Avec l’envolée des prix du mazout et du gaz, le poêle à pellets connaît un succès grandissant. C’est tout bénéfice pour l’usine Erda, installée à Bertrix, qui compte parmi les plus gros producteurs de pellets en Belgique. Produits et transformés localement, ces granulés de bois compressé sont considérés comme écoresponsables.
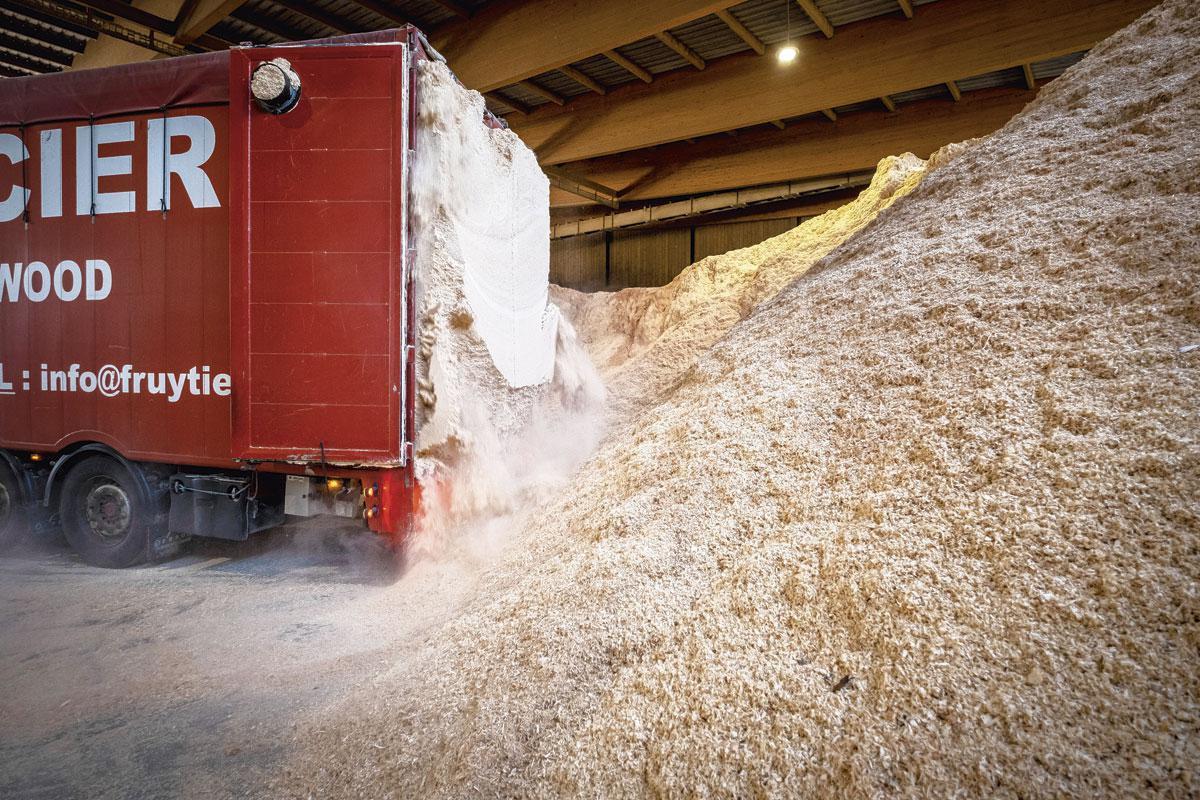
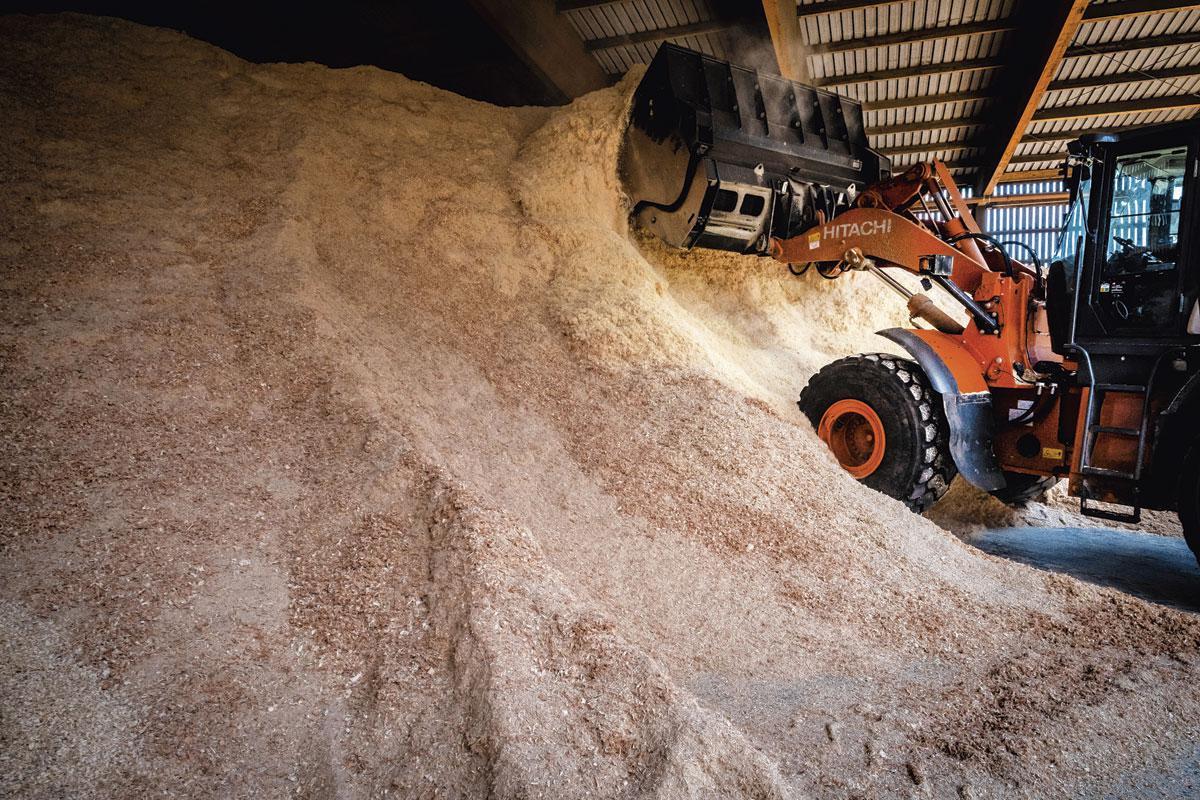
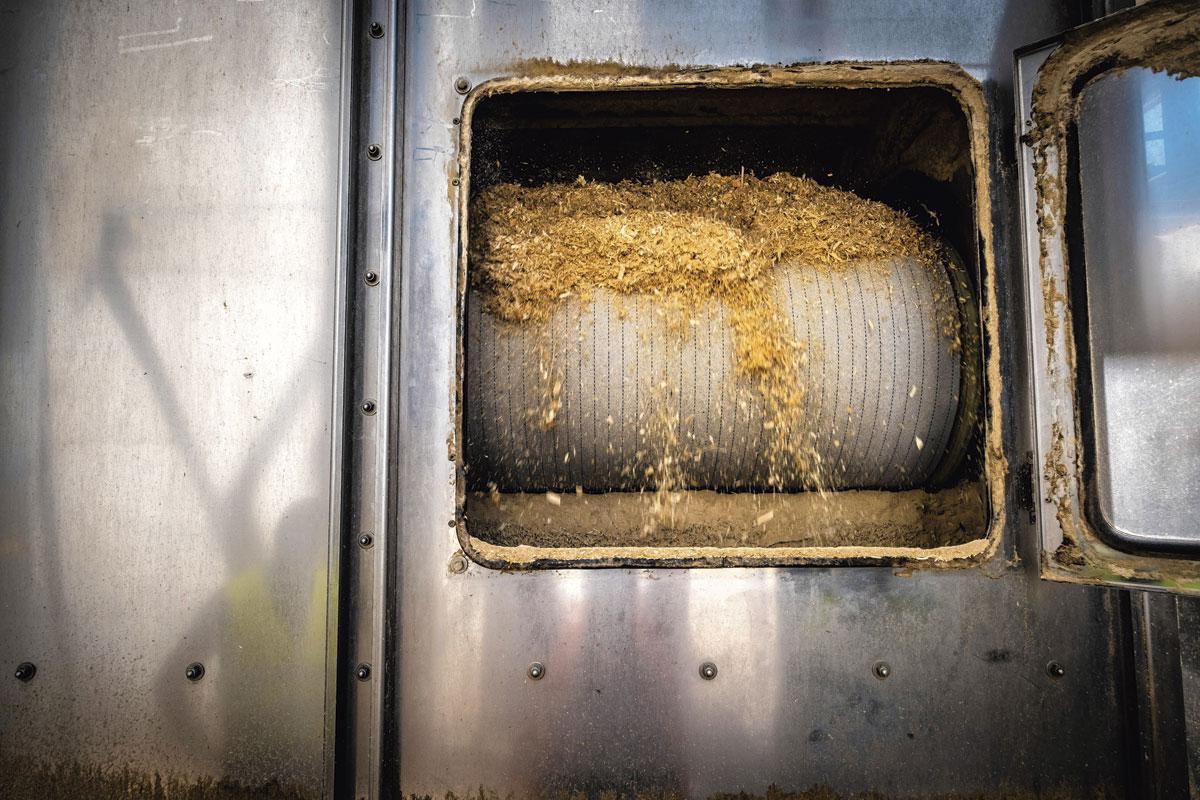
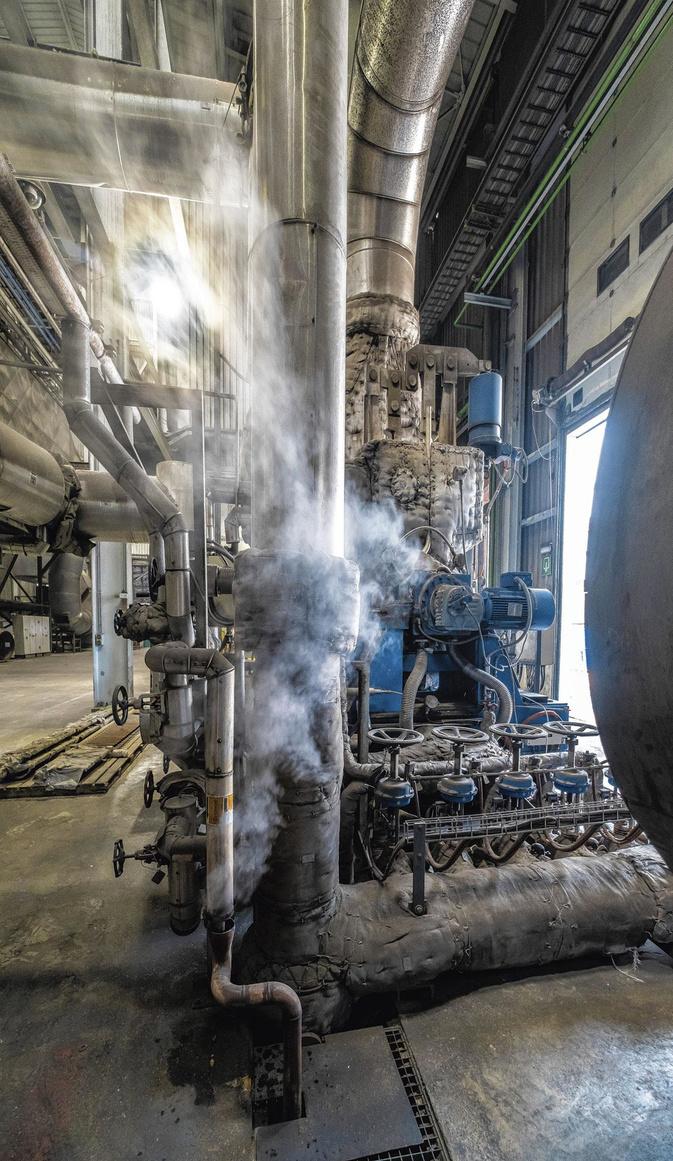
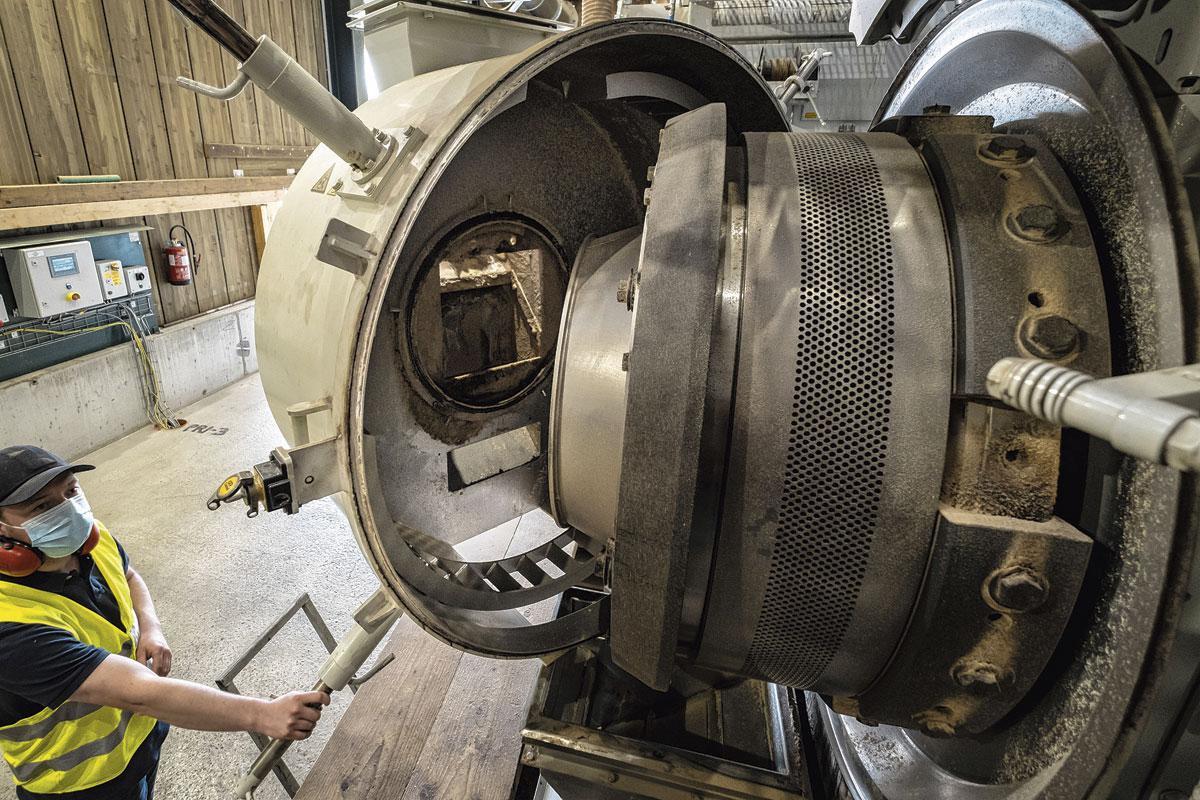
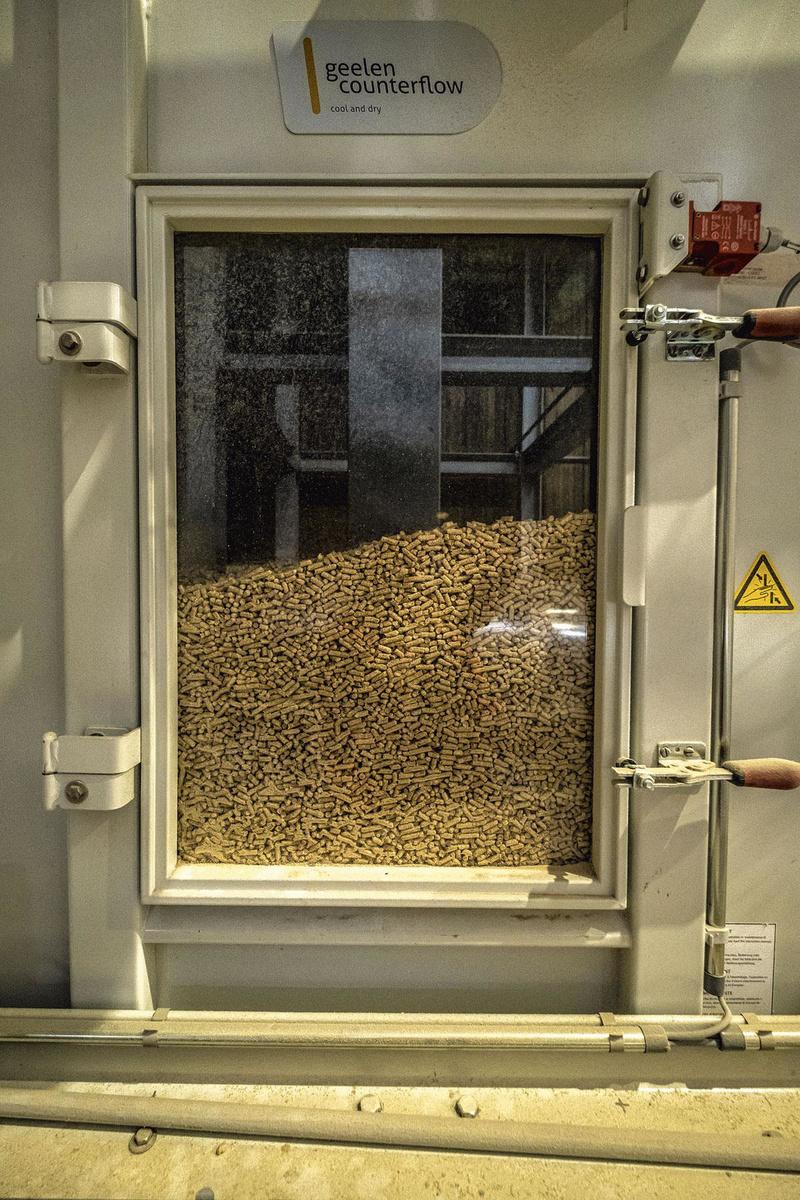
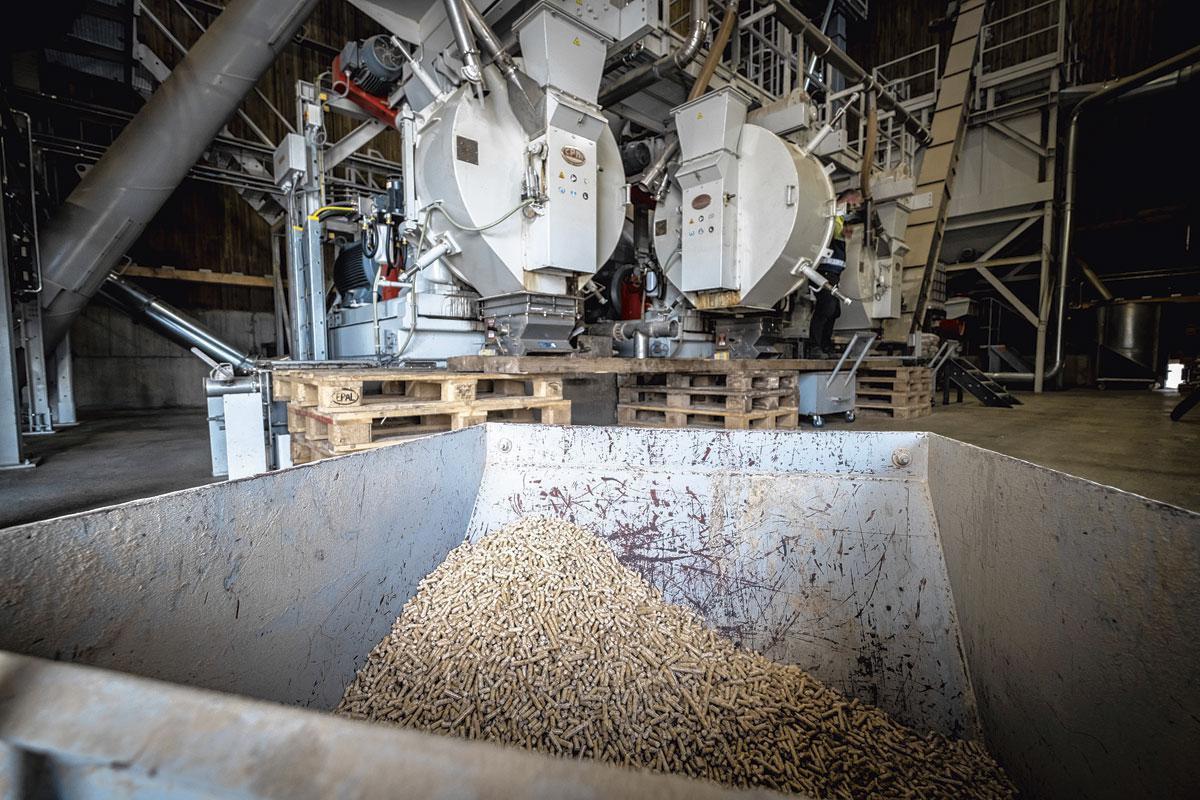
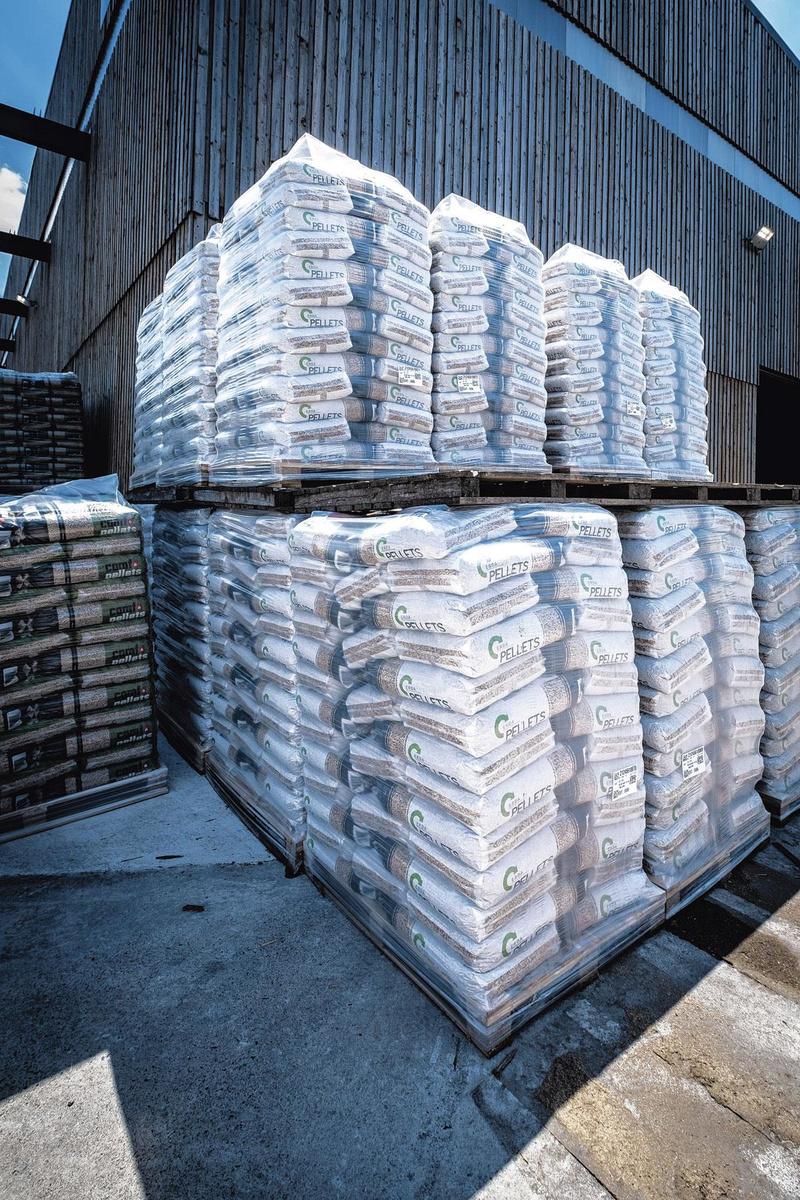
Fruytier, groupe familial spécialisé dans le bois
Jusqu’en 2009, Erda fournissait la centrale de biomasse d’Electrabel. Lorsque celle-ci a fermé, l’entreprise ardennaise s’est tournée vers les particuliers. “Le marché était mûr pour cela, se souvient Stephan Smits, le directeur général. Il était clair que le succès remporté par les pellets en Italie et en France allait s’étendre à la Belgique.” Depuis, les pellets Erda sont également vendus aux Pays-Bas, en Allemagne et en France.
En 2014, Erda intègre le groupe créé par Pierre et Herman Fruytier à Marche-en-Famenne. Autrefois négociant en bois rond, Fruytier s’est diversifié pour devenir une des plus grandes scieries de résineux d’Europe. En quête de plus-value, il est devenu une raboterie, une usine de traitement de déchets de bois, un producteur de bois collé et un bâtisseur de halls logistiques avec des sites à Bertrix, Marche, Vivy (Bouillon), en France et en Allemagne. Le groupe Fruytier a investi 9 millions d’euros sur plusieurs années dans l’usine Erda pour moderniser les séchoirs et les presses et faire passer la capacité à 200.000 tonnes par an. De quoi chauffer 200.000 maisons.
Erda joue la carte du développement durable. “Nous n’utilisons que des chutes de bois issus de forêts locales, précise Stephan Smits. Chaque arbre abattu est remplacé. Notre processus de production, de même que la combustion des pellets chez les clients, sont neutres en CO2. La quantité de CO2 libérée est identique à celle que les déchets produiraient si on les laissait pourrir et se transformer en compost sur place.” Erda, qui produit aussi de l’électricité par cogénération et dispose de certificats verts, doit aux pellets 75% de ses 32 millions d’euros de chiffre d’affaires.