène, des déchets forestiers en biochar, un coproduit riche en carbone apte à remplacer le coke dans le haut-fourneau. “Il faut se souvenir qu’un haut-fourneau peut durer un siècle, on ne va pas les arrêter demain”, pronostique Jean-Claude Herman, qui fut le CEO de CRM Group (un centre de recherche sur la métallurgie installé à Liège). “ArcelorMittal va devoir faire vivre les deux technologies côte à côte”, ajoute-t-il.
1,85 tonne
La quantité de CO2 émise pour la production d’une tonne d’acier, selon la World Steel Association.
Un surcoût de 20 à 30%
Un acier plus vert est, pour le moment, plus cher. Hybrit mise sur un surcoût de 20 à 30%. De son côté, ArcelorMittal estime que par rapport à une réduction directe au méthane, l’emploi d’hydrogène vert majore le prix de revient à la tonne de 150 à 250 dollars, pour un cours de l’acier qui tourne autour de 1.000 dollars. Mais les sidérurgistes constatent que le Système d’échange de quotas d’émission de l’Union européenne, par lequel les secteurs fortement émetteurs peuvent acheter les droits d’émettre, leur revient de plus en plus cher ; ils anticipent un durcissement qui les pénaliserait s’ils restaient passifs.
En outre, ils s’organisent, notamment via leur association Eurofer, pour que l’acier moins vertueux soit davantage régulé. “Si l’Europe veut être leader dans le management du risque climatique sur la planète, prévient Eric Niedziela, exprimant ainsi l’opinion de nombreux confrères, il ne faut pas laisser rentrer les importations qui n’ont pas le même système de régulation que le nôtre. Sinon, on est dans une concurrence complètement déloyale.”
L’enjeu est immense, et totalement inédit. “Bien sûr, les sidérurgistes ont toujours été dans une démarche pour limiter les émissions et l’énergie, pour être plus efficace et économe, relève Véronique Vitry, chargée de cours à la Faculté polytechnique de l’université de Mons. Mais avec l’hydrogène, on n’est plus dans l’incrémental, un pas après l’autre. On est dans une rupture de process.” S’ils le font, c’est parce que la pression politique est forte. Notamment celle émanant de la Commission européenne qui incite les Etats membres à viser la neutralité carbone pour 2050. Forte, la pression sociétale l’est aussi. Certains jeunes ingénieurs, par exemple, boudent déjà un secteur énergivore qui, à leurs yeux, n’agit pas assez pour l’environnement.
En s’engageant dans la combinaison réduction directe-fours électriques, la sidérurgie belge s’expose aussi davantage à la hausse des prix du gaz et de l’électricité. Or, l’Union européenne n’est pas connue pour l’abondance de ses réserves en hydrocarbures, et nombre de pays sont encore hésitants sur leurs choix énergétiques à venir. Comme le souligne un bon connaisseur du dossier, “les compagnies sidérurgiques, conformément aux voeux des autorités, considèrent la disponibilité en gaz naturel, mais aussi et surtout de l’électricité verte comme acquises, alors qu’aucun gouvernement ne traite le sujet au niveau où il devrait l’être.”
D’où un effort global pour mieux maîtriser les approvisionnements, incarné par exemple par Aperam, spécialiste des aciers inox en Belgique et en France. Utilisant comme matière première plus de 90% de ferraille qu’il fond dans des fours à arcs électriques, ce groupe a acquis il y a peu ELG, leader mondial de la collecte et du retraitement de l’inox. Affichant un engagement environnemental fort adossé à la certification Responsible Steel décrochée en septembre, Aperam a déjà installé des éoliennes sur plusieurs sites et déploie à Genk un vaste champ photovoltaïque qui couvrira jusqu’au parking. Au Brésil, l’entreprise alimente son haut-fourneau avec du charbon de bois d’eucalyptus qu’elle fabrique elle-même à partir de ses propres forêts certifiées. “Une fois ELG dans notre giron, plus de 30% de notre personnel travaillera dans le recyclage, la culture de forêt ou la valorisation des matières, précise Bernard Hallemans, CEO de l’activité acier inox en Europe. C’est un chiffre fort pour un soi-disant sidérurgiste, non?”