Bienvenue sur le terrain synthétique de Lano. Depuis 35 ans, la société tapissière d’Harelbeke, en région de Courtrai, s’est tissée une réputation dans la production de gazon artificiel de qualité. Un produit en plein boom, tant auprès des particuliers que des clubs de sport. L’alchimie industrielle combine fibres en polyéthylène, latex, tests et respect des réglementations. Une ” success story “cousue de fil vert. Par Fernand Letist.
Gazon béni ou maudit ?
En pariant il y a 35 ans sur la production de gazon synthétique à côté de son offre de tapis et moquettes traditionnelles, Lano Carpets a eu le nez fin. Aujourd’hui, l’herbe artificielle a le vent en poupe. N° 2 sur ce créneau, l’entreprise de la région de Courtrai en produit 4 millions de m2 par an dont un million pour le sport, soit 50.000 m2 par jour, principalement destinés aux terrains de football, en Belgique et à l’international.
Sur les 110 millions de chiffre d’affaires annuel, un tiers provient du gazon. Le segment connaît un joli boom et se drape d’un argumentaire durable et responsable, valorisant le fait que le gazon artificiel ne nécessite aucune tonte, aucun arrosage, aucun entretien majeur, etc. Mais le gazon artificiel est également maudit par certains et suscite une certaine polémique car, sur les terrains, il est lesté (en proportions variables) de sable et, surtout, de granules de caoutchouc composées de résidus de pneus. Ces granules ont été soupçonnées d’être cancérigènes.
” Ce risque n’a à ce jour été ni infirmé, ni confirmé “, répond laconiquement, Johan Dewaele. Le conseiller R&D de Lano préfère épingler que ” depuis 20 ans, le gazon synthétique vit une vraie évolution qualitative des polymères de polyéthylène “. ” Cela permet des filaments plus épais, cos-tauds et résilients, ce qui est tout bénef pour nos clients, vu que la qualité des revêtements synthé-tiques est aujourd’hui bien supé-rieure qu’avant mais à un prix bien inférieur “, ajoute-t-il.
Et Lano, crampons belges bien plantés dans son gazon, n’a même pas peur de la concurrence asiatique qui s’accentue. ” Leurs frais de transport mettent leurs produits à un prix quasi équivalent aux nôtres. “
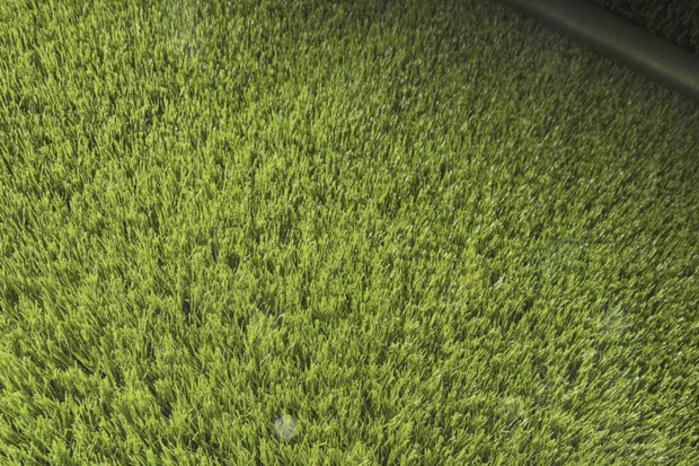
Lano.
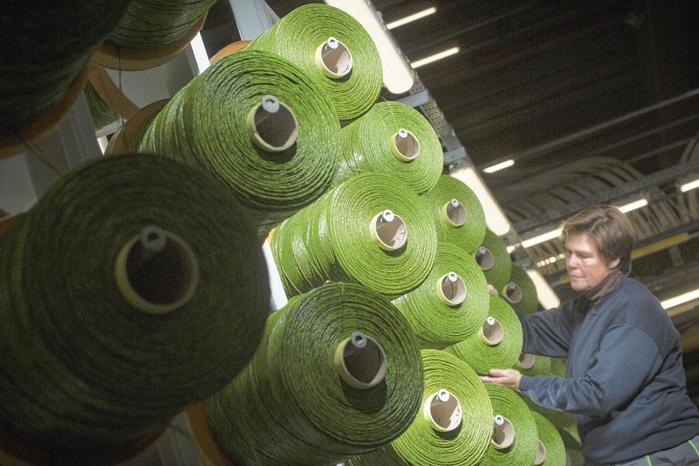
1. De fil en aiguille: Mille cinq cents tonnes. C’est ce que pèse le stock permanent de bobines de fil que l’entreprise réserve à sa production de gazon synthétique (pour terrains de sport et particuliers). Douze de ses machines de confection (sur 35) sont dédiées aux pelouses artificielles dont cinq uniquement aux surfaces sportives : hockey, tennis, rugby et… foot. Ce dernier, en été, mobilise trois machines. Les bobines de fil vert sont accrochées à une armature. L’employée supervise et noue chaque fil d’une bobine à la suivante pour garantir un déroulage continu vers la machine à coudre.
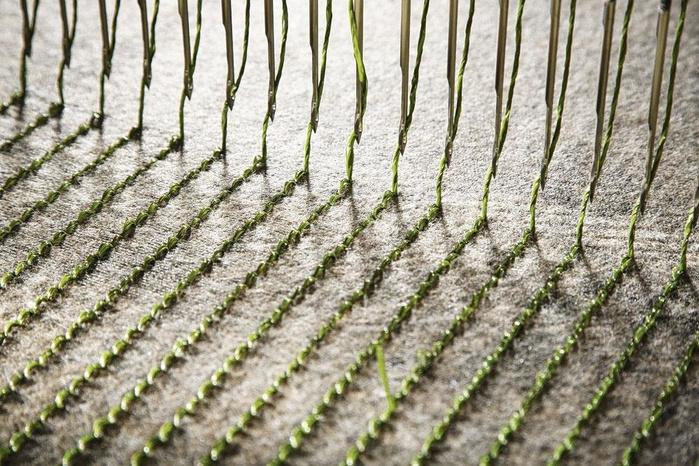
2. Le tuftage: Tufter, c’est enraciner l’herbe artificielle dans son support textile à l’aide d’une énorme machine à coudre. Ses aiguilles percent la toile (de 20 à 30 m de long sur 5 m de large), puis un crochet tire le fil et le met en boucle. Ensuite, un couteau sectionne la boucle en deux filaments. Pour le foot, la hauteur du gazon varie de 40 à 65 mm. Taille des brins, position des aiguilles, traçage ou non d’une ligne blanche sur le gazon…, toutes les données sont pilotées par ordinateur selon les désirs du client. Un em- ployé vérifie en permanence le respect de ces paramètres. Une autre machine coud ensuite les bandes de gazon entre elles pour arriver à la taille voulue. Le gabarit standard des bandes produites pour le foot est long de 60 à 70 m (soit la largeur d’un terrain) et large de 4,1 m.
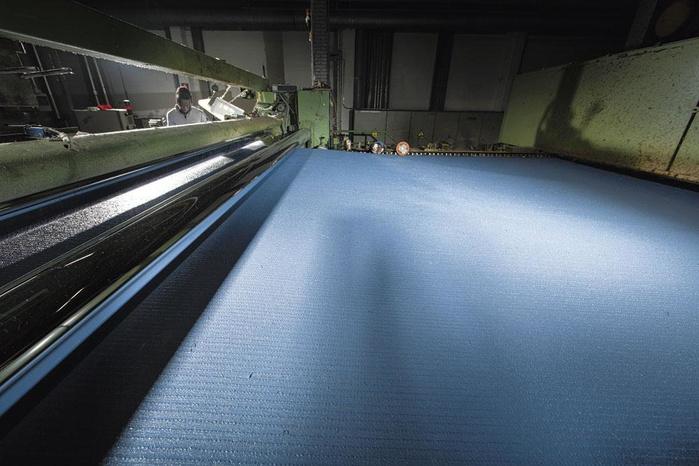
3. Un bain de latex: Une fois le gazon ” tufté “, direction le backing. L’opération consiste à enduire la face arrière du support d’une couche adhérente de latex liquide, déposée par de larges rouleaux tournant dans un bain. Le latex sert à arrimer fortement au support textile les filaments d’herbe synthétique cousus. Sorti de sa trempette, le revêtement file au sauna : deux fours successifs (un de 10 m et un de 60 m) qui réalisent son séchage intégral et confèrent au tapis d’herbe synthétique sa résistance idéale. Ainsi rigidifié, ce caoutchouc peut tenir jusqu’à 15 ans, là où les herbes artificielles survivent rarement au-delà des huit ans garantis d’usage normal, soit 1.500 heures par an.
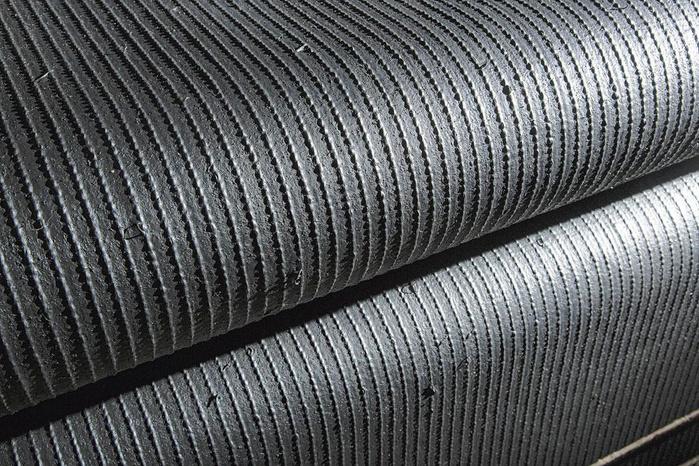
3. Un bain de latex: Une fois le gazon ” tufté “, direction le backing. L’opération consiste à enduire la face arrière du support d’une couche adhérente de latex liquide, déposée par de larges rouleaux tournant dans un bain. Le latex sert à arrimer fortement au support textile les filaments d’herbe synthétique cousus. Sorti de sa trempette, le revêtement file au sauna : deux fours successifs (un de 10 m et un de 60 m) qui réalisent son séchage intégral et confèrent au tapis d’herbe synthétique sa résistance idéale. Ainsi rigidifié, ce caoutchouc peut tenir jusqu’à 15 ans, là où les herbes artificielles survivent rarement au-delà des huit ans garantis d’usage normal, soit 1.500 heures par an.
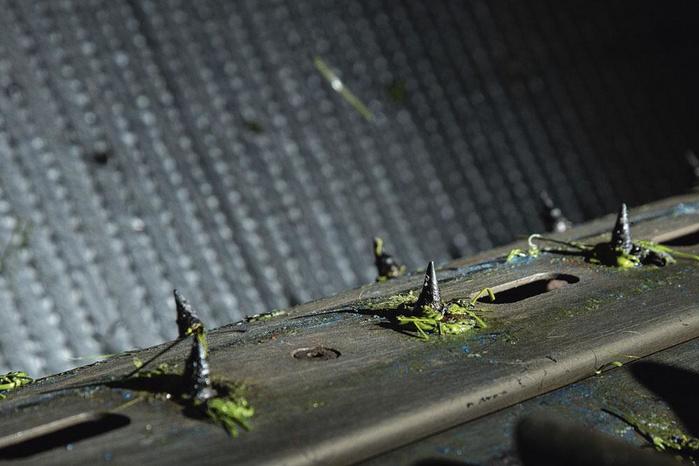
4. Des trous pour le drainage: Pour éviter le bain de pieds lors de son utilisation, le revêtement doit pouvoir évacuer l’eau en cas de pluie. Un rouleau hérissé de pointes de métal se charge de perforer le support latexé de trous de 4 mm de diamètre, tous espacés de 10 cm. ” Ce sont les meilleures dimensions, testées et validées pour tous nos gazons synthétiques “, précise le spécialiste R&D de Lano, Johan Dewaele. Et en dessous, faut-il un drainage vertical ou horizontal ? Tout dépend de la nature du sol. En Belgique, l’eau peut s’évacuer verticalement grâce à nos sols perméables, contrairement à l’Italie où beaucoup de clubs optent pour un système d’évacuation horizontal, plus complexe à mettre en place.
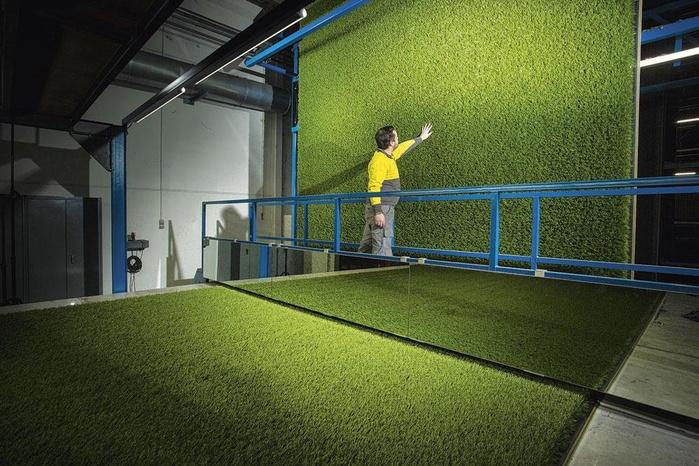
5. Le contrôle qualité: Après ce traitement, les bandes de gazon défilent lentement – verticalement, à plat, puis à nouveau verticalement – sous l’oeil d’un contrôleur. De sa passerelle, il peut tout voir du produit fini, notamment grâce à un miroir large et vertical lui offrant une visualisation du tapis dans les deux sens. L’employé traque surtout les décalages de couleurs et les fils manquants. Parfois, il passe aussi la main dans la pelouse synthétique pour en vérifier la densité et la solidité de l’ancrage des brins. Jugée prête à servir, la pièce est ensuite roulée, emballée et stockée jusqu’à livraison dans les racks géants des 200.000 m2 d’entrepôts.
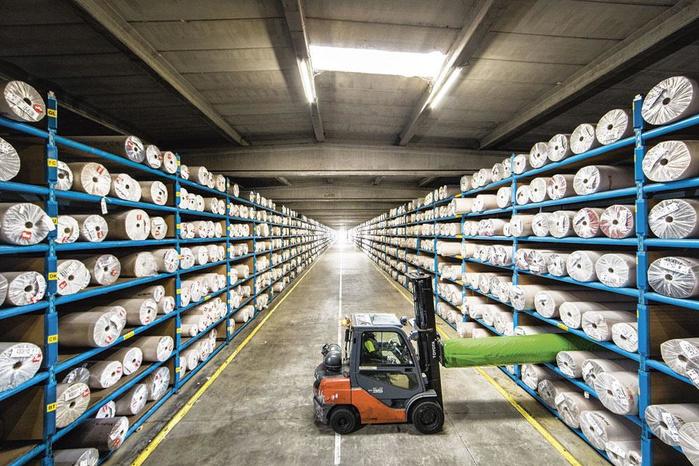
5. Le contrôle qualité: Après ce traitement, les bandes de gazon défilent lentement – verticalement, à plat, puis à nouveau verticalement – sous l’oeil d’un contrôleur. De sa passerelle, il peut tout voir du produit fini, notamment grâce à un miroir large et vertical lui offrant une visualisation du tapis dans les deux sens. L’employé traque surtout les décalages de couleurs et les fils manquants. Parfois, il passe aussi la main dans la pelouse synthétique pour en vérifier la densité et la solidité de l’ancrage des brins. Jugée prête à servir, la pièce est ensuite roulée, emballée et stockée jusqu’à livraison dans les racks géants des 200.000 m2 d’entrepôts.
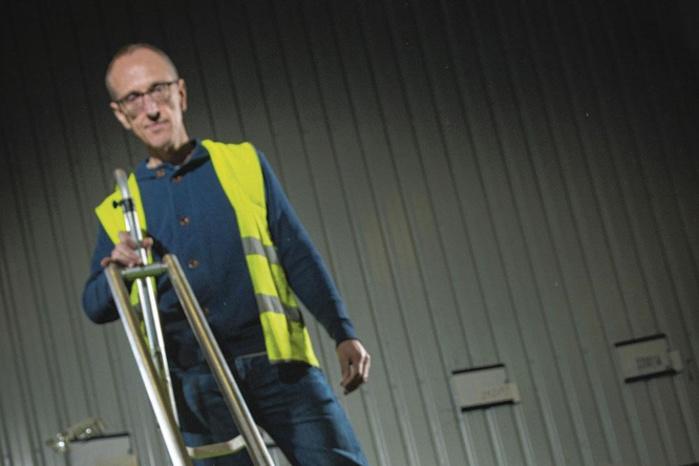
6. Règles et usure: Lano dispose d’un labo et d’une mini-salle simulant les conditions de terrain pour tester les qualités techniques de différents types de gazon, certaines d’entre elles étant réglementaires. Par exemple, l’herbe artificielle doit garantir un certain rebond du ballon et celui-ci doit pouvoir rouler au minimum sur 4 mètres et au maximum sur 10. Le gazon est testé aussi bien sec que mouillé. Une autre batterie de tests porte sur la résistance à l’usage. Pour ce test, des échantillons de gazon sont lestés de sable et de billes de caoutchouc, puis passés dans des machines à cylindres munis de crampons. Les échantillons sont piétinés par phases de 5.000 à 20.000 allers-retours.