Chez City Sport, il n’y a pas d’employés anonymes. Bianca, Heidi, Aurica, Marleen, Chris, Veronique, Connie, Aldonna et 27 autres travailleuses et travailleurs de la production sont tous des spécialistes dans leur fonction. Leurs compétences respectives sont indispensables pour fabriquer 100.000 casquettes à la main par an. Le savoir-faire belge est reconnu dans le monde entier.
“Dans cinq ans, une casquette devrait s’appeler City Sport”, s’amuse Lowie Coffez. Avec son frère jumeau Artuur, il a repris la fabrique artisanale de casquettes de Tom Declercq au début de l’année 2024. L’entreprise appartenait à sa famille depuis 126 ans. “Nous sommes très heureux d’avoir réussi à nous passer d’investisseurs étrangers, déclare Lowie Coffez. Nous avons eu la chance que Tom nous apprenne beaucoup de choses, partage tous ses secrets et nous mette en relation avec tous les clients et les fournisseurs. Nous venons de rentrer de Milan et de Paris. C’est plutôt cool de voir nos casquettes au Bon Marché.”
L’entreprise basée en Flandre-Occidentale a connu une forte croissance au cours des 35 dernières années, pour atteindre un chiffre d’affaires de plus de quatre millions d’euros en 2023. City Sport se concentre sur les exportations, en particulier vers l’Europe, les États-Unis et le Japon. L’intérêt mondial s’explique en partie grâce au succès de la série britannique Peaky Blinders (BBC/Netflix) et à des célébrités telles que David Beckham et Matthew McConaughey, que l’on voit régulièrement porter des casquettes belges.
Artuur s’occupe de la création et du marketing. Lowie s’occupe des clients, des agents, des finances et de la gestion générale. “Chacun des 40 employés est un expert dans sa fonction. En même temps, il est bon d’avoir un œil plus frais et plus jeune. Nous voulons moderniser le marketing, le logo et le site web. Le processus de traitement des commandes peut être plus numérique et il est certain que l’analyse et l’optimisation de la production permettent de réaliser des gains. Nous sommes également attentifs à la durabilité. Nous ne travaillons qu’avec des tissus européens, nous coupons avec parcimonie, nous faisons traiter les surplus de tissu et nous expédions de la manière la plus écologique possible.”
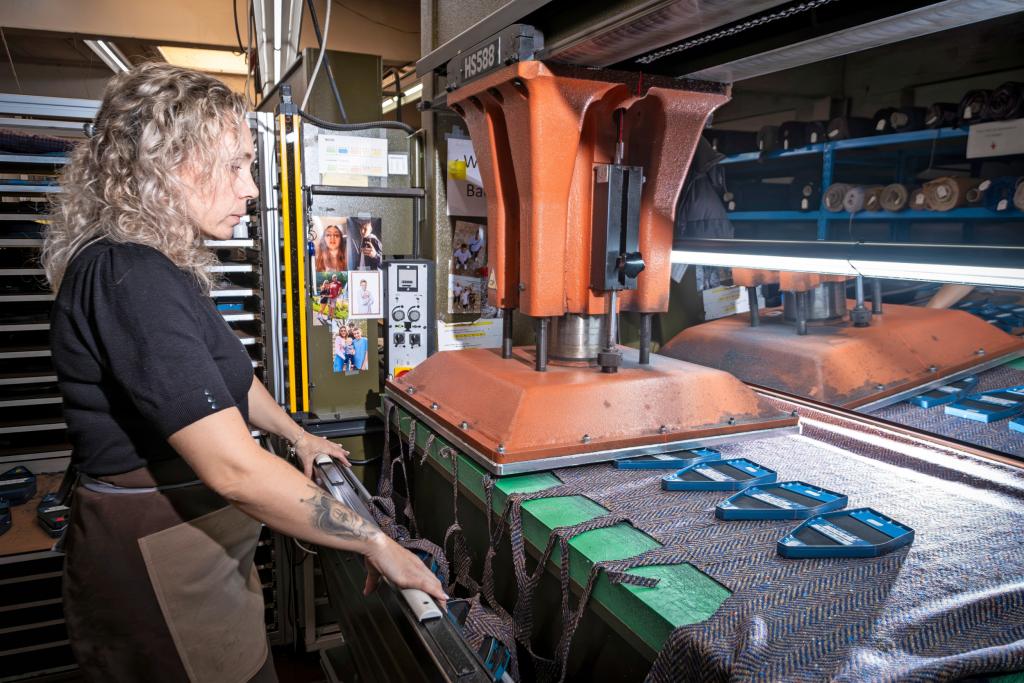
Chaque modèle a des formes différentes chez City Sport
Après un contrôle de la longueur et de la qualité des tissus entrants, les rouleaux sont coupés en bandes de 25 mètres. Les modèles peuvent ensuite être découpés dans le tissu. Une employée place avec précision les découpes métalliques sur le tissu. Elle tient compte des lignes et des formes pour que le motif soit régulier de la visière à l’arrière de la casquette. Chaque modèle et chaque taille nécessitent des formes différentes. La presse Atom imprime les formes dans le tissu.
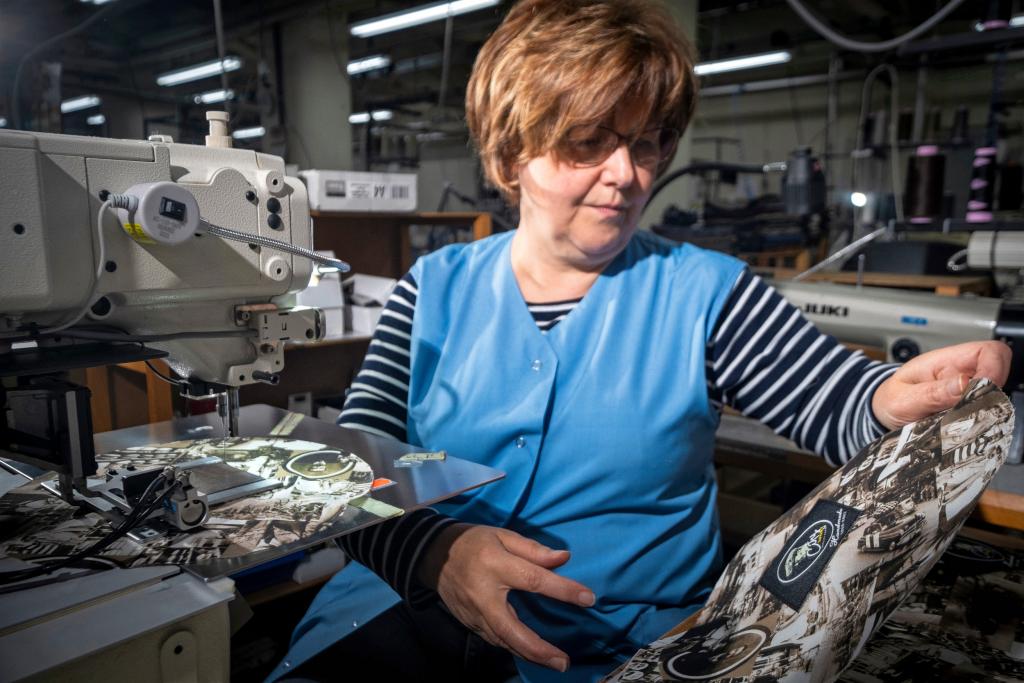
Un savoir-faire raffiné, également à l’intérieur de la casquette
Chaque saison, il y a environ cinq nouveaux tissus de doublure. Pour l’intérieur de la casquette, la doublure, les couches de protection imperméables pour les casquettes d’hiver et la bande de doublure sont cousues de manière experte. Un travail manuel minutieux. Plusieurs machines sont utilisées pour chaque opération. L’étiquette au centre de la casquette est cousue de manière automatique.
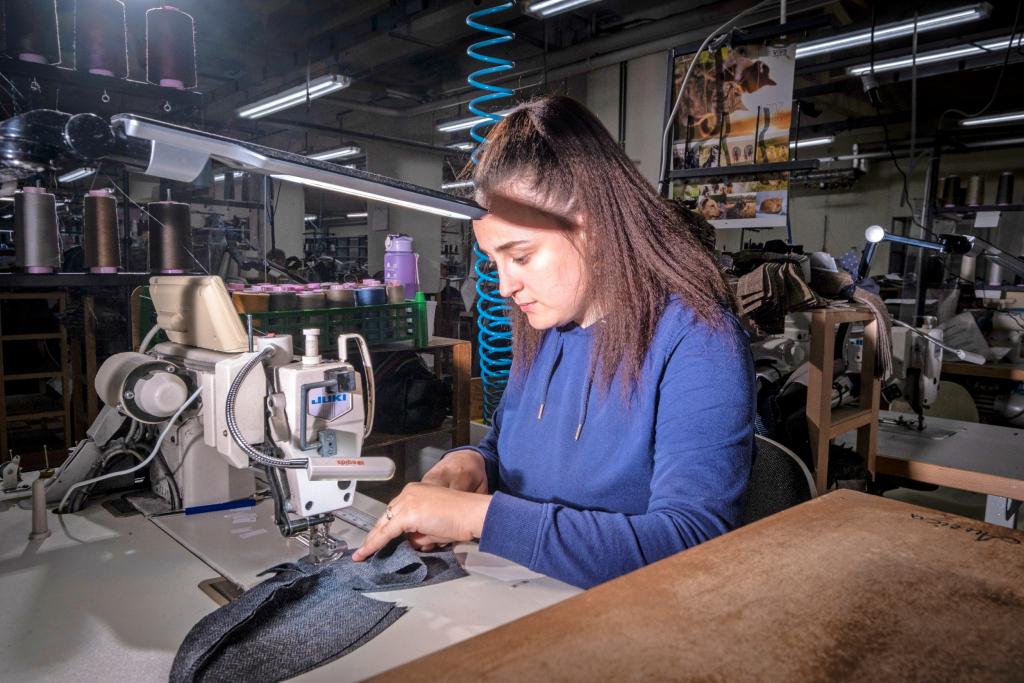
Un spécialiste pour chaque type de casquette
Chaque modèle a ses piqueuses attitrées. Par exemple, il est complètement différent de coudre une casquette plate ou une casquette à six ou huit pièces. Jusqu’à huit pièces de tissu sont cousues ensemble pour former l’extérieur de la casquette (ou couronne). Pour réaliser une visière de qualité, dure et souple, on y insère du texon. Malgré les différentes sections, le motif doit se suivre.
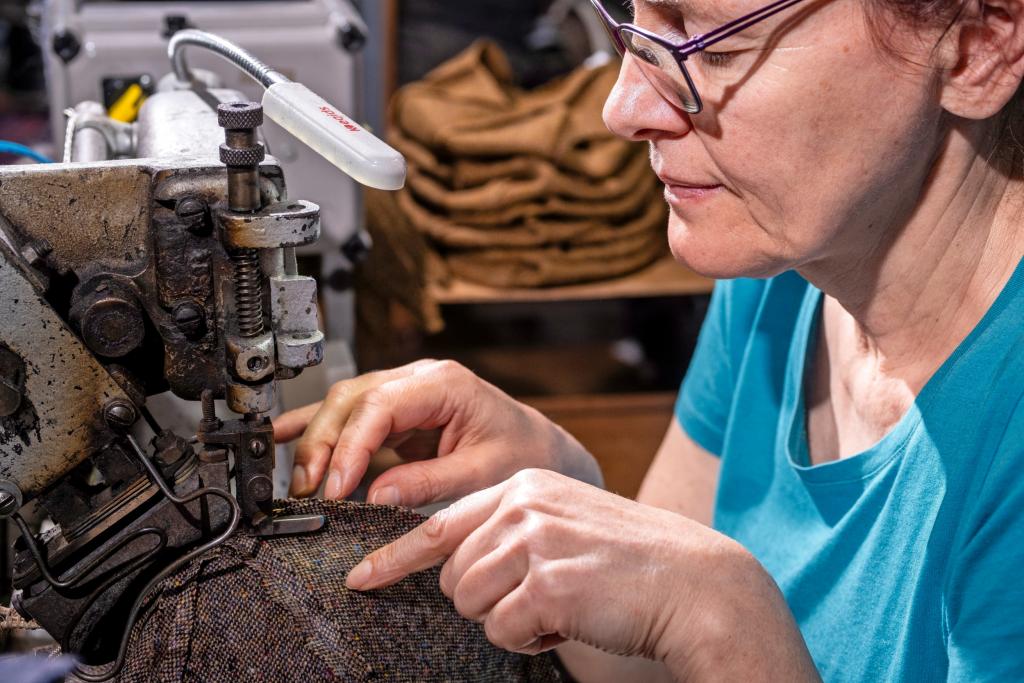
Chaque couture de City Sport doit être plate
L’une des plus anciennes machines est utilisée pour repasser les coutures de la couronne. Une fois le tissu correctement positionné, un tapis roulant tire la couture sur la résistance convexe à 180 degrés. Le repassage permet d’éviter l’apparition d’une couture laide et épaisse à l’endroit où deux pièces ont été cousues ensemble. Le fer à repasser est aussi parfois utilisé à d’autres étapes pour avoir le moins de plis possible.
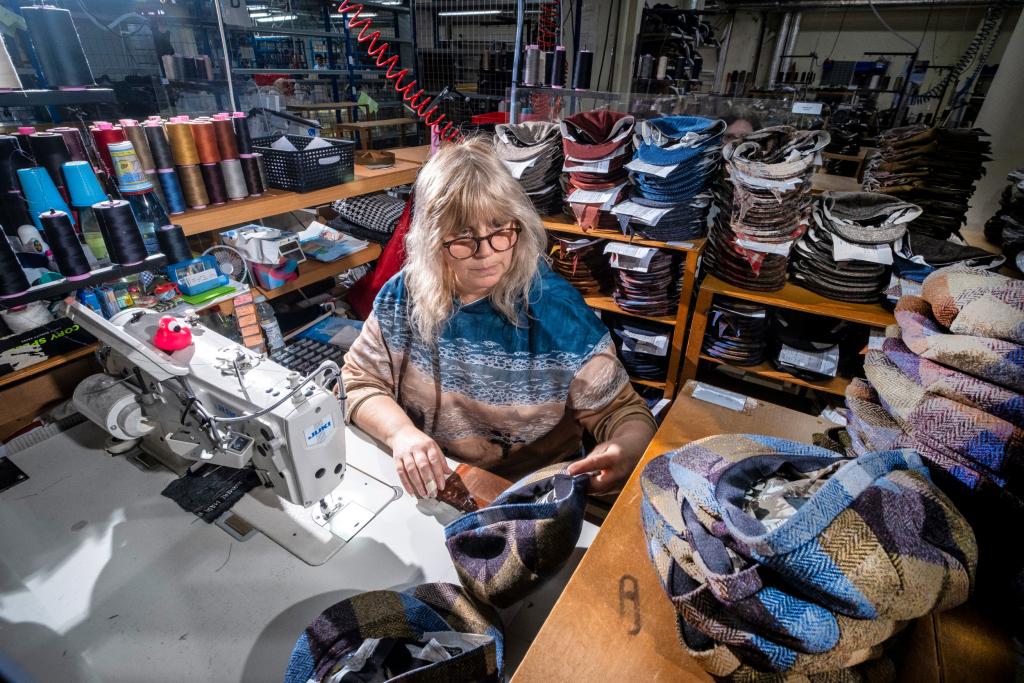
De l’intérieur à l’extérieur
Les casquettes en cours de fabrication sont amenées sur des chariots dans les allées étroites. Elles sont classées par autocollant, par commande, modèle, tissu et taille. La visière est d’abord fixée à la couronne. En option, un bouton peut être ajouté . Ensuite, l’intérieur et l’extérieur sont cousus ensemble, éventuellement avec une bande pour que la casquette adhère mieux à la tête. Les tissus de luxe européens, tels que le Donegal Tweed et le Harris Tweed, bénéficient d’une étiquette spéciale.
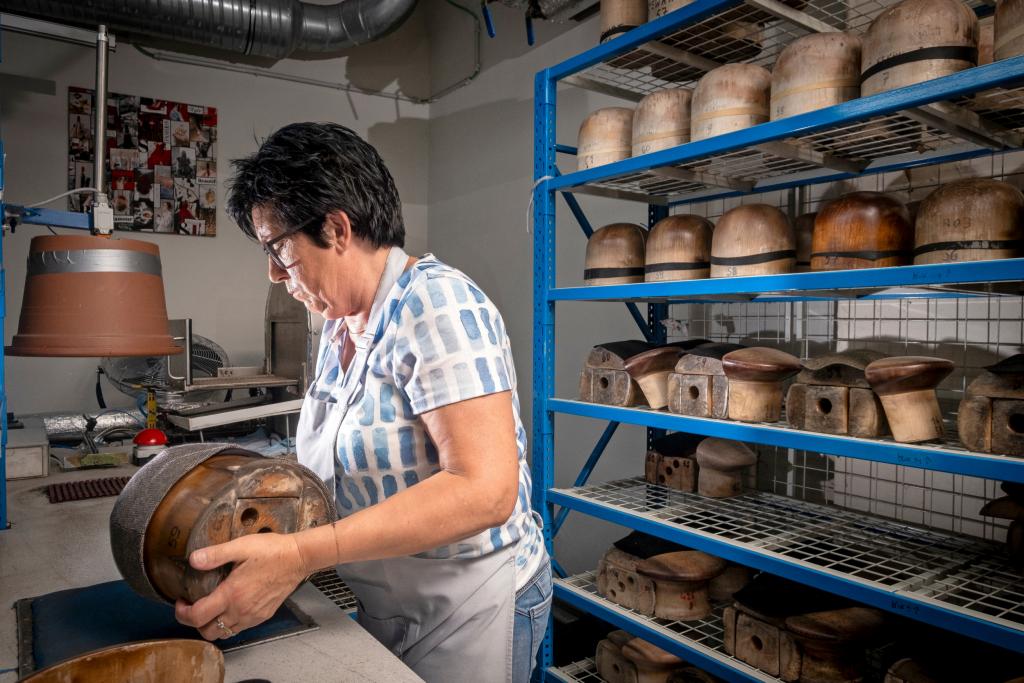
Le bain de vapeur donne la forme
La casquette prend sa forme définitive lors d’une ultime étape au cours de laquelle un employé pose la casquette encore plate sur un moule composé de cinq blocs qui forment la taille souhaitée. La casquette passe ensuite dans le four à vapeur pendant une minute, à une température de 96 degrés. Ensuite, la casquette est refroidie instantanément sous un pot en terre cuite et est placée sur une étagère. Ce processus lui donne sa forme définitive. Après le contrôle de qualité, la coupe des fils lâches et l’épinglage du pin’s avec le logo City Sport, la casquette est fin prête pour l’emballage et l’expédition.