Vous vous êtes sans doute déjà assis sur un Fibrocit. Vous les trouverez à Bozar, à l’Ancienne Belgique, à Forest National ou dans les salles de l’Union européenne. Alliant savoir-faire, personnalisation et approche circulaire, cette entreprise de Marke, près de Courtrai, construit des sièges fixes sur mesure. “Parfois, aucun d’entre eux n’est identique.”
L’entreprise Fibrocit, basée à Courtrai, a fondamentalement changé au cours des dernières années. En 2015, le leader du marché Benelux des sièges fixes pour théâtre, cinémas et auditoriums, entre autres, a changé de propriétaire. L’entreprise appartient désormais à Benedict Geers. Et en 2023, Steven Stichelbout est devenu partenaire commercial et coassocié de la société holding au-dessus de Fibrocit.
Le duo d’entrepreneurs a des projets de croissance ambitieux pour cette entreprise vieille de 103 ans. “Nous voulons atteindre 100 employés à temps plein et ouvrir des ateliers de vente avec des équipes locales d’assemblage aux cinq coins du continent, explique Benedict Geers. Nous voulons devenir un opérateur dominant dans l’Union européenne, en concurrence avec les deux acteurs mondiaux, l’un espagnol, l’autre japonais. Ensuite, nous nous lancerons dans l’intercontinental avec la même formule.”
La période covid a pourtant bien coupé les jambes du fauteuil du CEO. “En mars 2020, tout a été annulé pour une durée indéterminée et nous n’avons même pas été autorisés à franchir la frontière pour travailler aux Pays-Bas, explique-t-il. J’ai dit à mes collaborateurs : ‘Je démissionne si vous ne restez pas en poste’. Comme tout le monde m’est resté fidèle, j’ai contracté des emprunts importants, jusqu’à 1,5 million d’euros. Aujourd’hui encore, les banques nous refusent tout capital de croissance jusqu’à ce que le dernier centime soit remboursé, en 2026.”
Mais Benedict Geers ne se laissera pas arrêter par cette situation. Il a cherché des capitaux externes pour son scénario de croissance. D’autant qu’en 2022, le chiffre d’affaires s’est normalisé. Selon le fournisseur d’informations économiques Trendstop, la marge brute de la société au-dessus de Fibrocit, MPRA, s’élève à 1,37 million d’euros. Grâce au rattrapage d’après covid, le chiffre d’affaires devrait continuer à augmenter, estime Benedict Geers. .
1 De vieux fauteuils comme matière première
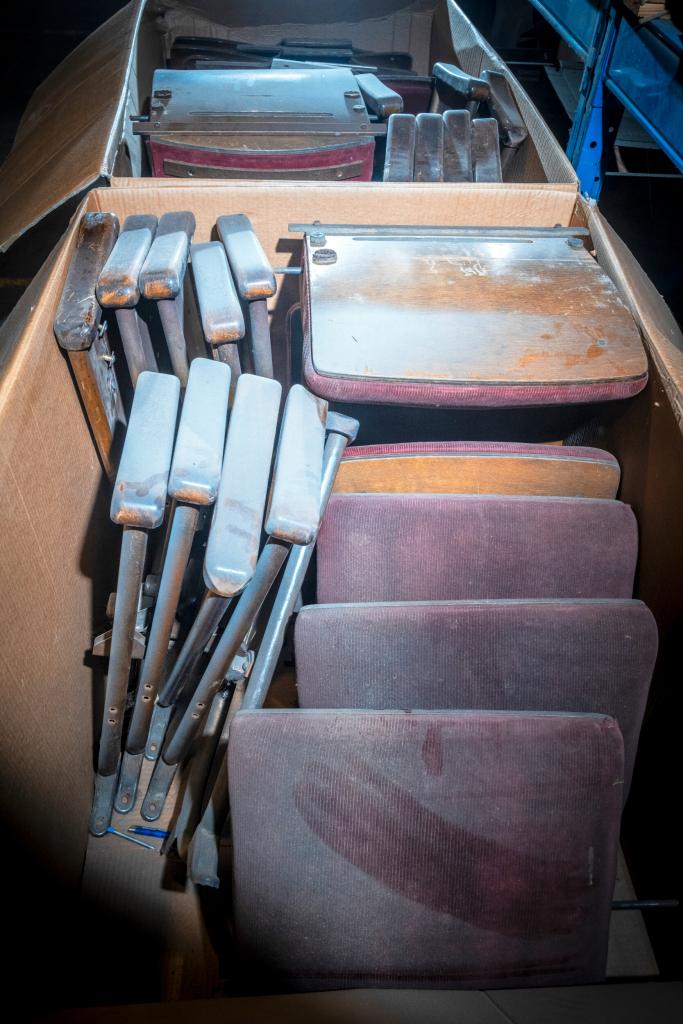
Fibrocit ne veut pas jeter les vieux fauteuils de théâtre, car dans une économie circulaire, ils constituent la matière première idéale pour la fabrication de nouveaux produits. De plus en plus de projets réutilisent du vieux matériel, déniché dans les salles. Dans l’atelier de Marke, ces fauteuils sont ensuite démontés manuellement.
2 Ponçage et décapage
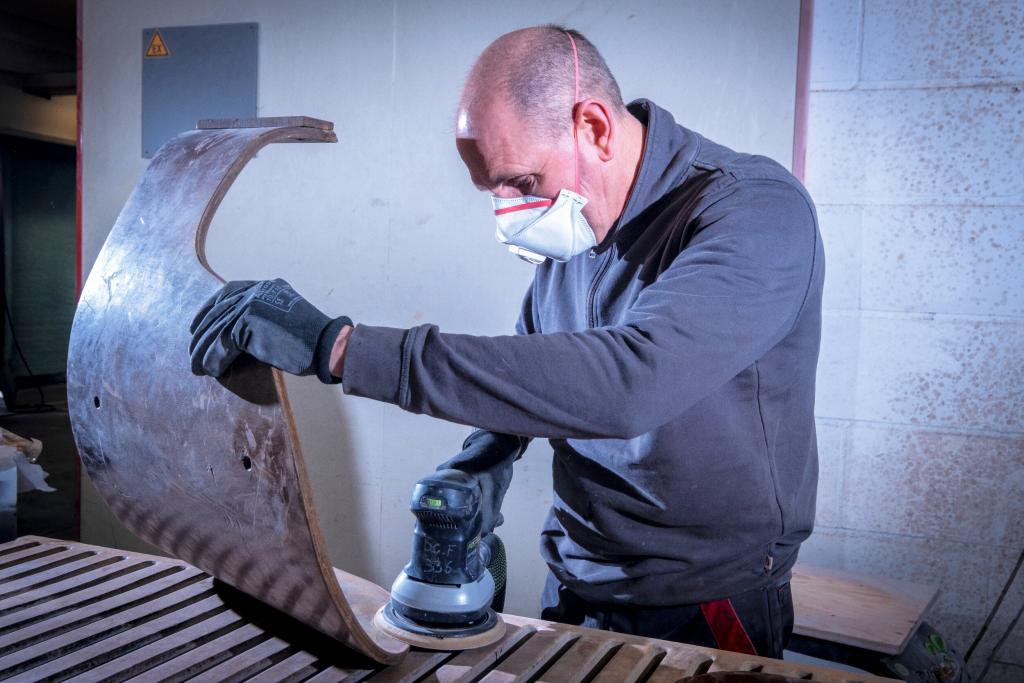
Le vieux bois est décapé et poncé. Les planches plates peuvent certes passer à la machine, mais toutes les pièces rondes et courbes doivent être poncées à la main. Les pièces métalliques, telles que les étaux, les écrous, les tiges, les ressorts hélicoïdaux, sont, elles, débarrassées de leur peinture et de la rouille qui parfois les recouvre.
3 Des pièces flambant neuves
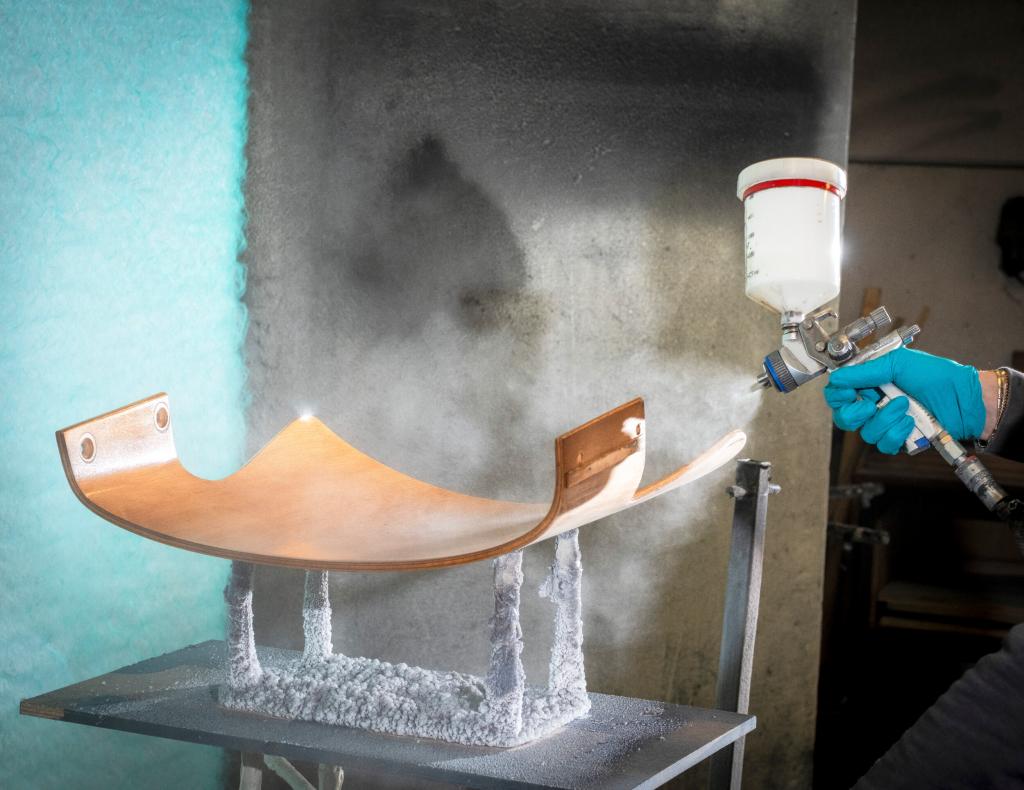
Le bois et le métal vierges reçoivent une nouvelle couche de peinture. La peinture au pistolet, travail d’expert, doit aussi être effectuée manuellement. Le défi? Ne pas pulvériser trop épais ni trop liquide et suffisamment vite pour obtenir un résultat uniforme. Après séchage, personne ne doit deviner que certains matériaux ont déjà été utilisés intensivement pendant 50 ans.
4 Mousse moulée sur mesure
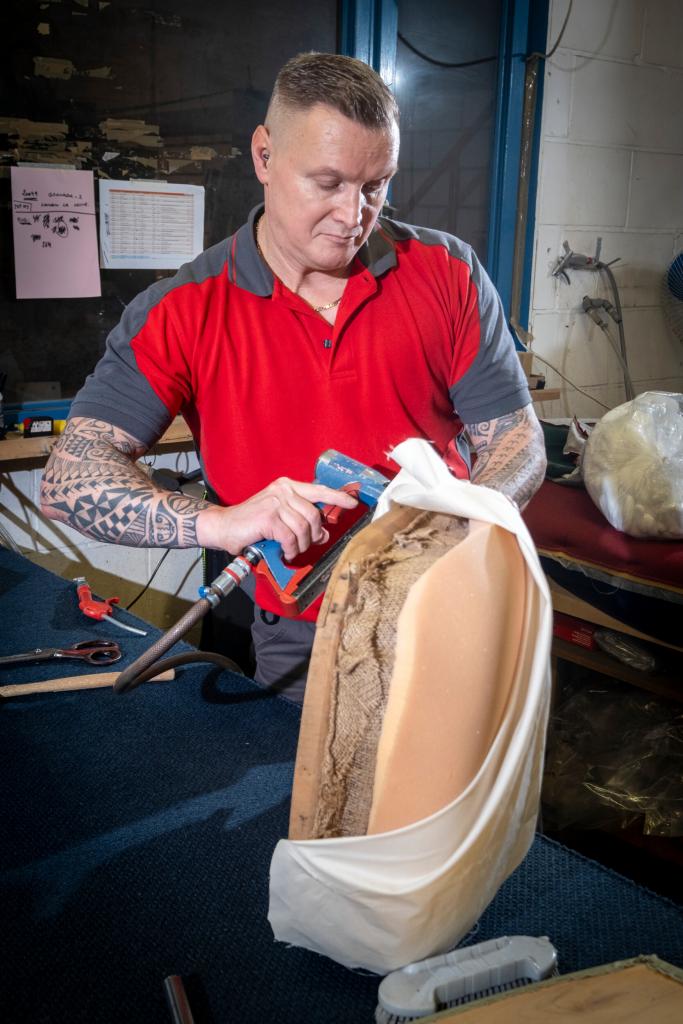
Il est temps de passer aux parties souples, au rembourrage et au tissu. La mousse moulée pour l’assise, le dossier et parfois les accoudoirs, est créée sur mesure, puis livrée à Marke. Elle est découpée en 3D sur place. Une colle à base d’eau est utilisée pour fixer la mousse à la base en bois, ou la mousse à la mousse moulée, créant ainsi une rainure dans laquelle les coutures vont disparaître.
5 L’homme l’emporte sur la machine
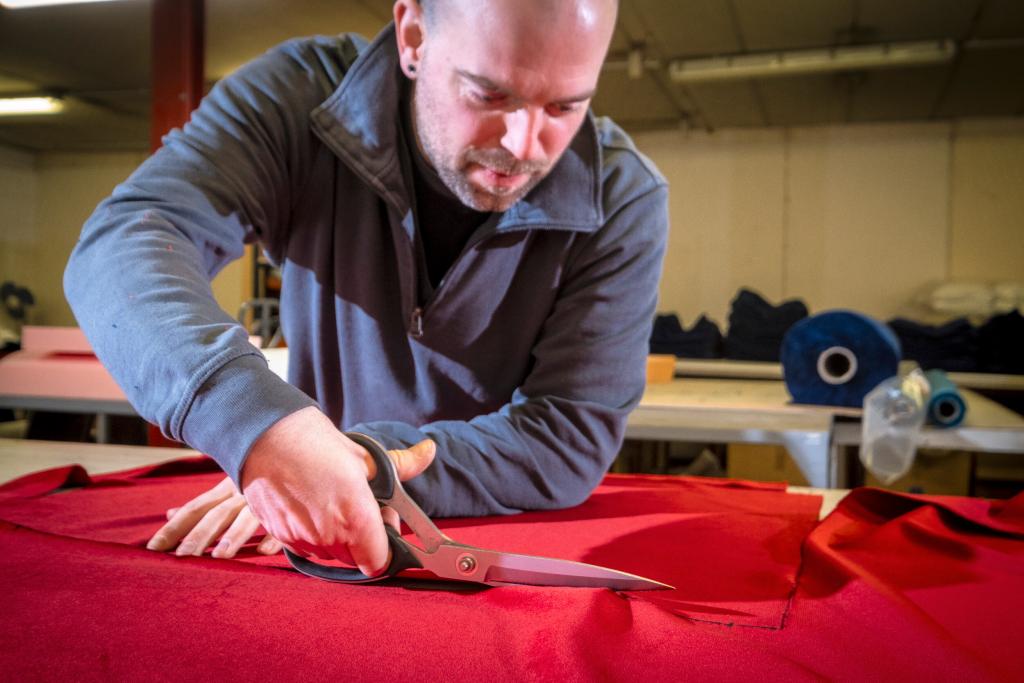
Le coupeur superpose plusieurs couches de tissu, d’une épaisseur pouvant aller jusqu’à 20 centimètres. Il découpe ce revêtement manuellement, plus rapidement qu’une machine ne pourrait le faire avec de telles quantités de tissu. L’étape suivante consiste à agrafer les tissus aux pièces de bois. Pour certains sièges, une couverture supplémentaire est aussi cousue.
6 Les fauteuils varient en taille
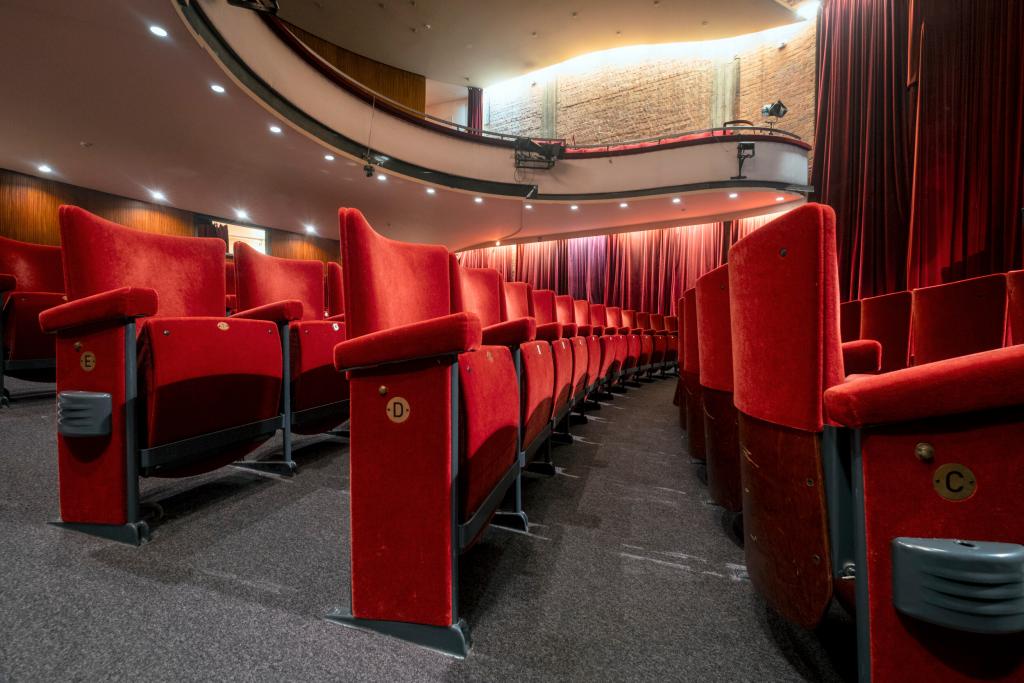
Douze semaines après la signature de l’appel d’offres, les pièces peuvent déjà être acheminées vers leur chantier de destination. Les artisans sont capables d’y installer en moyenne 50 fauteuils par jour, souvent avec des largeurs de siège – la taille centrale – et des hauteurs différentes. Ces inégalités sont nécessaires pour compenser les différences de hauteur de sol. En résultent des rangées de sièges d’une rectitude impressionnante, dans des salles remplies de manière parfaitement symétrique.