Le nouveau vaccin anti-covid a été mis au point en moins d’un an. On en oublierait presque à quel point le processus est complexe. La production du Shingrix, le vaccin le plus récent de GSK – rien à voir avec le coronavirus – témoigne de toute la difficulté de sortir un vaccin biologique.
Le plus grand centre de production de vaccins du monde
La Belgique est devenue un eldorado pharmaceutique pour le développement et la production des vaccins, entre autres contre le coronavirus, grâce au cadre innovant mis en place par les autorités, à notre situation centrale en Europe et aux synergies entre les universités, les hôpitaux et des entreprises comme Johnson & Johnson ou GSK. Le pays abrite même le plus grand centre de production de vaccins du monde. A Wavre, le groupe britannique GlaxoSmithKline (GSK) produit l’adjuvant pour trois candidats vaccins contre le coronavirus (Sanofi, Medicago et SK Bioscience) et une trentaine d’autres destinés à éradiquer des maladies comme la polio. Le site participe également à la production du vaccin ARNm de Curevac. La division belge de GSK emploie pas moins de 9.000 personnes, de 80 nationalités différentes.
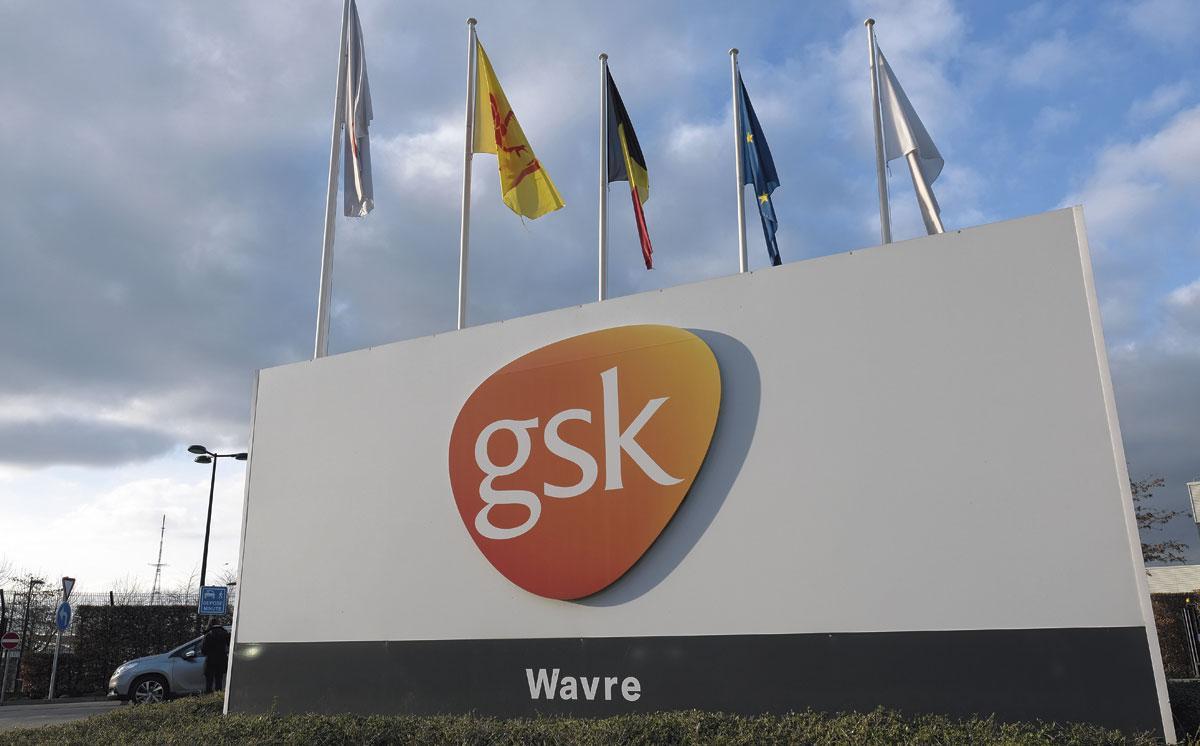
Le site historique de Rixensart est, lui, entièrement dédié à la recherche. Au total, avec les tests cliniques, les contrôles et l’enregistrement, il faut compter 14 ans pour développer un vaccin, voire 28 ans dans le cas du Shingrix. Plus de deux millions de vaccins sont envoyés par jour vers 162 Etats. En 2020, 580 millions de doses ont été dispatchées, dont 70% vers les pays en voie de développement. Les prix sont calculés en fonction de la capacité financière de chaque Etat. L’expertise vaccinale de GSK remonte à Piet De Somer, professeur et recteur de l’université de Louvain, qui a développé et produit un des premiers vaccins contre la polio dans les années 1940. Plusieurs fusions ont permis à GSK de devenir le grand groupe pharmaceutique que nous connaissons aujourd’hui.
1. Sous stricte surveillance
Le vaccin contre le zona, sujet de ce reportage, est le dernier succès en date de GSK. Il prévient les éruptions cutanées douloureuses qui apparaissent chez les personnes âgées, principalement la fameuse “ceinture de feu” à hauteur du thorax. Sa mise au point a duré 30 ans. A Wavre, GSK Vaccin emploie pas moins de 7.000 personnes sur une superficie équivalente à 70 terrains de football. Chaque unité produit un antigène entrant dans la préparation de différents vaccins. Le site est sous haute surveillance: caméras, portiques d’accès, agents de sécurité…
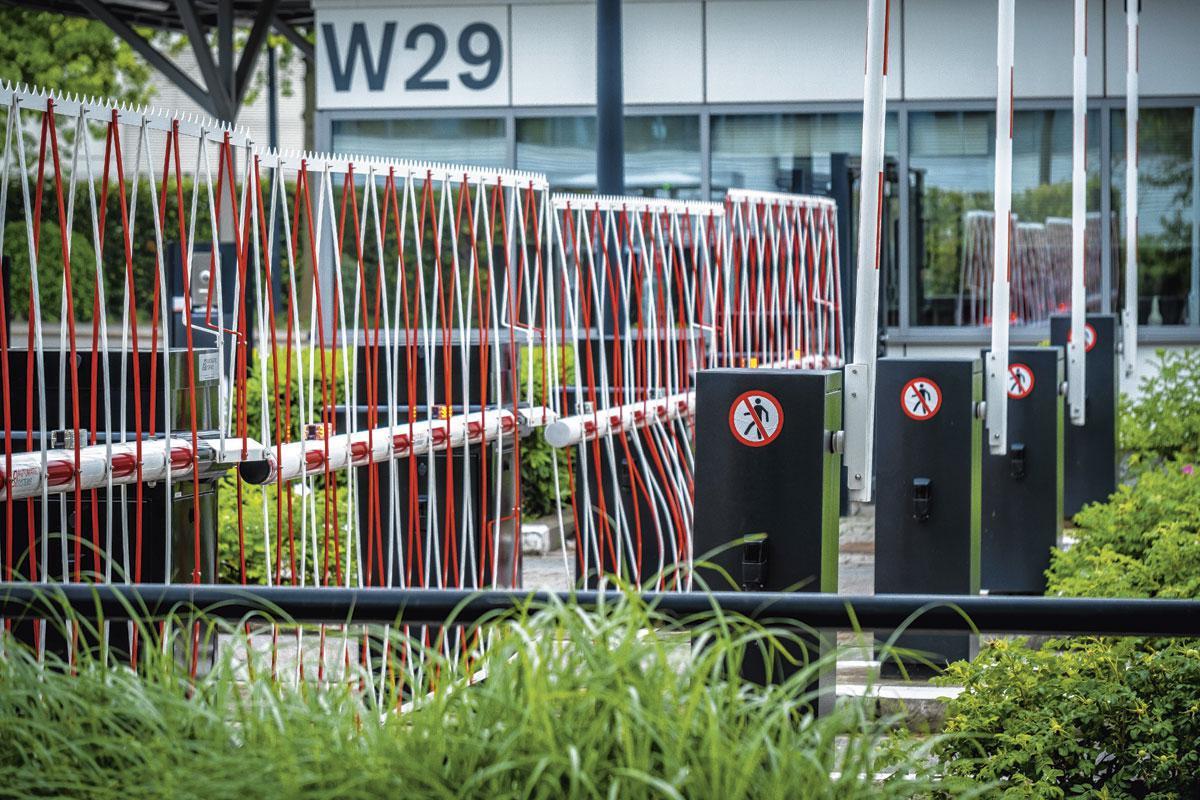
2. A chacun sa combinaison
Personne ne pénètre dans une unité de production sans d’abord passer au vestiaire. Seuls les collaborateurs spécialement formés ont accès aux locaux stériles dédiés à la manipulation d’organismes vivants. Le protocole d’habillage/déshabillage est strict ou très strict selon la zone. Les combinaisons vertes, avec gants, masque facial et lunettes sont obligatoires dans les zones les plus sécurisées. Les combinaisons bleu clair conviennent pour les zones moins risquées, et les blanches pour le département emballage.
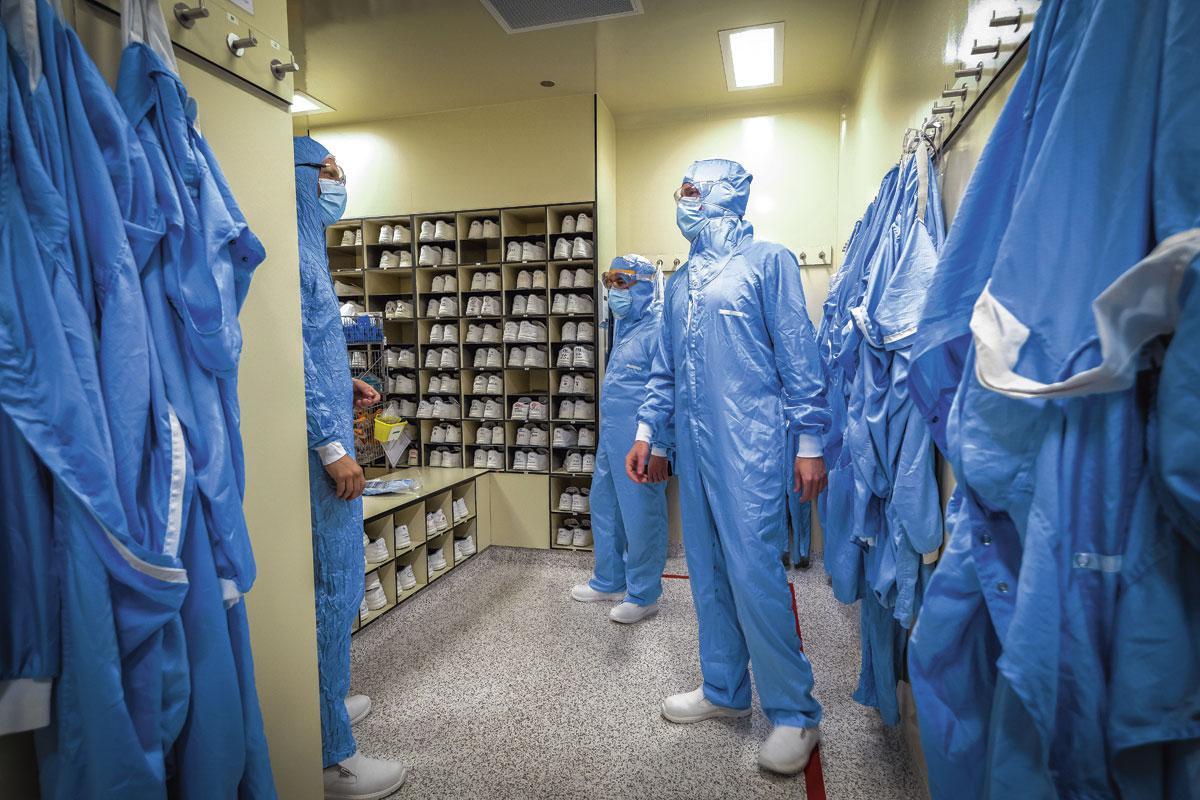
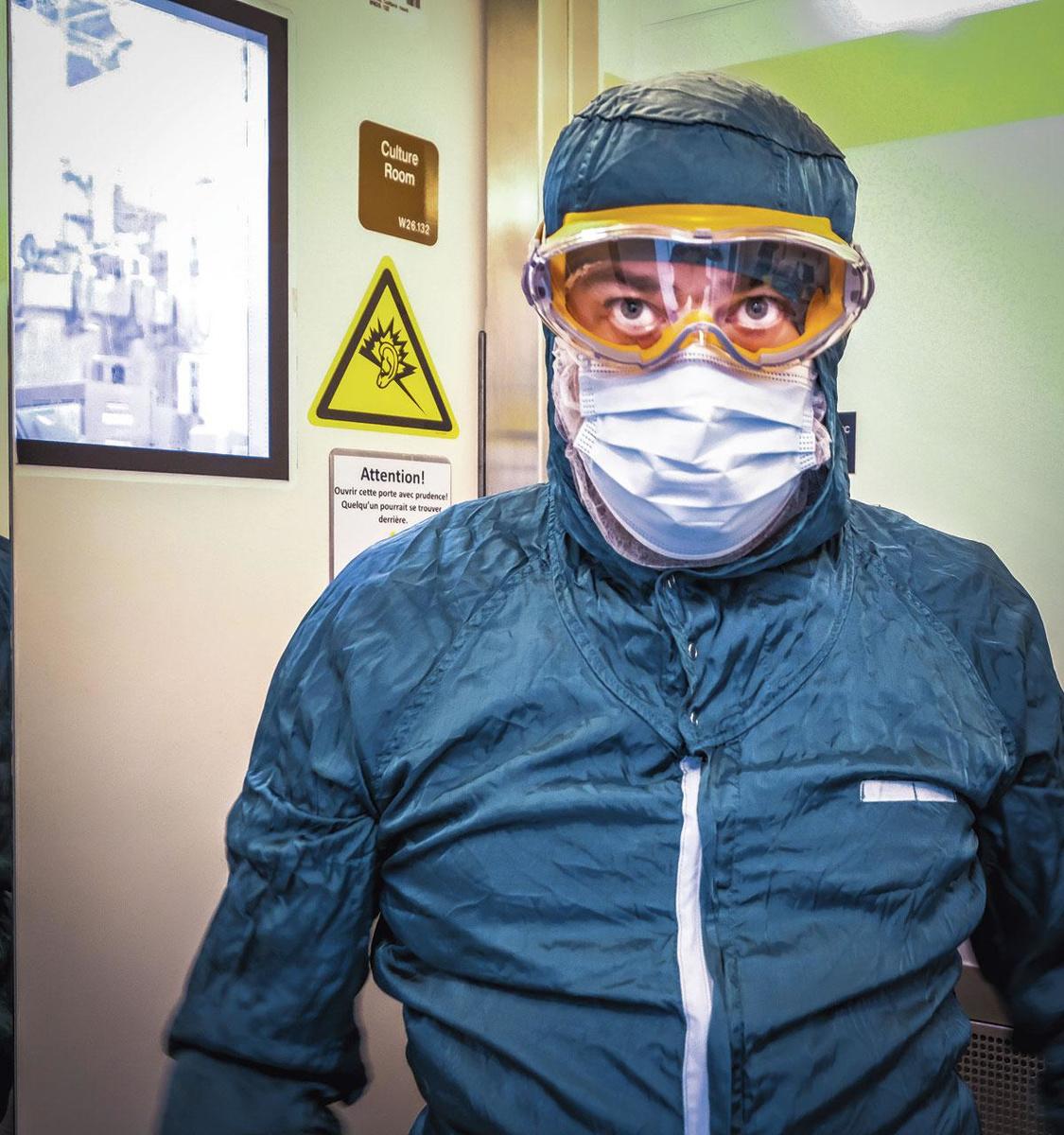
3. Plusieurs lignes de production
Le vaccin contre le zona contient un antigène, produit par technologie recombinante dans les cellules, et un adjuvant. Ce dernier est un mélange d’extraits de plantes et de graisses, pour une meilleure réponse du système immunitaire humain et une protection prolongée.
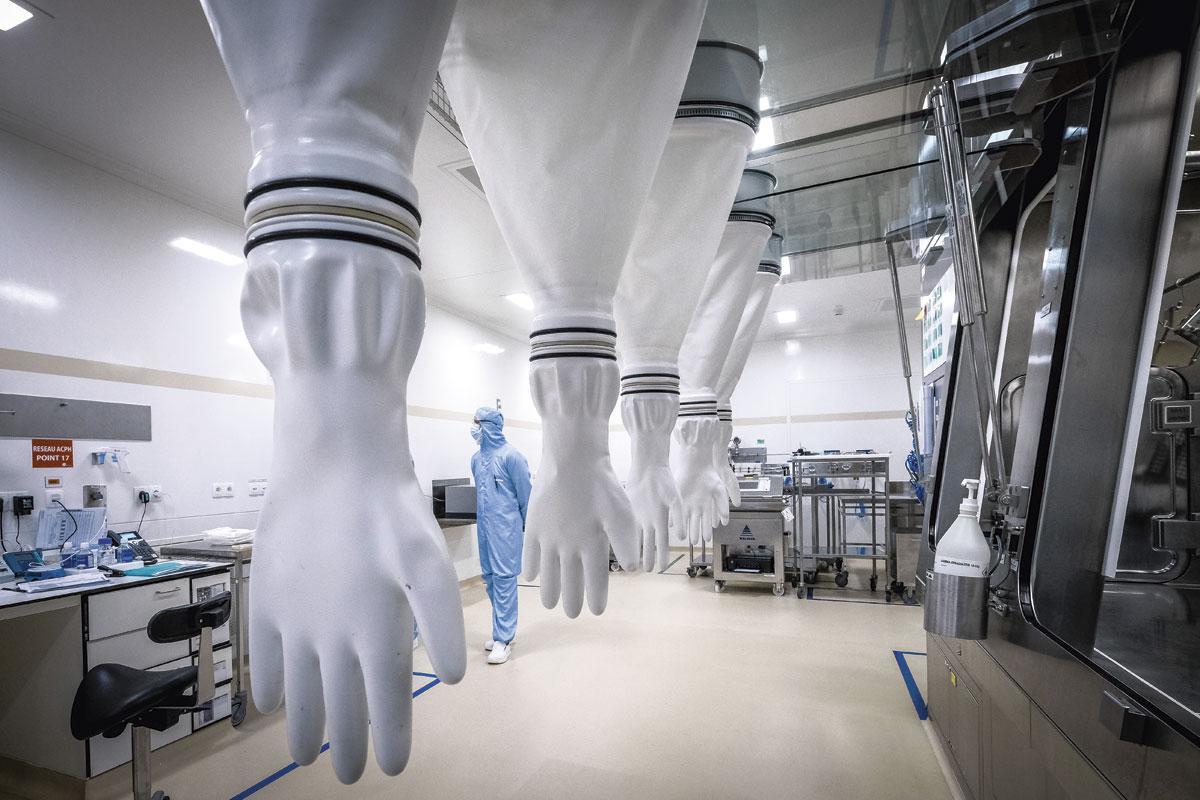
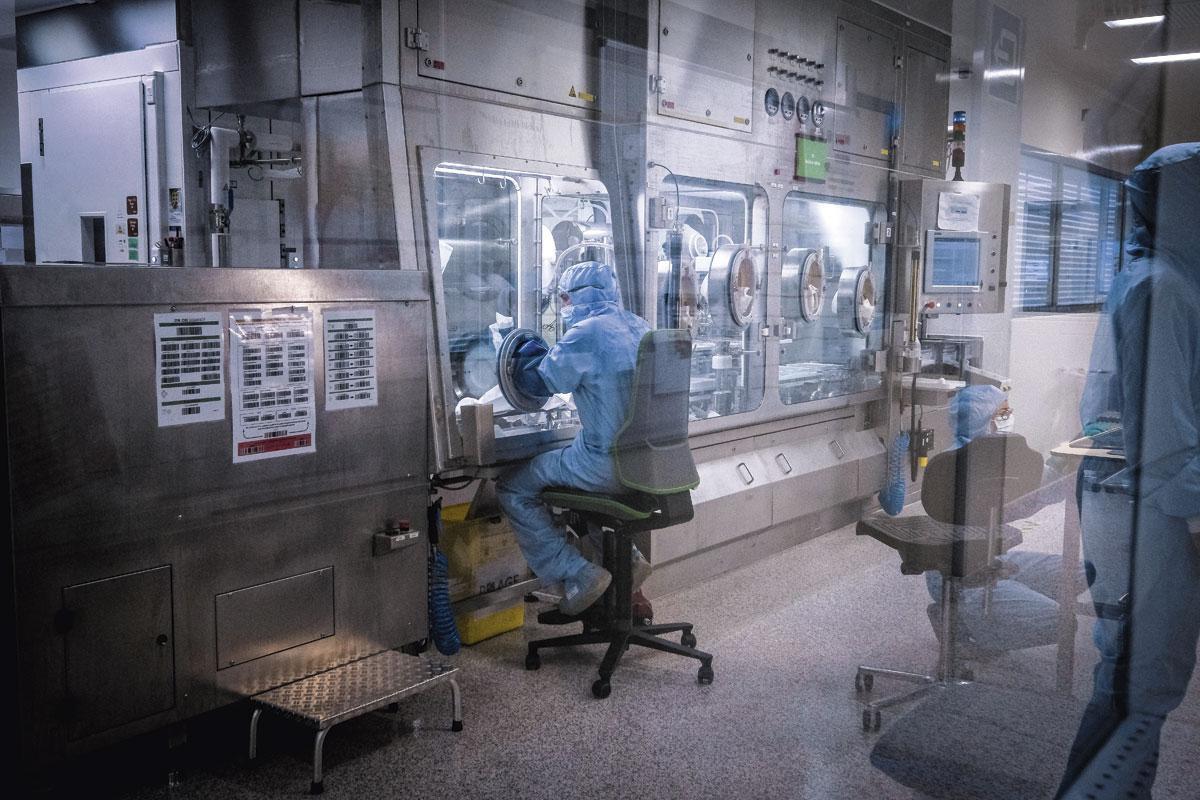
4. Production d’antigènes
Pendant plusieurs semaines, l’équivalent de moins d’une cuillère à thé des fameuses protéines antigènes, en provenance du labo, est cultivé dans un bioréacteur. Jusqu’à produire 600 litres de cellules actives au final. Le processus, entièrement automatisé, nécessite un environnement très contrôlé: température, pression de l’air, humidité ambiante.
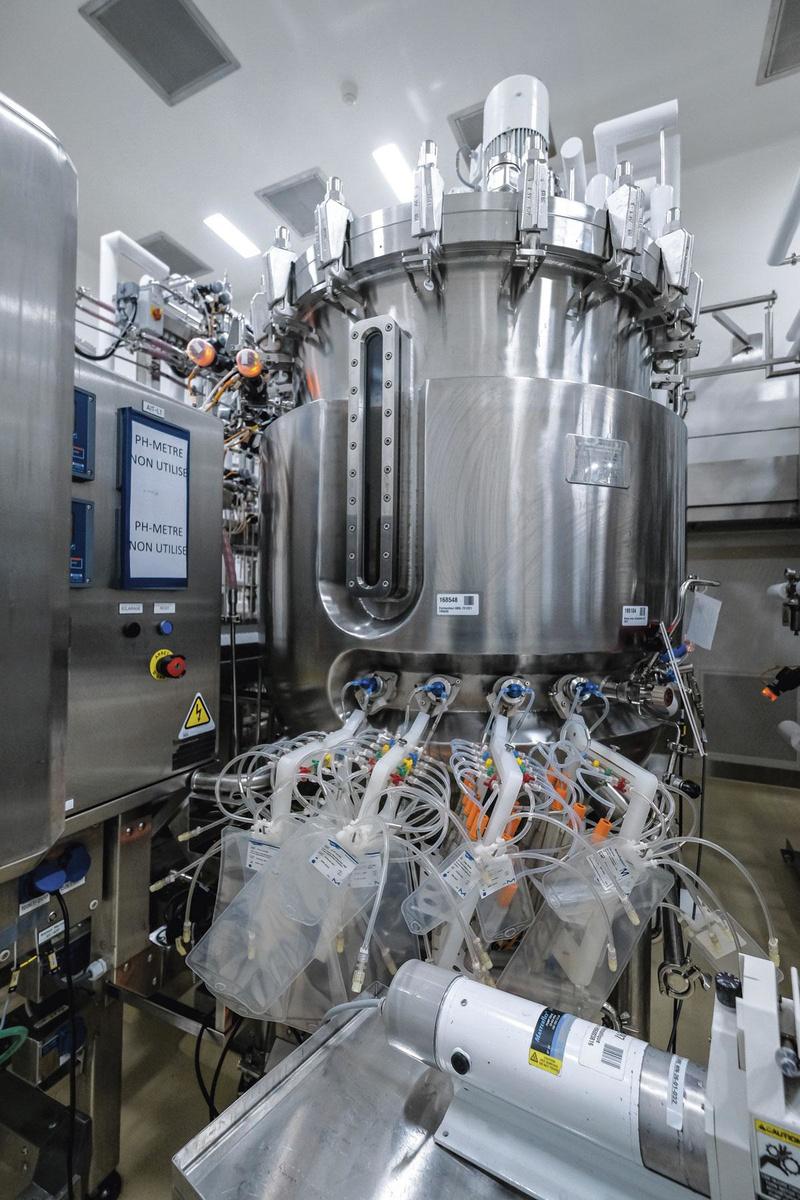
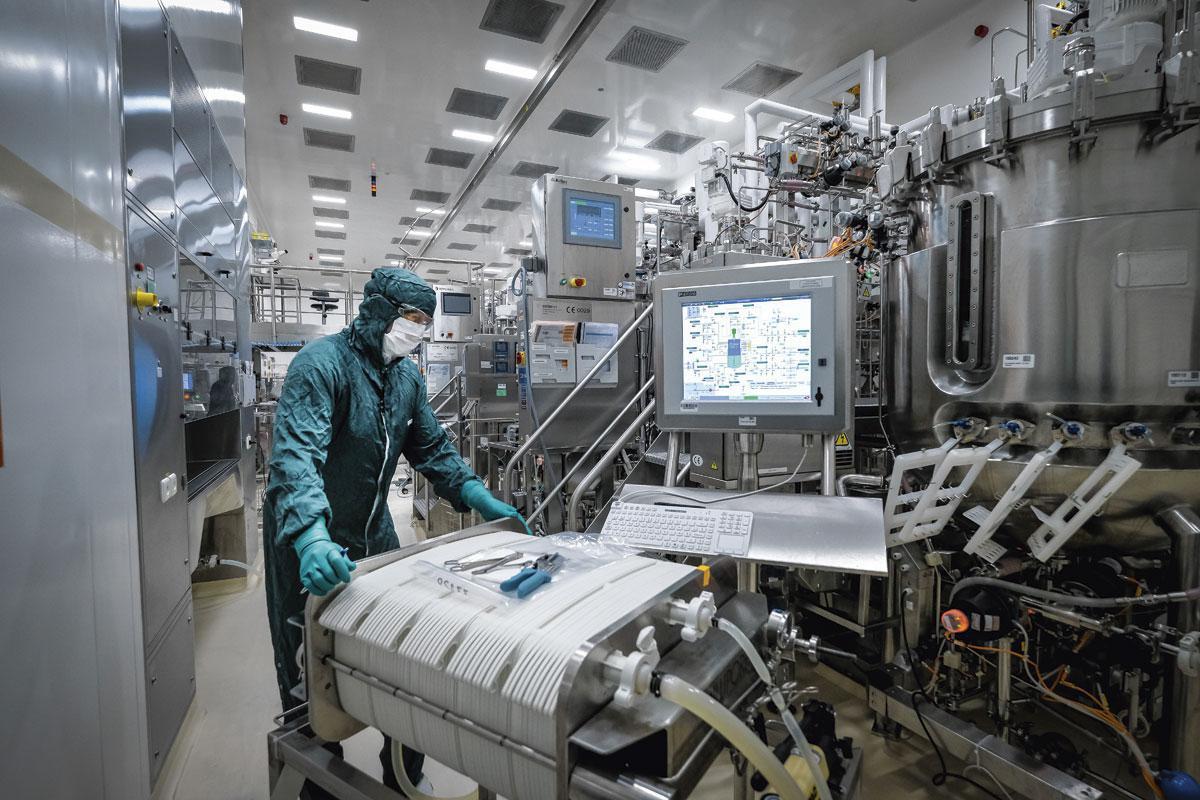
5. Filtrage et formulation
Les antigènes sont ensuite séparés par filtration, épurés et conservés à -5° C, puis concentrés dans des flacons et stockés dans un congélateur à -45° C. De là, ils sont transférés à l’unité formulation où s’opère le mélange des antigènes avec d’autres substances.
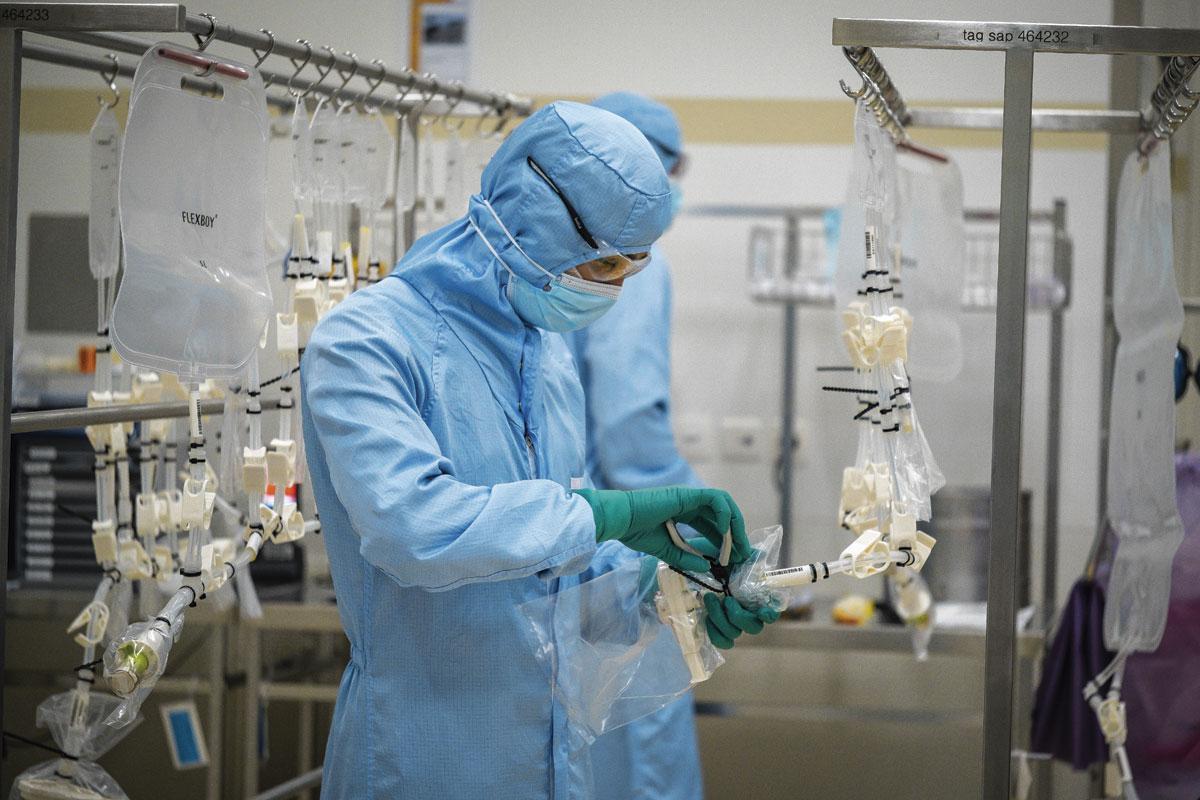
6. Remplissage des flacons
Une fois le mélange prêt, la préparation est acheminée vers les remplisseuses. Des millions de flacons sont remplis de quelques millilitres de protéines actives. Elles sont généralement prêtes à l’emploi. Ou lyophilisées comme pour le vaccin contre le zona. Les vaccins lyophilisés se conservent plus facilement et plus longtemps.
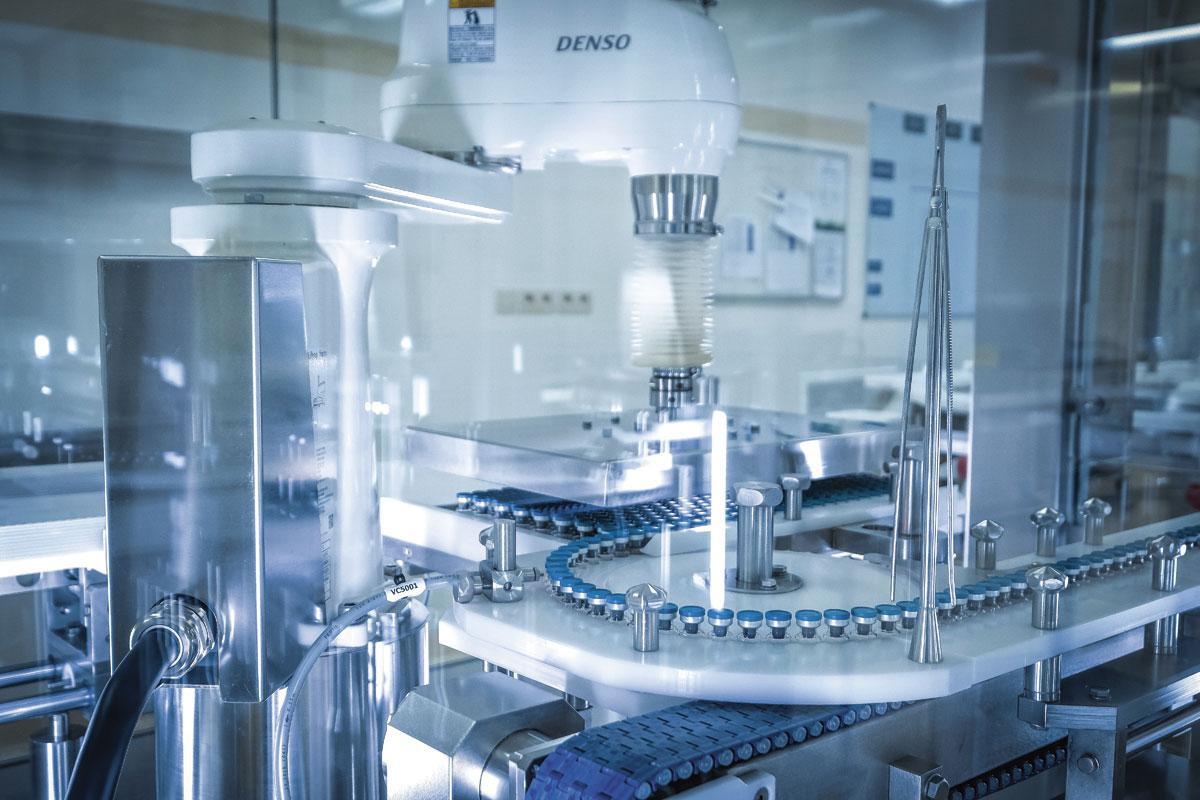
7. Contrôle
Le processus de contrôle, assuré à chaque étape, représente 70% de la durée totale de production. A la fin, chaque flacon est soumis au test du rayon lumineux avant son conditionnement. Les flacons non conformes sont automatiquement éliminés. Ailleurs dans le bâtiment, une dizaine de contrôleurs qualité sont assis devant des écrans noirs et blancs dans un silence religieux. Ils retournent le flacon dans tous les sens et l’inspectent visuellement. Pour assurer un maximum de concentration, une pause de 5 minutes est observée après chaque contrôle intensif de 30 minutes.
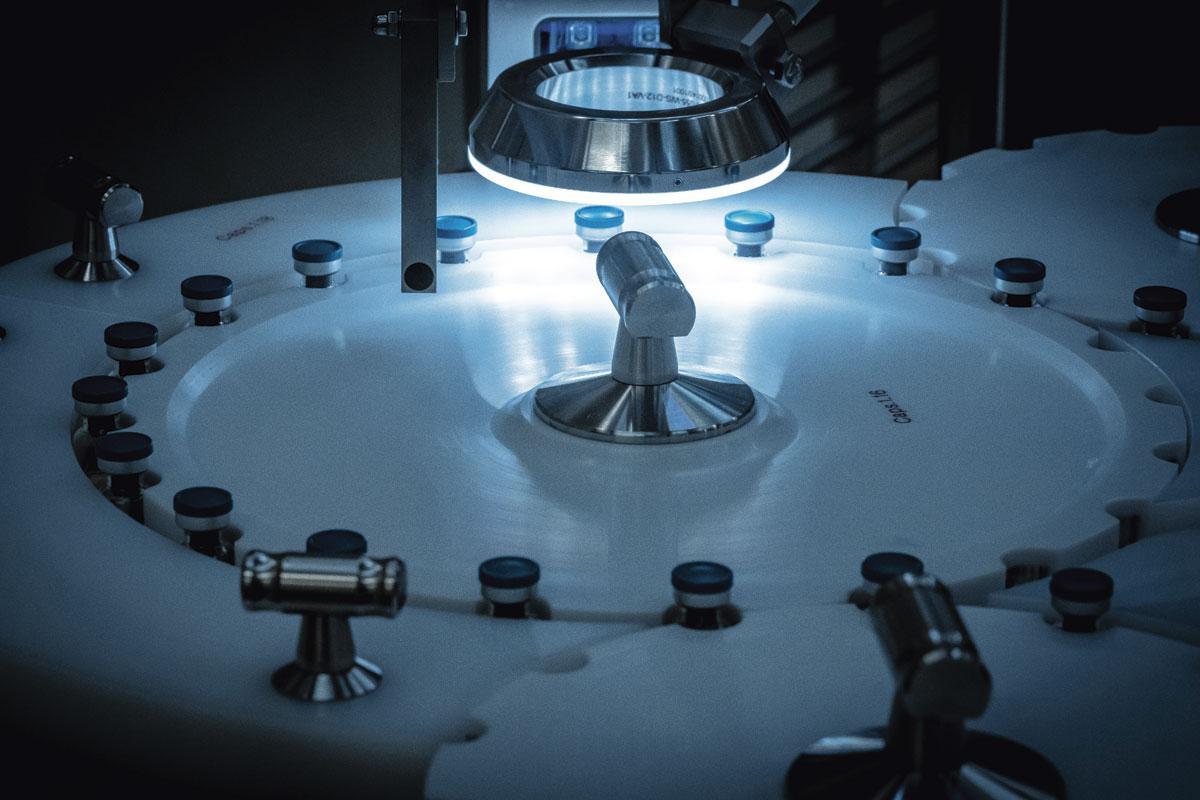
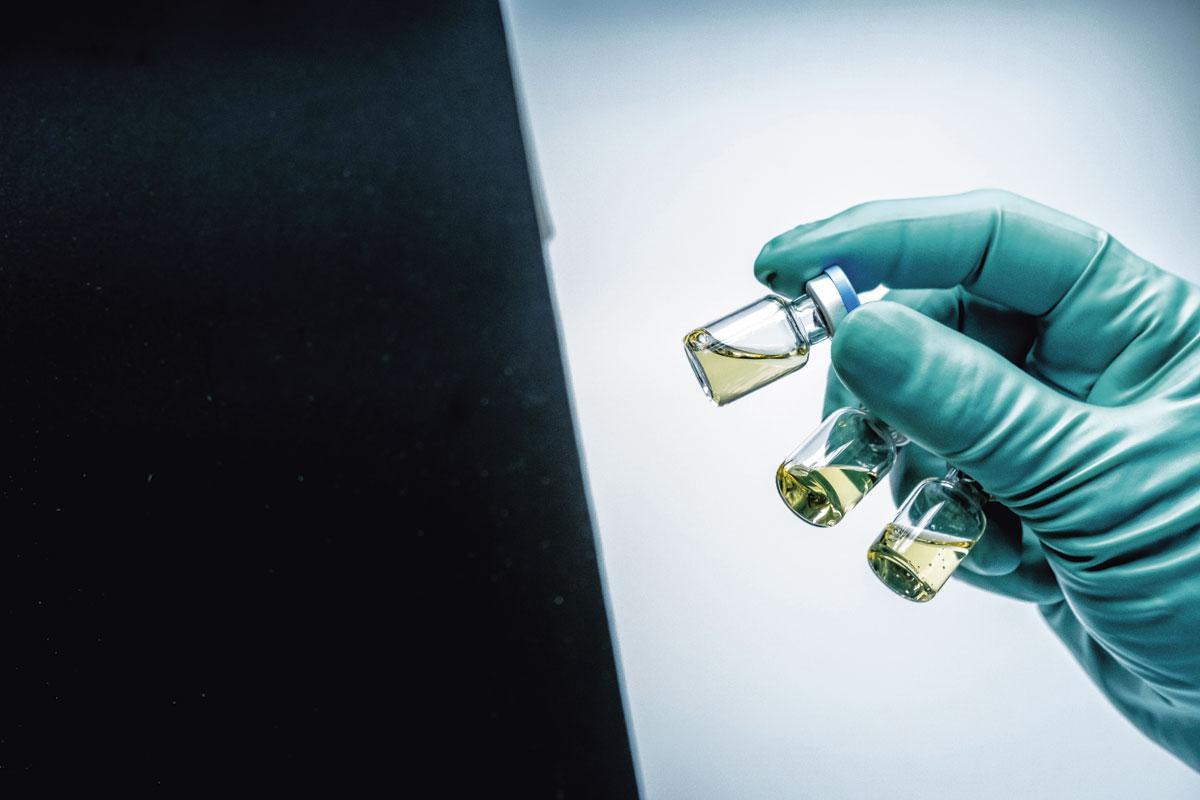
8. Emballage
L’adjuvant et la substance active (les antigènes) sont finalement réunis et emballés conformément aux exigences du pays de destination. Pour chaque ligne de conditionnement, une dizaine de collaborateurs préparent les matériaux de conditionnement et formatent les machines.
