Le groupe suédois Mölnlycke est un leader mondial en fourniture au milieu médical de produits hospitaliers à usage unique. La crise du coronavirus a mis à contribution son usine belge de Waremme, pivot européen de sa logistique et de sa production, notamment pour les champs opératoires stériles. Parcours au coeur de la fabrication kilométrique et ininterrompue de l’étanche et absorbante toile bleue.
Soins intensifs
Le groupe suédois Mölnlycke Health Care (MHC, 8.000 personnes dans le monde) est présent depuis 44 ans à Waremme, ayant racheté aux Américains l’usine Arrow qui produisait des chemises. L’usine belge produit aujourd’hui 13% de l’assortiment global des produits MHC mais elle est aussi le siège européen polyvalent en logistique, service clientèle et chaîne d’approvisionnement. Le groupe Mölnlycke est présent sur deux segments. D’une part, les ” soins de plaie “, la première spécialité de la société originelle fondée en 1849. Les ” soins de plaie ” consistent principalement en des pansements et sont produits en Finlande, en Grande-Bretagne et aux Etats-Unis. ” Ces produits pèsent plus lourd que le volet chirurgical dans le chiffre d’affaires “, précise Alain Biston. D’autre part, le chirurgical, dont l’usine de Waremme fait partie. ” Mölnlycke produit également des gants chirurgicaux en Malaisie et des casaques en Thaïlande, ajoute le directeur général belge. La gamme est encore complétée par différents équipements de protection : masques, surchaussures, charlottes, etc., tous fabriqués par des sous-traitants en Asie. ” Mölnlycke joue aussi un rôle international important dans l’accompagnement de la pandémie du coronavirus. ” Comme fournisseur d’équipements de protection individuelle, la situation évolutive de la crise sanitaire a mis à rude épreuve nos flux de production et notre logistique, souligne Jenny Johansson, la directrice corporate communications de MHC. Notre priorité absolue est de maintenir en toutes circonstances les livraisons à nos clients et nous assurer que les professionnels de la santé soient correctement équipés. La pandémie a causé des tensions sur l’offre et la production de certains produits en raison de la très forte demande. Nous avons dû adapter notre logistique et accélérer des livraisons par fret aérien. ” L’usine de Waremme qui emploie 350 personnes a, de son côté, continué la production de sa spécialité : les champs hospitaliers et compresses stériles. Mais à une cadence un peu moins soutenue du fait du report des chirurgies électives (non urgentes) entraîné par le recentrage hospitalier sur la crise coronavirale. L’usine belge a continué à produire ses champs, malgré les mesures de confinement, grâce à une spécificité : ” Nous avons 120 opérateurs machines formés en interne. Chacun d’eux fonctionne en solo, par poste, en mode d’autonomie sans management. Chacun est à même de solutionner 80% des éventuels problèmes de sa machine “, explique Alain Biston.
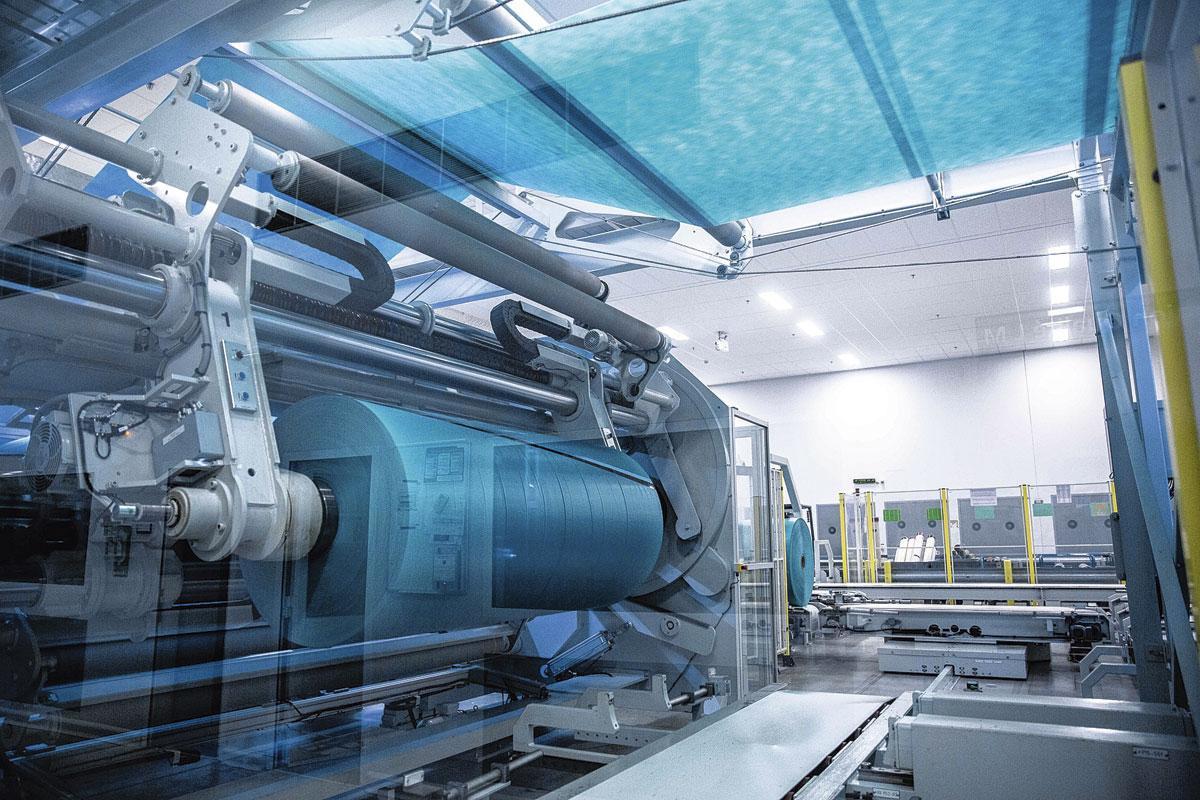
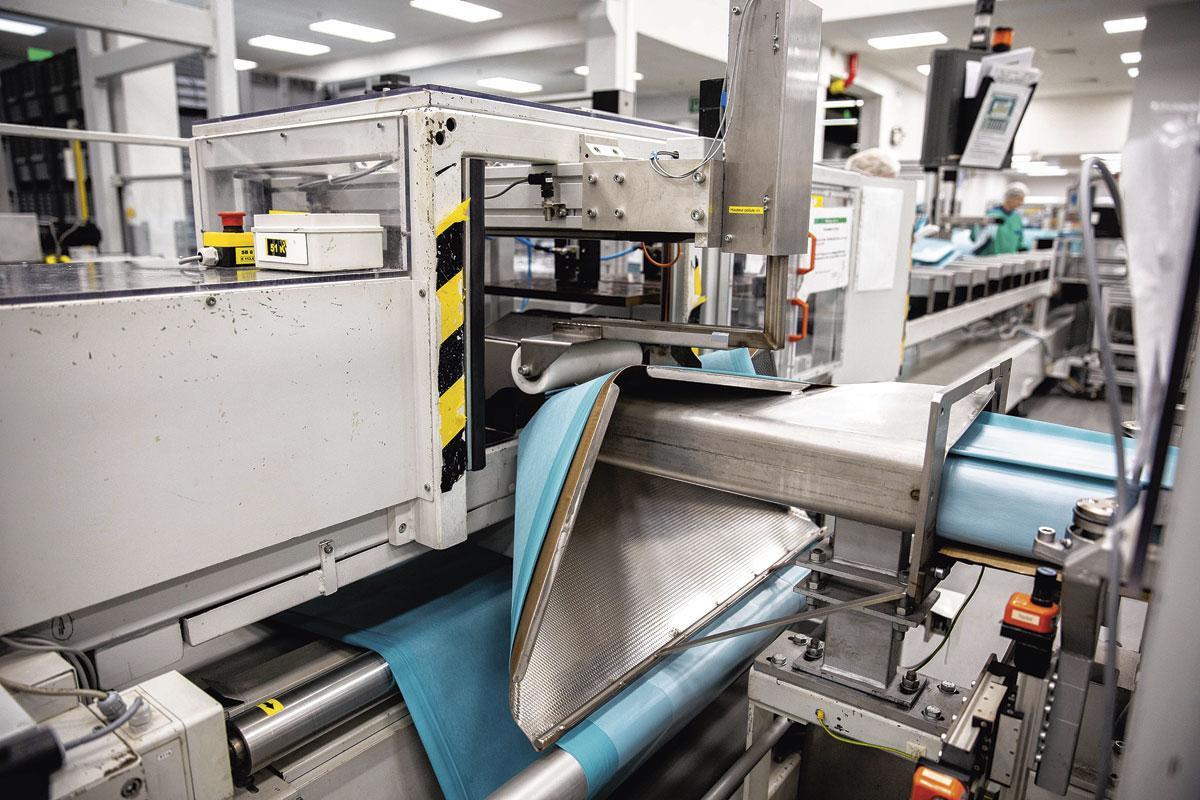
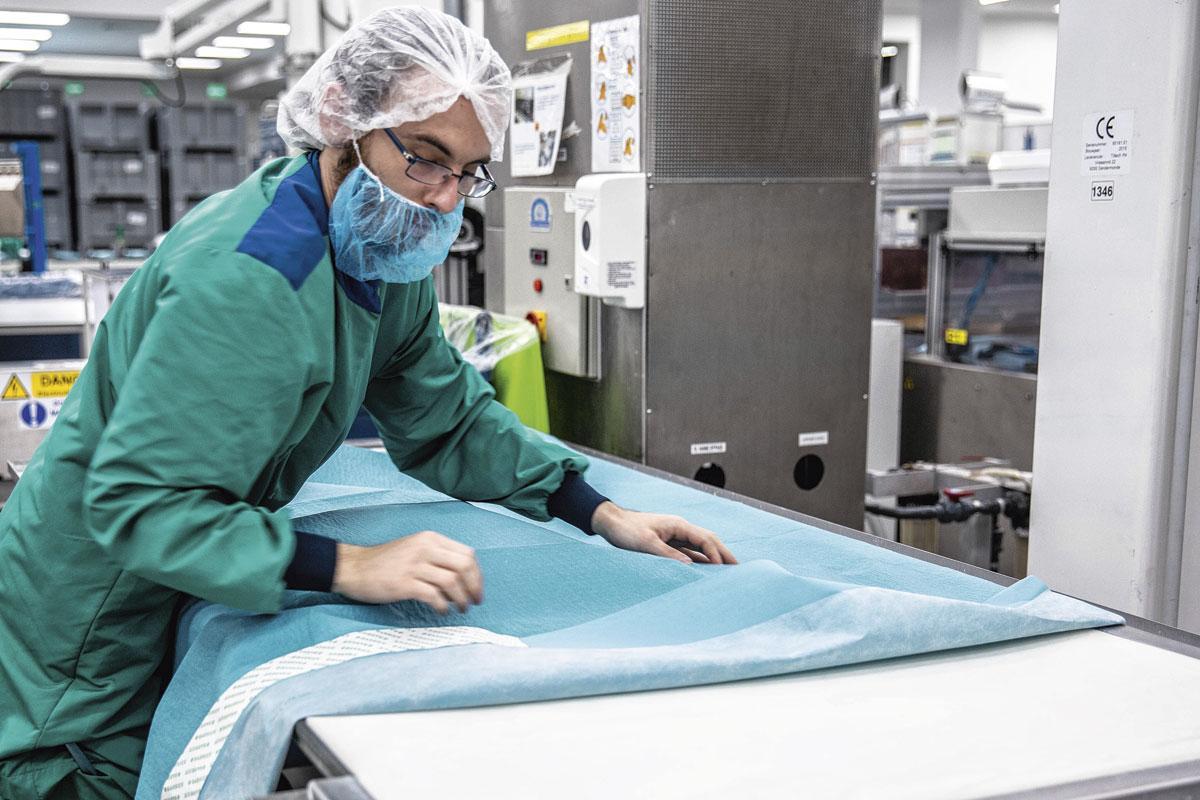
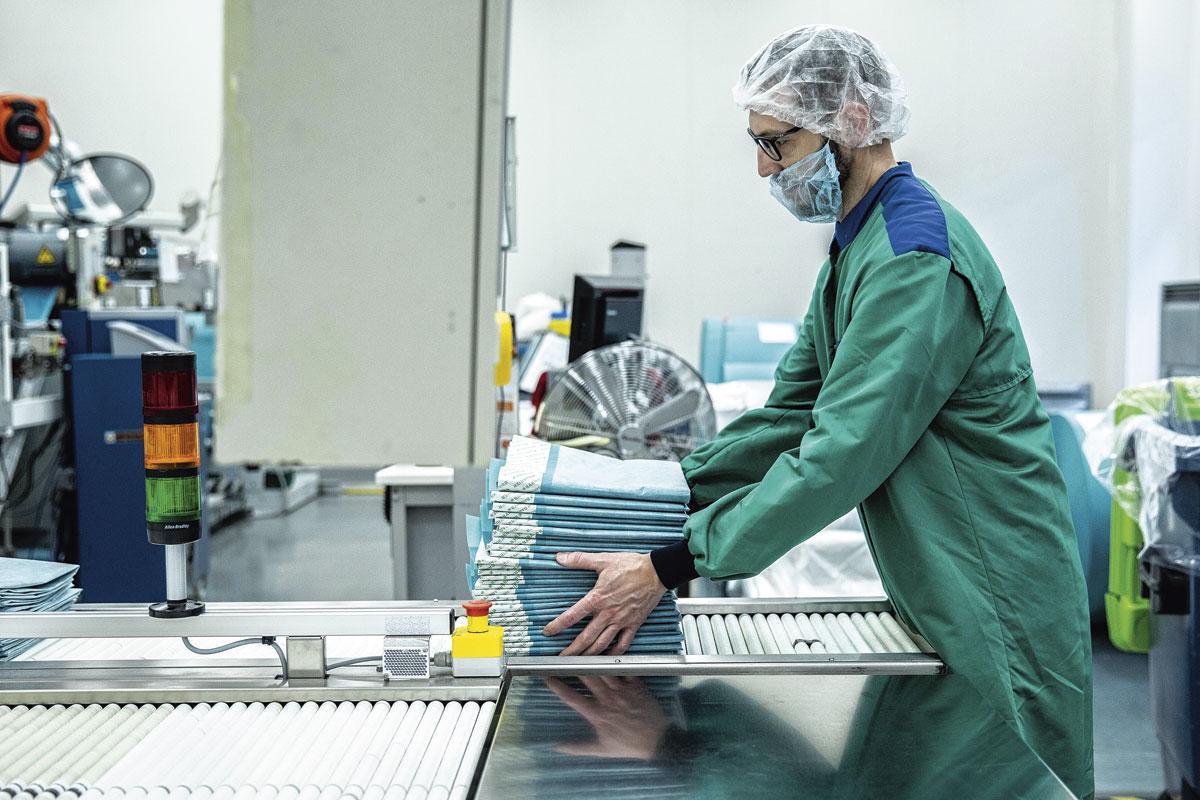
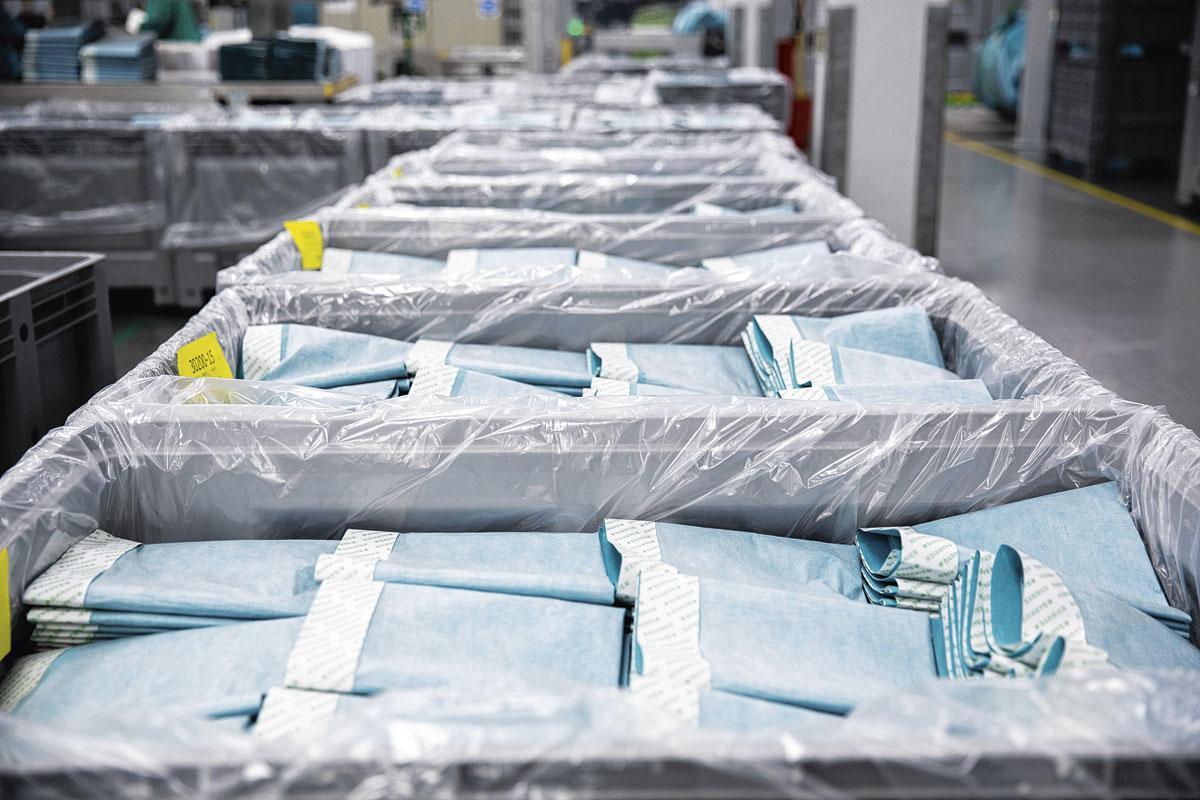
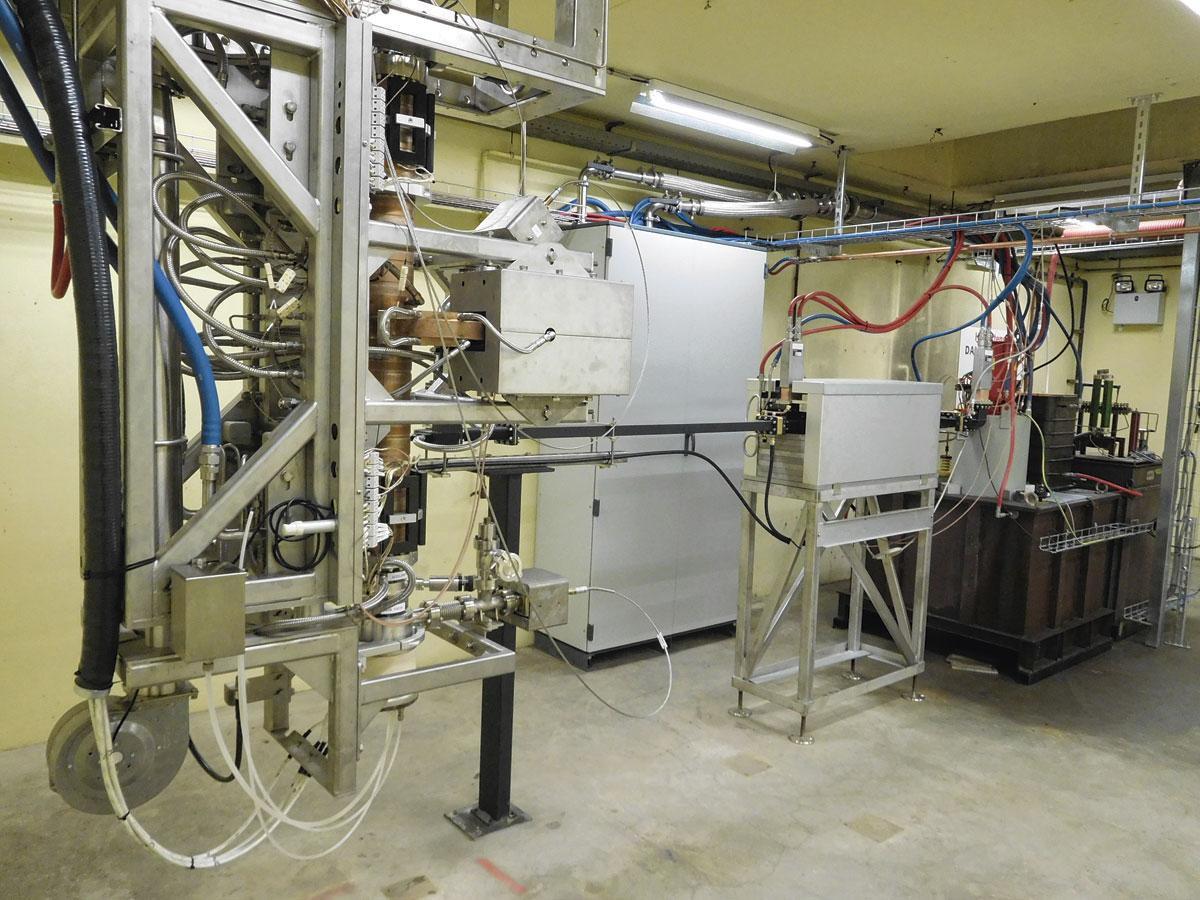
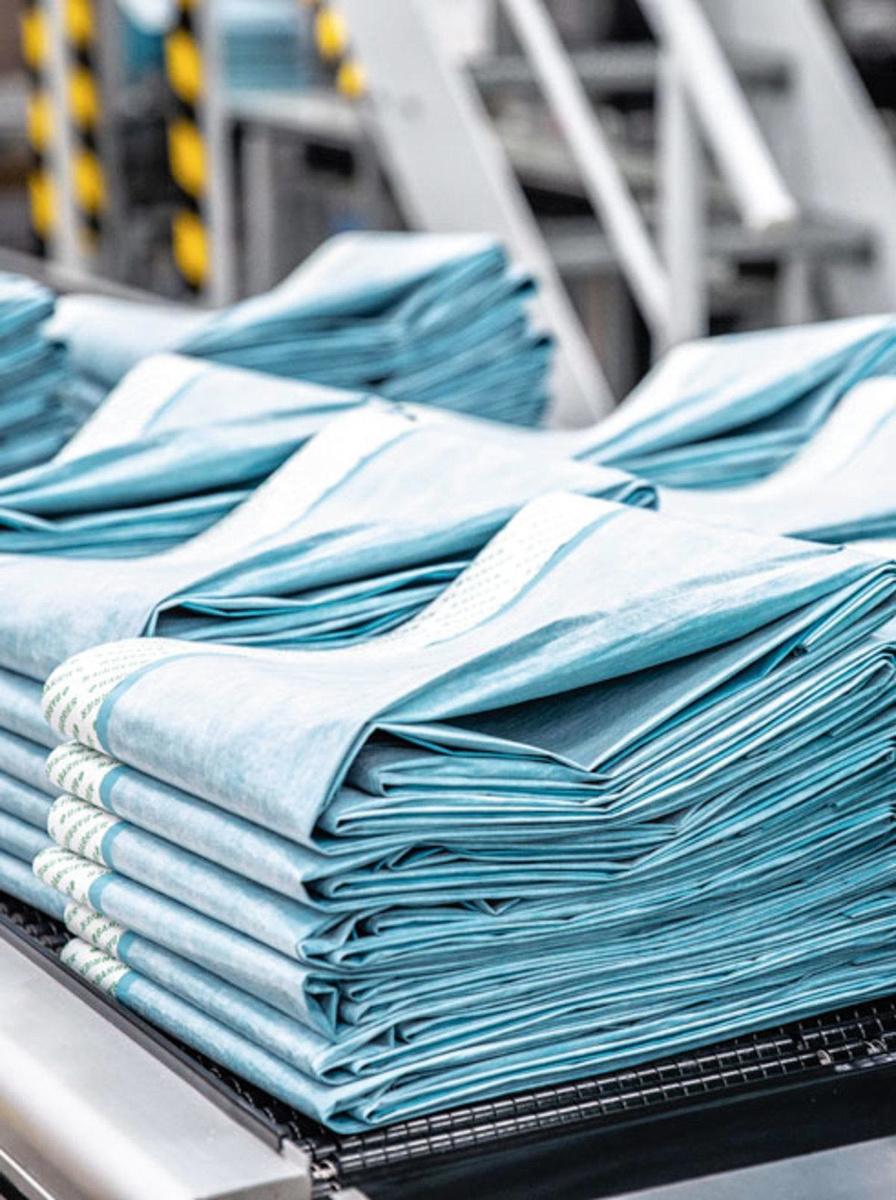