Brabantia a vu le jour il y a un siècle. Depuis lors, l’entreprise familiale néerlandaise a su se rendre incontournable sur la scène internationale et donne le ton sur le marché des articles ménagers. Un de ses produits phares, la poubelle newIcon, est fabriqué en Belgique.
La filiale belge, poids lourd du groupe
L’entreprise familiale Van Elderen & Co, créée en 1919 dans la ville néerlandaise d’Aalst, s’est hissée au rang international. Elle est aujourd’hui gérée par le CEO Tijn van Elderen, représentant de la quatrième génération. Au début, l’usine fabriquait essentiellement des cruches à lait, des passoires et des entonnoirs. Au siècle dernier, elle a élargi et diversifié son assortiment d’articles ménagers. Tous les composants plastiques et tous les produits destinés au tri des déchets sont fabriqués à Overpelt. La filiale de Brabantia S&L Belgium à Overpelt a réalisé en 2017 un chiffre d’affaires de 73,5 millions d’euros, soit environ deux tiers du chiffre du groupe tout entier. Brabantia, dont le siège est sis à Valkenswaard, lance chaque année près de 150 nouveaux produits. Le centre de distribution d’Overpelt dessert 85 pays. En 2018, Brabantia a acquis Dutchdeluxes, une entreprise d’Eindhoven spécialisée dans les articles de cuisine design. Au mois de mai, Brabantia a reçu du roi Willem-Alexander des Pays-Bas l’autorisation d’utiliser le qualificatif de “royal”. Autrefois purement fonctionnels, les articles ménagers se doivent aussi, à l’heure actuelle, d’être design. ” La planche à repasser, l’étendoir, la poubelle font désormais partie intégrante de la décoration intérieure, affirme le COO Gijs Lathouwers. Depuis 2012, nos ventes en ligne ont augmenté de 5 à 45%. “
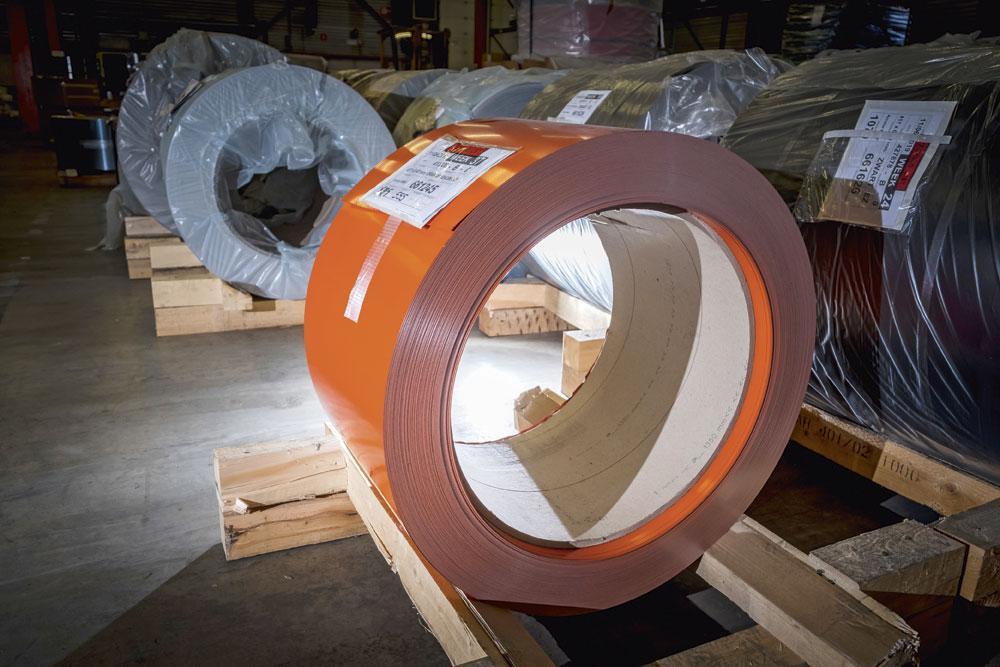
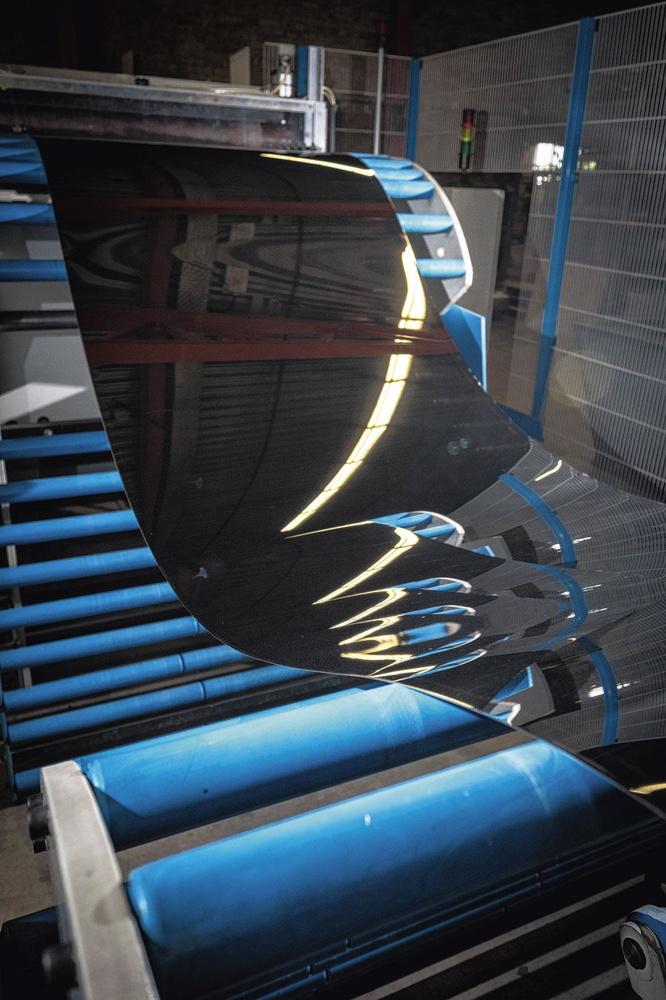
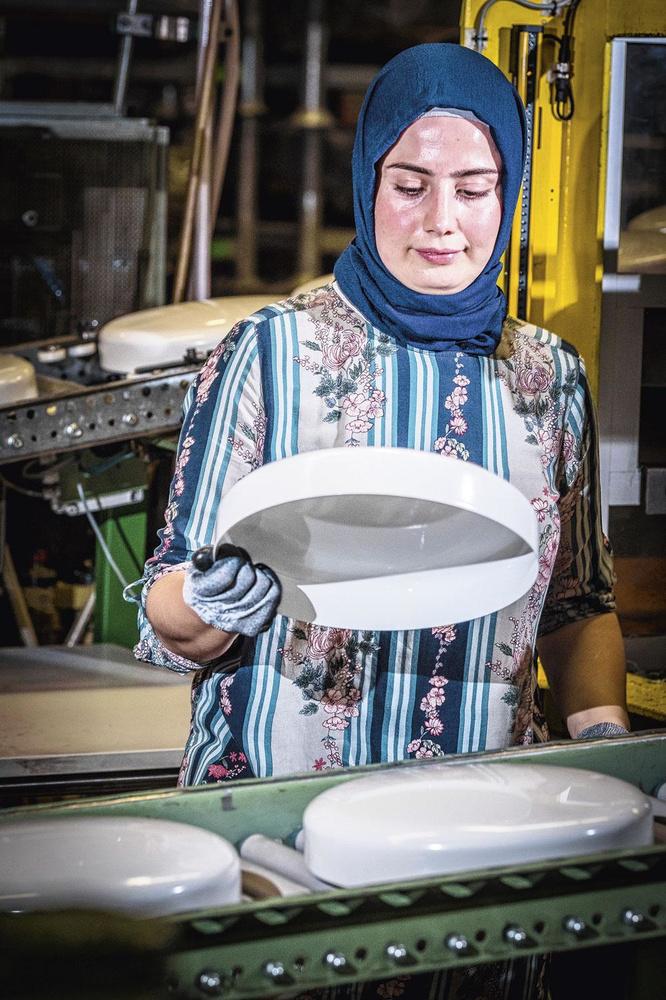
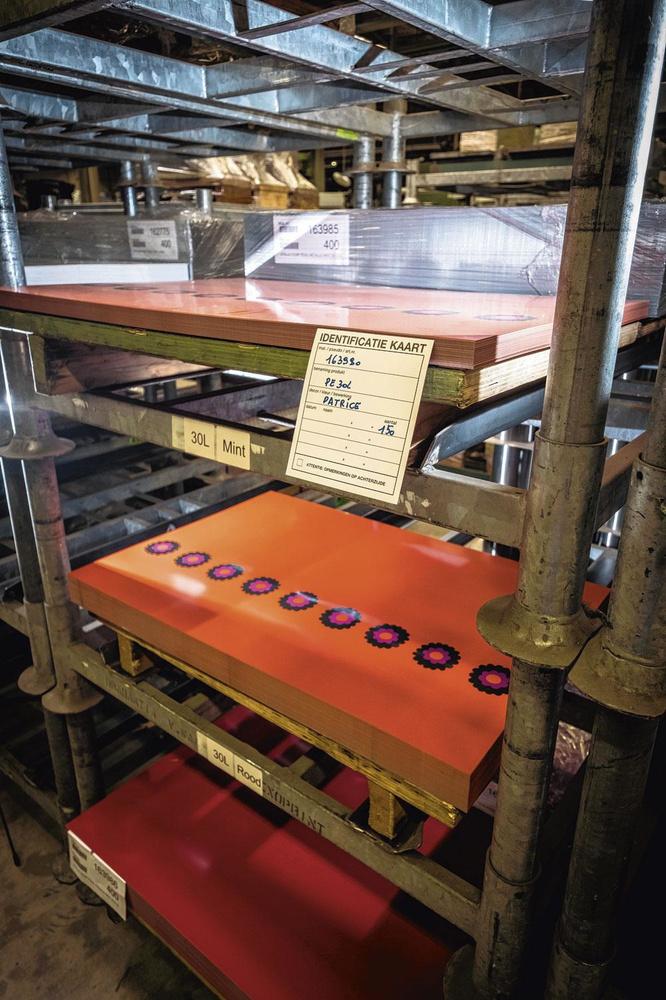
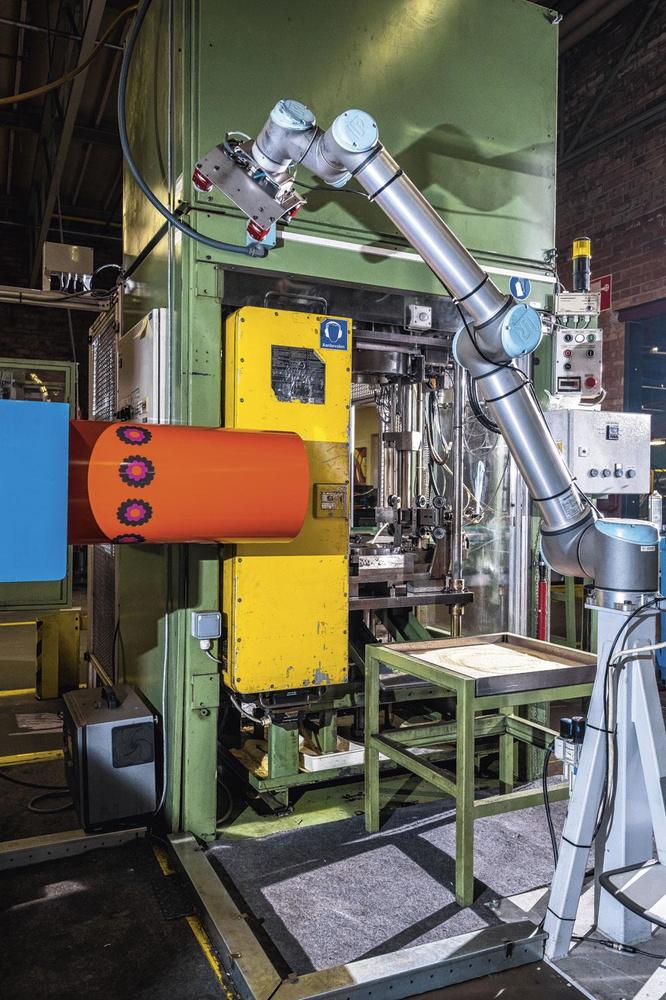
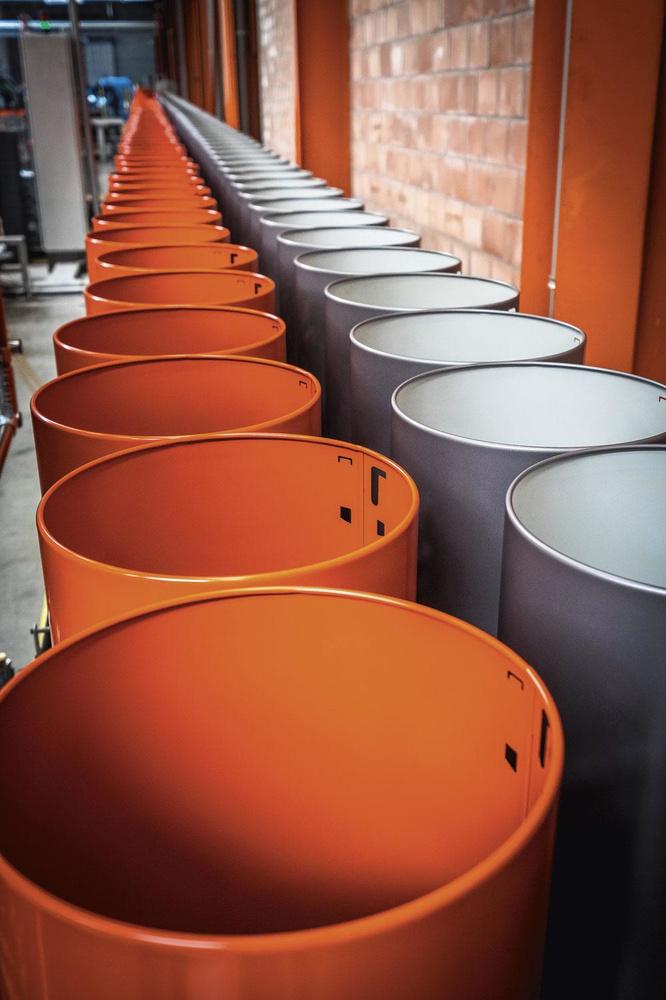
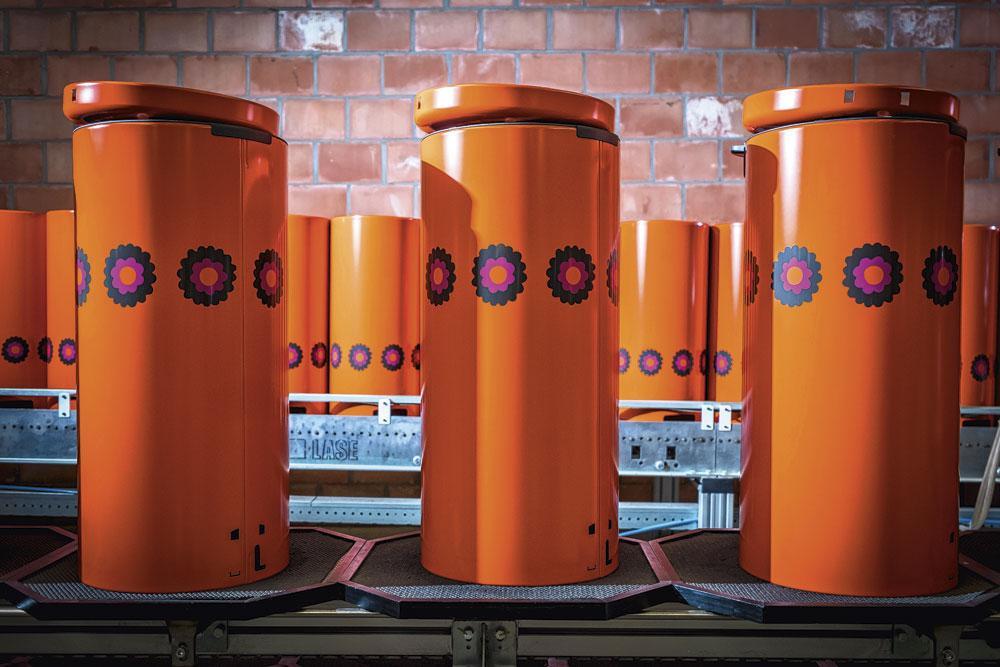
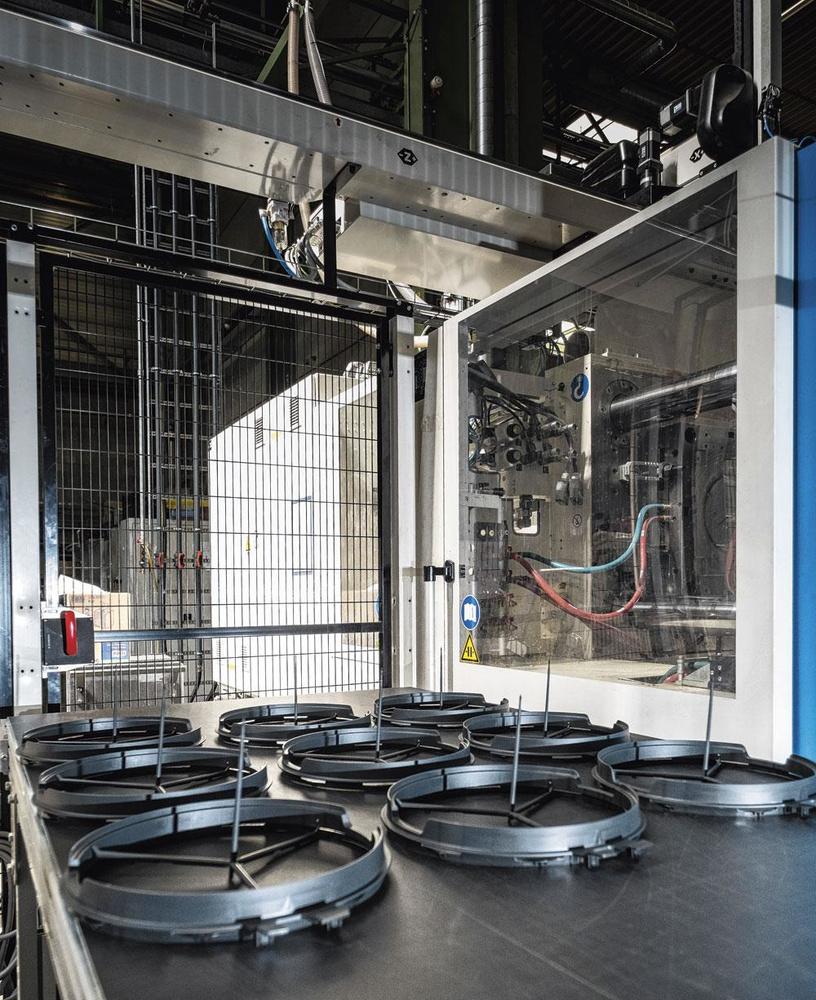
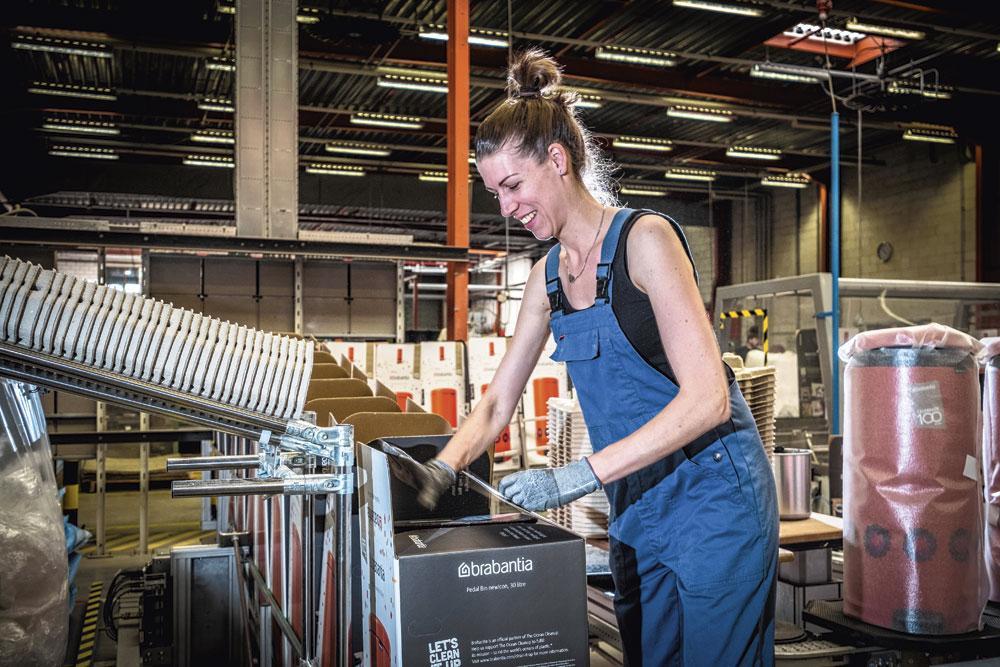
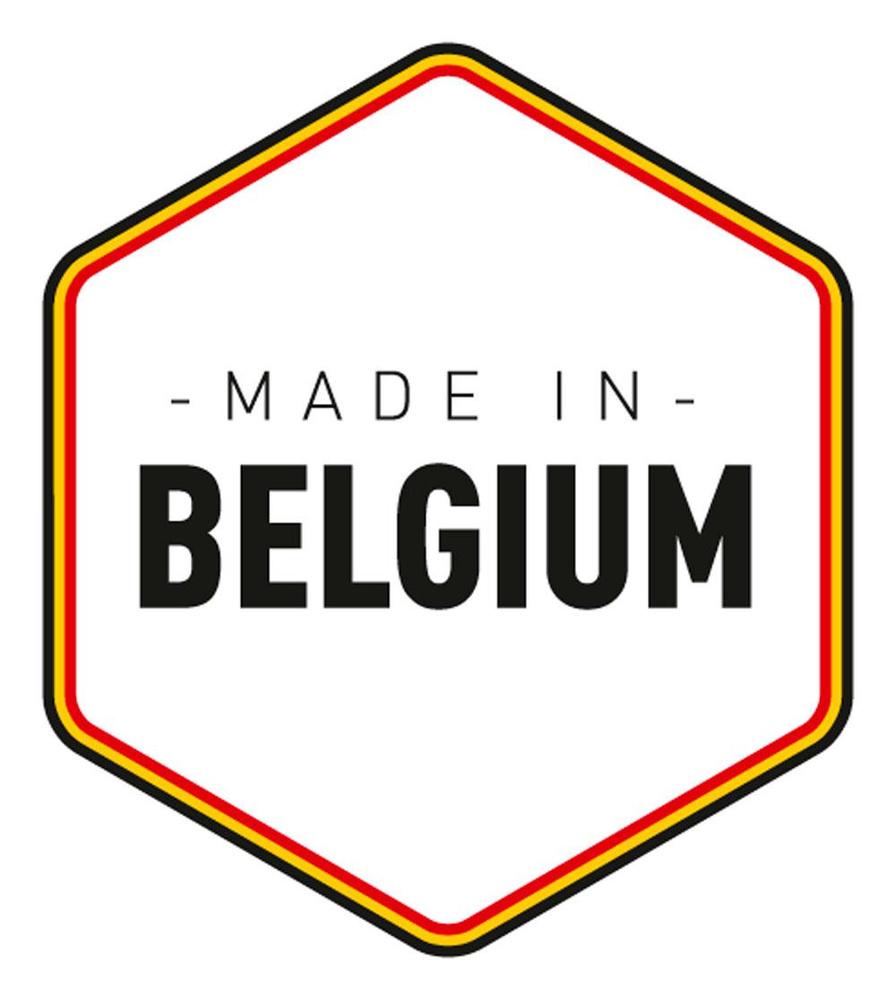